Injection molding is a widely used manufacturing process for producing plastic parts, and the choice between a 2-plate and 3-plate mold design significantly impacts the production process, part quality, and cost. The primary difference lies in the mold structure, gating system, and ejection mechanism. A 2-plate mold is simpler and more cost-effective, typically using side gates for feeding material into the cavity. In contrast, a 3-plate mold is more complex, allowing for pinpoint gating at any location in the cavity, which is particularly useful for intricate designs or large parts with central holes. This flexibility makes 3-plate molds ideal for high-precision applications but comes at a higher cost and complexity.
Key Points Explained:
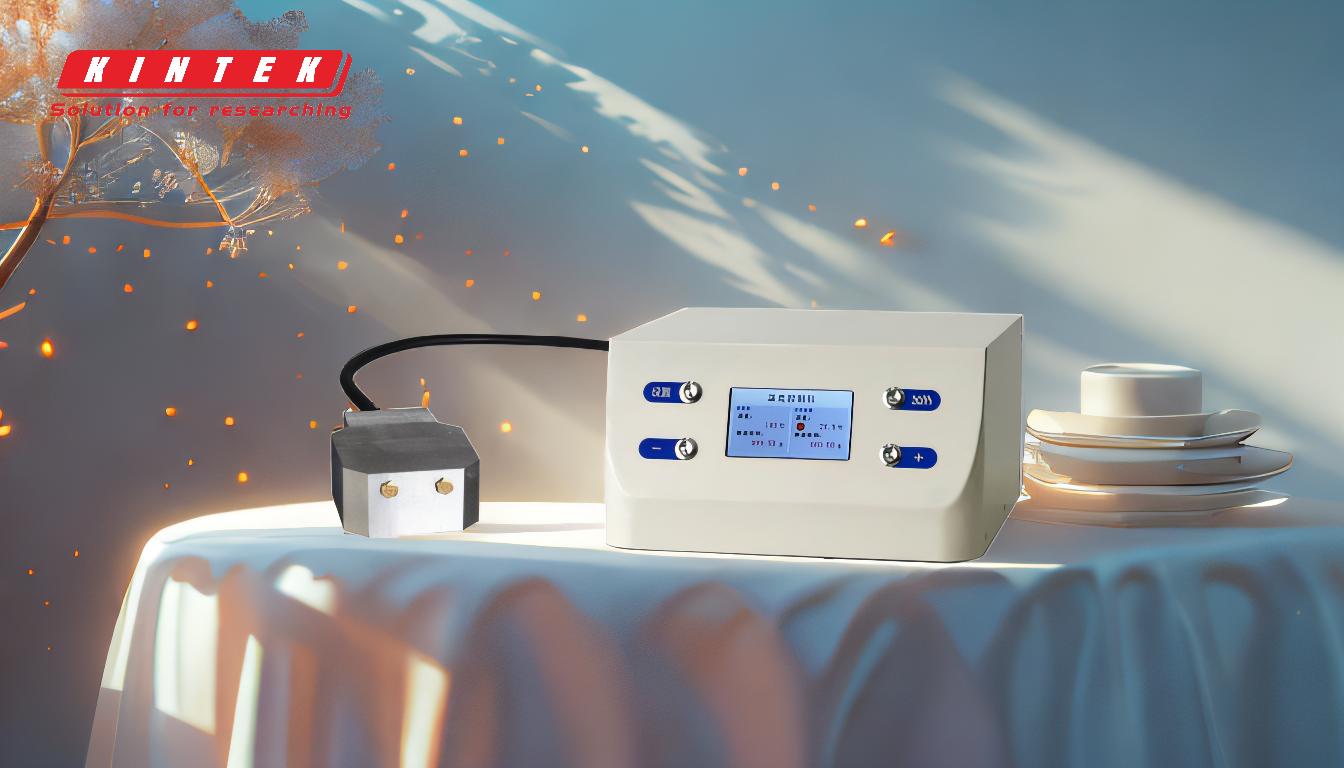
-
Mold Structure:
- 2-Plate Mold: Consists of two main plates—the cavity plate and the core plate. This design is simpler and more straightforward, making it easier to manufacture and maintain.
- 3-Plate Mold: Includes an additional plate (the runner plate) between the cavity and core plates. This extra plate allows for more complex gating systems and better control over material flow.
-
Gating System:
- 2-Plate Mold: Typically uses side gates, which feed material into the cavity from the outer edge. This is suitable for simpler parts but may leave visible gate marks.
- 3-Plate Mold: Allows for pinpoint gating, enabling material to be injected at any point in the cavity. This is ideal for complex parts or those requiring high precision, as it minimizes gate marks and allows for better material distribution.
-
Ejection Mechanism:
- 2-Plate Mold: The ejection mechanism is simpler, usually involving ejector pins that push the part out of the mold after cooling.
- 3-Plate Mold: The additional runner plate complicates the ejection process, often requiring a more sophisticated system to separate the part from the runner and gate.
-
Applications:
- 2-Plate Mold: Best suited for simpler parts where cost and ease of manufacturing are primary concerns. Commonly used in high-volume production of less complex items.
- 3-Plate Mold: Ideal for complex parts, large items, or those requiring precise material placement. Often used in applications where part quality and precision are critical, such as in medical devices or automotive components.
-
Cost and Complexity:
- 2-Plate Mold: Generally less expensive and easier to design and manufacture. Lower maintenance costs and simpler operation make it a cost-effective choice for many applications.
- 3-Plate Mold: More expensive due to the additional plate and more complex gating and ejection systems. Higher maintenance and operational costs, but justified for high-precision or complex parts.
-
Material Efficiency:
- 2-Plate Mold: May result in more material waste due to the side gating system, which can leave larger gate marks and require more trimming.
- 3-Plate Mold: More material-efficient, as pinpoint gating minimizes waste and allows for better control over material distribution, reducing the need for post-processing.
In summary, the choice between a 2-plate and 3-plate injection mold depends on the complexity of the part, the required precision, and budget constraints. While 2-plate molds are simpler and more cost-effective, 3-plate molds offer greater flexibility and precision, making them suitable for more demanding applications.
Summary Table:
Feature | 2-Plate Mold | 3-Plate Mold |
---|---|---|
Mold Structure | 2 plates (cavity & core) | 3 plates (cavity, runner, & core) |
Gating System | Side gates | Pinpoint gating |
Ejection Mechanism | Simpler, ejector pins | More complex, advanced systems |
Applications | Simpler parts, high-volume production | Complex parts, high-precision needs |
Cost & Complexity | Lower cost, simpler design | Higher cost, more complex design |
Material Efficiency | More waste, larger gate marks | Less waste, minimal gate marks |
Need help choosing the right injection mold for your project? Contact our experts today for personalized advice!