The primary difference between a 2-plate and a 3-plate mold lies in their design, gating systems, and applications. A 2-plate mold is simpler, typically using side gates for feeding material into the cavity from the outer side, making it suitable for straightforward parts. In contrast, a 3-plate mold is more complex, allowing for pinpoint gating at any point in the cavity, which is ideal for intricate designs or parts requiring multiple gates. The 3-plate mold also separates the runner system from the part, enabling more flexibility in gating locations and better control over material flow. Both molds have distinct advantages depending on the product requirements.
Key Points Explained:
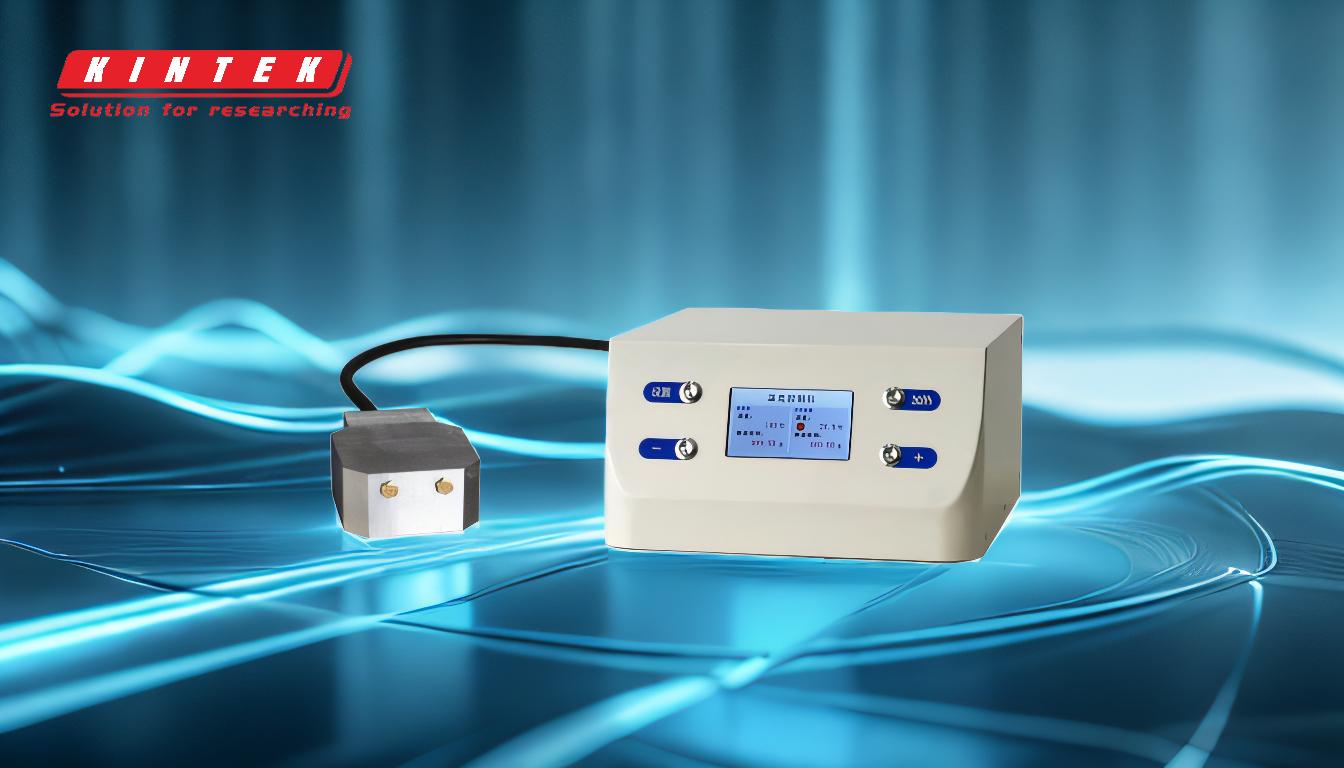
-
Design Complexity:
- 2-Plate Mold: This design consists of two main plates: the cavity plate and the core plate. It is simpler and easier to manufacture, making it cost-effective for straightforward parts.
- 3-Plate Mold: This design includes an additional plate between the cavity and core plates, separating the runner system from the part. The added complexity allows for more precise gating and ejection mechanisms.
-
Gating Systems:
- 2-Plate Mold: Typically uses side gates, which feed material into the cavity from the outer side. This is suitable for parts that do not require intricate gating or multiple injection points.
- 3-Plate Mold: Allows for pinpoint gates, which can be placed at any point in the cavity. This flexibility is beneficial for complex parts requiring multiple gates or precise material flow control.
-
Applications:
- 2-Plate Mold: Best suited for simple parts with minimal gating requirements. It is commonly used for products that do not have large holes or intricate designs in the center.
- 3-Plate Mold: Ideal for complex parts with large holes or intricate designs in the center. The ability to gate from any point in the cavity makes it versatile for a wide range of applications.
-
Material Flow and Control:
- 2-Plate Mold: The material flow is generally straightforward, with less control over the injection points. This can lead to issues like weld lines or uneven material distribution in complex parts.
- 3-Plate Mold: Offers better control over material flow, reducing the risk of defects. The separation of the runner system from the part allows for more precise injection and ejection.
-
Cost and Maintenance:
- 2-Plate Mold: Generally less expensive to manufacture and maintain due to its simpler design. It is a cost-effective solution for high-volume production of simple parts.
- 3-Plate Mold: More expensive to produce and maintain due to its complexity. However, the added cost can be justified for parts requiring precise gating and material control.
-
Ejection Mechanism:
- 2-Plate Mold: The ejection mechanism is straightforward, often using ejector pins to push the part out of the mold.
- 3-Plate Mold: The additional plate allows for more complex ejection mechanisms, which can be beneficial for parts with intricate designs or multiple undercuts.
In summary, the choice between a 2-plate and a 3-plate mold depends on the complexity of the part, the required gating system, and the level of control needed over material flow. While 2-plate molds are simpler and more cost-effective for straightforward parts, 3-plate molds offer greater flexibility and precision for complex designs.
Summary Table:
Feature | 2-Plate Mold | 3-Plate Mold |
---|---|---|
Design Complexity | Simpler design, 2 main plates | More complex, 3 plates with runner separation |
Gating System | Side gates for outer cavity feeding | Pinpoint gates for precise material flow |
Applications | Best for simple parts | Ideal for complex, intricate designs |
Material Control | Less control, potential for defects | Better control, reduced risk of defects |
Cost & Maintenance | Lower cost, easier maintenance | Higher cost, more complex maintenance |
Ejection Mechanism | Straightforward ejector pins | Complex mechanisms for intricate parts |
Need help choosing the right mold for your project? Contact our experts today for personalized advice!