Ball mills and rod mills are both grinding equipment used in various industries, but they differ in their design, operation, and applications. A ball mill uses rotating balls to grind materials into fine powders, making it suitable for materials like ore, ceramics, and paint. On the other hand, a rod mill uses long cylindrical rods as the grinding medium, which is more effective for coarse grinding and avoids over-grinding. The choice between the two depends on the material properties, desired particle size, and specific application requirements.
Key Points Explained:
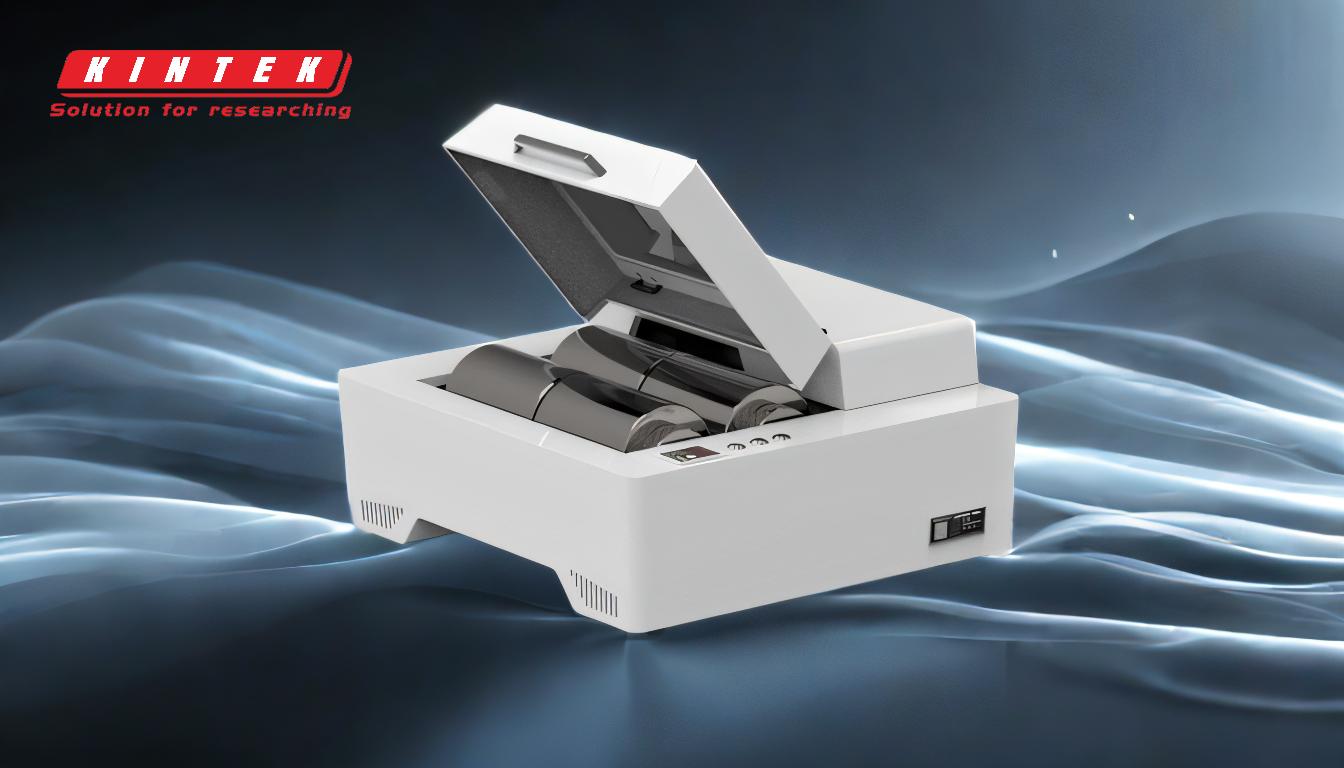
-
Grinding Medium:
- Ball Mill: Uses steel or ceramic balls as the grinding medium. The balls rotate inside the mill, impacting and grinding the material into fine particles.
- Rod Mill: Uses long cylindrical rods made of steel or other materials. The rods grind the material by rolling and sliding within the mill, providing a more uniform particle size.
-
Grinding Mechanism:
- Ball Mill: The grinding action is primarily through impact and attrition. The balls drop from near the top of the shell and impact the material, breaking it down into smaller particles.
- Rod Mill: The grinding action is more of a rolling and sliding motion. The rods grind the material by rolling over it, which helps in producing a more uniform particle size and avoids over-grinding.
-
Particle Size:
- Ball Mill: Capable of producing very fine particles, often used for materials that require ultra-fine grinding. It is suitable for materials like ceramics, paint, and ore.
- Rod Mill: Produces coarser particles compared to a ball mill. It is more effective for coarse grinding and is often used in the first stage of grinding in mineral processing.
-
Application:
- Ball Mill: Commonly used in industries where fine grinding is required, such as in the production of cement, silicate products, new building materials, refractory materials, fertilizers, black and non-ferrous metal beneficiation, and glass ceramics.
- Rod Mill: Often used in the mining industry for grinding ores, coal/coke, and other materials. It is particularly useful in applications where over-grinding needs to be avoided.
-
Design and Operation:
- Ball Mill: Typically has a higher rotational speed, which increases the impact force of the balls. It can be operated in both dry and wet conditions.
- Rod Mill: Generally operates at a lower speed to allow the rods to cascade and grind the material more effectively. It is often used in wet grinding applications.
-
Maintenance and Wear:
- Ball Mill: The balls and the lining of the mill are subject to wear and need to be replaced periodically. The maintenance can be more frequent due to the high impact forces involved.
- Rod Mill: The rods are also subject to wear, but the wear is generally more uniform. The maintenance requirements can be lower compared to a ball mill, especially in applications where over-grinding is a concern.
-
Energy Efficiency:
- Ball Mill: Can be less energy-efficient for coarse grinding due to the high impact forces and the need for finer grinding.
- Rod Mill: More energy-efficient for coarse grinding as it avoids over-grinding and produces a more uniform particle size.
In summary, the choice between a ball mill and a rod mill depends on the specific requirements of the application, including the desired particle size, material properties, and operational considerations. Both mills have their unique advantages and are suited for different types of grinding tasks.
Summary Table:
Aspect | Ball Mill | Rod Mill |
---|---|---|
Grinding Medium | Steel or ceramic balls | Long cylindrical rods |
Grinding Mechanism | Impact and attrition | Rolling and sliding motion |
Particle Size | Produces very fine particles | Produces coarser particles |
Applications | Cement, ceramics, paint, ore | Mining, coal/coke, coarse grinding |
Design & Operation | Higher rotational speed, dry/wet conditions | Lower speed, often wet grinding |
Maintenance | Frequent due to high wear | Lower maintenance, uniform wear |
Energy Efficiency | Less efficient for coarse grinding | More efficient for coarse grinding |
Need help choosing the right grinding equipment for your application? Contact our experts today!