Rotary tablet presses and single punch tablet presses are both used in the pharmaceutical and nutraceutical industries to produce tablets, but they differ significantly in design, operation, and application. A single punch tablet press is a simple, manually operated machine ideal for small-scale production or R&D, while a rotary tablet press is a high-speed, automated machine designed for large-scale manufacturing. The single punch press compresses one tablet at a time using a single set of dies and punches, whereas the rotary press uses multiple dies and punches arranged in a circular turret to produce tablets continuously. Key differences include production capacity, automation level, and suitability for specific use cases.
Key Points Explained:
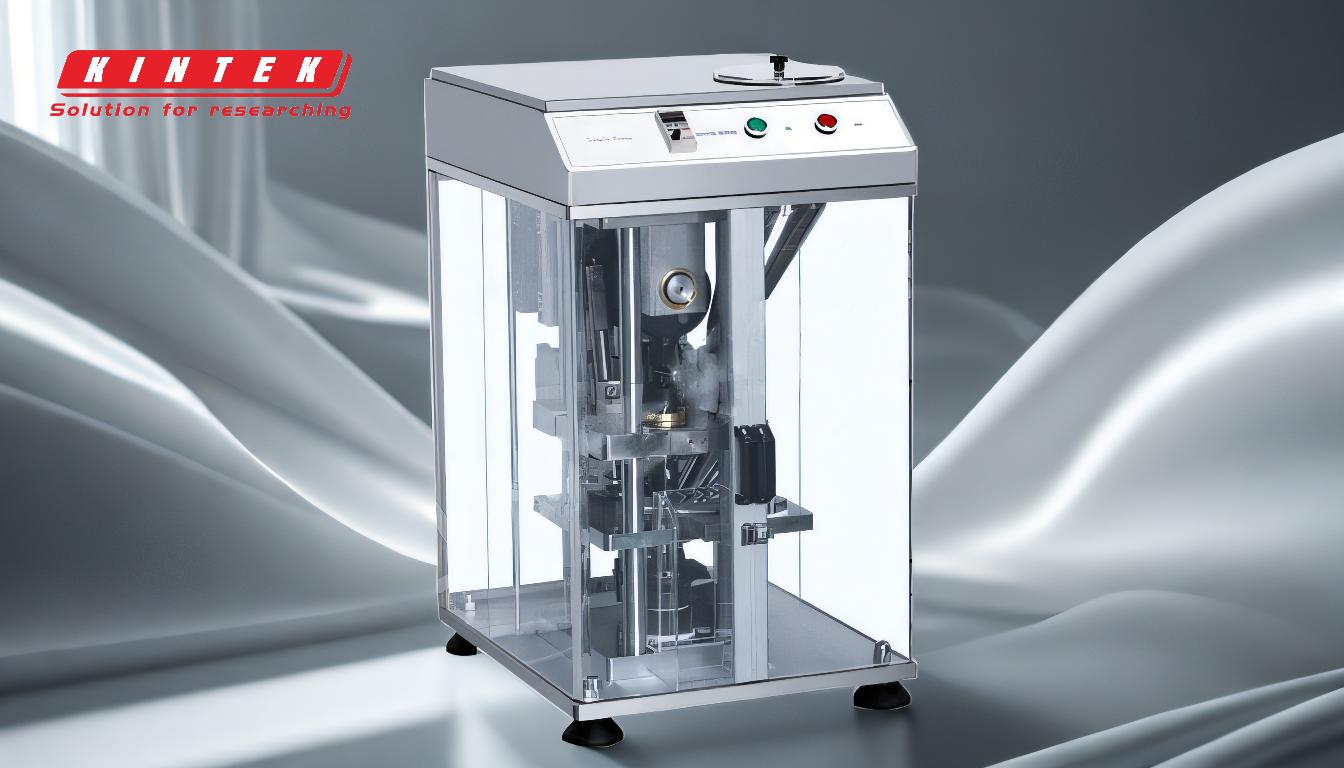
-
Design and Operation:
- Single Punch Tablet Press: This machine operates using a single set of dies and punches. The powder mixture is fed into the die cavity, and the punch compresses the material to form a tablet. It is manually operated and produces one tablet at a time. Key components include the hopper, die cavity, punches, dosing plow, and ejection cam. For more details, refer to single punch tablet press.
- Rotary Tablet Press: This machine features multiple dies and punches arranged in a rotating turret. As the turret rotates, the punches compress the powder mixture to form tablets continuously. It is fully automated and capable of producing thousands of tablets per hour.
-
Production Capacity:
- Single Punch Tablet Press: Ideal for small-scale production or R&D due to its low output capacity. It is suitable for projects with minimal test material or when confirming compressibility is the primary goal.
- Rotary Tablet Press: Designed for large-scale manufacturing, with high-speed production capabilities. It can produce hundreds to thousands of tablets per minute, making it suitable for industrial applications.
-
Automation and Efficiency:
- Single Punch Tablet Press: Requires manual operation, making it less efficient for high-volume production. However, it is easy to operate and maintain.
- Rotary Tablet Press: Fully automated, with advanced features like weight control, pressure monitoring, and ejection systems. This ensures consistent tablet quality and high efficiency.
-
Applications:
- Single Punch Tablet Press: Best suited for small-scale projects, R&D, or when working with limited material quantities. It is also used for testing the compressibility of new formulations.
- Rotary Tablet Press: Used in large-scale manufacturing of tablets for pharmaceuticals, nutraceuticals, and other industries. It is ideal for high-volume production with consistent quality.
-
Advantages:
- Single Punch Tablet Press: Compact size, low noise levels, ease of operation, and low material consumption. It is also cost-effective for small-scale applications.
- Rotary Tablet Press: High production capacity, automation, and ability to produce uniform tablets at high speeds. It is also versatile, with the ability to handle a wide range of tablet shapes and sizes.
-
Limitations:
- Single Punch Tablet Press: Limited production capacity and manual operation make it unsuitable for large-scale manufacturing.
- Rotary Tablet Press: Higher initial cost and complexity of operation compared to single punch presses. It also requires more space and maintenance.
In summary, the choice between a rotary tablet press and a single punch tablet press depends on the scale of production, automation needs, and specific application requirements. Single punch presses are ideal for small-scale or R&D purposes, while rotary presses are better suited for large-scale, high-speed production.
Summary Table:
Feature | Single Punch Tablet Press | Rotary Tablet Press |
---|---|---|
Design | Manual, single set of dies/punches | Automated, multiple dies/punches |
Production Capacity | Low, ideal for R&D/small-scale | High, suitable for large-scale |
Automation | Manual operation | Fully automated |
Applications | Small-scale, R&D, testing | Large-scale manufacturing |
Advantages | Compact, low cost, easy to operate | High speed, consistent quality |
Limitations | Limited output, manual operation | Higher cost, complex maintenance |
Need help choosing the right tablet press for your needs? Contact our experts today!