Chemical vapor deposition (CVD) and physical vapor deposition (PVD) are two distinct thin-film deposition techniques widely used in various industries. While both methods aim to deposit thin films onto substrates, they differ significantly in their processes, operating conditions, and outcomes. CVD relies on chemical reactions involving gaseous precursors, typically requiring high temperatures, and can produce corrosive byproducts. In contrast, PVD involves the physical vaporization of solid or liquid materials, operates at lower temperatures, and avoids corrosive byproducts. The choice between CVD and PVD depends on factors such as the desired film properties, substrate material, and application requirements.
Key Points Explained:
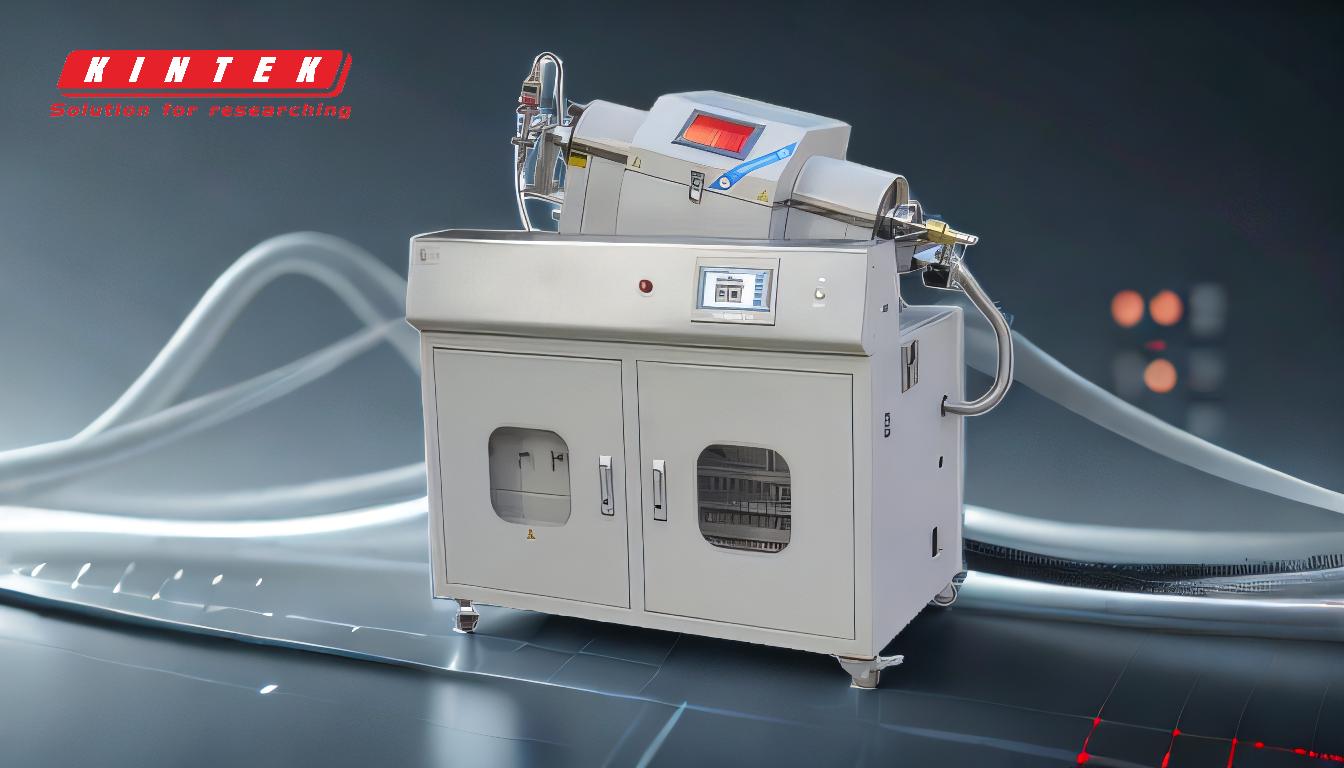
-
Process Mechanism:
- CVD: Involves chemical reactions of gaseous precursors on a heated substrate surface. The gaseous molecules adsorb onto the substrate, react, and form a solid film. This process is multi-directional, meaning it can coat complex geometries uniformly.
- PVD: Involves the physical vaporization of a solid or liquid material, which is then transported as a vapor to the substrate, where it condenses to form a thin film. PVD is a line-of-sight process, meaning it is more suitable for flat or simple geometries.
-
Temperature Requirements:
- CVD: Typically operates at high temperatures, ranging from 500°C to 1100°C. This high-temperature environment facilitates chemical reactions but can limit the types of substrates that can be used.
- PVD: Operates at lower temperatures compared to CVD, making it suitable for temperature-sensitive substrates. However, some PVD techniques, like electron beam PVD (EBPVD), can achieve high deposition rates at relatively low temperatures.
-
Byproducts and Impurities:
- CVD: Often produces corrosive gaseous byproducts, which can complicate the process and require additional safety measures. The high temperatures may also lead to impurities in the deposited film.
- PVD: Does not produce corrosive byproducts, making it a cleaner process. However, the deposition rates are generally lower compared to CVD.
-
Deposition Rates:
- CVD: Generally offers higher deposition rates, making it suitable for applications requiring thick films or high throughput.
- PVD: Typically has lower deposition rates, although advanced techniques like EBPVD can achieve rates ranging from 0.1 to 100 μm/min.
-
Material Utilization Efficiency:
- CVD: Efficient in terms of material utilization, as gaseous precursors can uniformly coat complex geometries.
- PVD: Also efficient, particularly in techniques like EBPVD, which offer very high material utilization efficiency.
-
Applications:
- CVD: Commonly used in semiconductor manufacturing, where high-quality, uniform films are required. It is also used for coating tools, optical components, and wear-resistant surfaces.
- PVD: Widely used for decorative coatings, anti-corrosion layers, and wear-resistant films. It is also employed in the production of solar panels and medical devices.
-
Equipment and Operational Complexity:
- CVD: Requires specialized equipment to handle high temperatures and corrosive gases. The process also demands skilled operators and precise control over reaction conditions.
- PVD: Requires vacuum conditions and, in some cases, cooling systems to manage heat dissipation. The equipment is generally less complex than CVD systems but still requires skilled operation.
In summary, the choice between CVD and PVD depends on the specific requirements of the application, including the desired film properties, substrate material, and operational constraints. CVD is favored for high-temperature, high-deposition-rate applications, while PVD is preferred for lower-temperature, cleaner processes with complex geometries.
Summary Table:
Aspect | CVD | PVD |
---|---|---|
Process Mechanism | Chemical reactions of gaseous precursors on a heated substrate surface | Physical vaporization of solid/liquid materials, condensing on substrate |
Temperature | High (500°C–1100°C) | Lower, suitable for temperature-sensitive substrates |
Byproducts | Corrosive gaseous byproducts | No corrosive byproducts |
Deposition Rates | High | Lower (0.1–100 μm/min with advanced techniques like EBPVD) |
Material Efficiency | High, uniform coating on complex geometries | High, especially with EBPVD |
Applications | Semiconductors, tools, optical components, wear-resistant surfaces | Decorative coatings, anti-corrosion layers, solar panels, medical devices |
Equipment Complexity | High, requires handling corrosive gases and high temperatures | Lower, requires vacuum conditions and cooling systems |
Need help choosing between CVD and PVD for your application? Contact our experts today for tailored advice!