Diamond coatings and DLC (Diamond-Like Carbon) coatings are both advanced surface treatments used to enhance the performance of materials, but they differ significantly in their composition, properties, and applications. Diamond coatings are made of pure carbon in a crystalline structure, offering extreme hardness and wear resistance. In contrast, DLC coatings are amorphous or semi-amorphous carbon films that combine properties of both diamond (hardness) and graphite (lubricity). While diamond coatings excel in applications requiring maximum hardness and durability, DLC coatings are preferred for their low friction, wear resistance, and versatility in various industries, including automotive, biomedical, and decorative applications.
Key Points Explained:
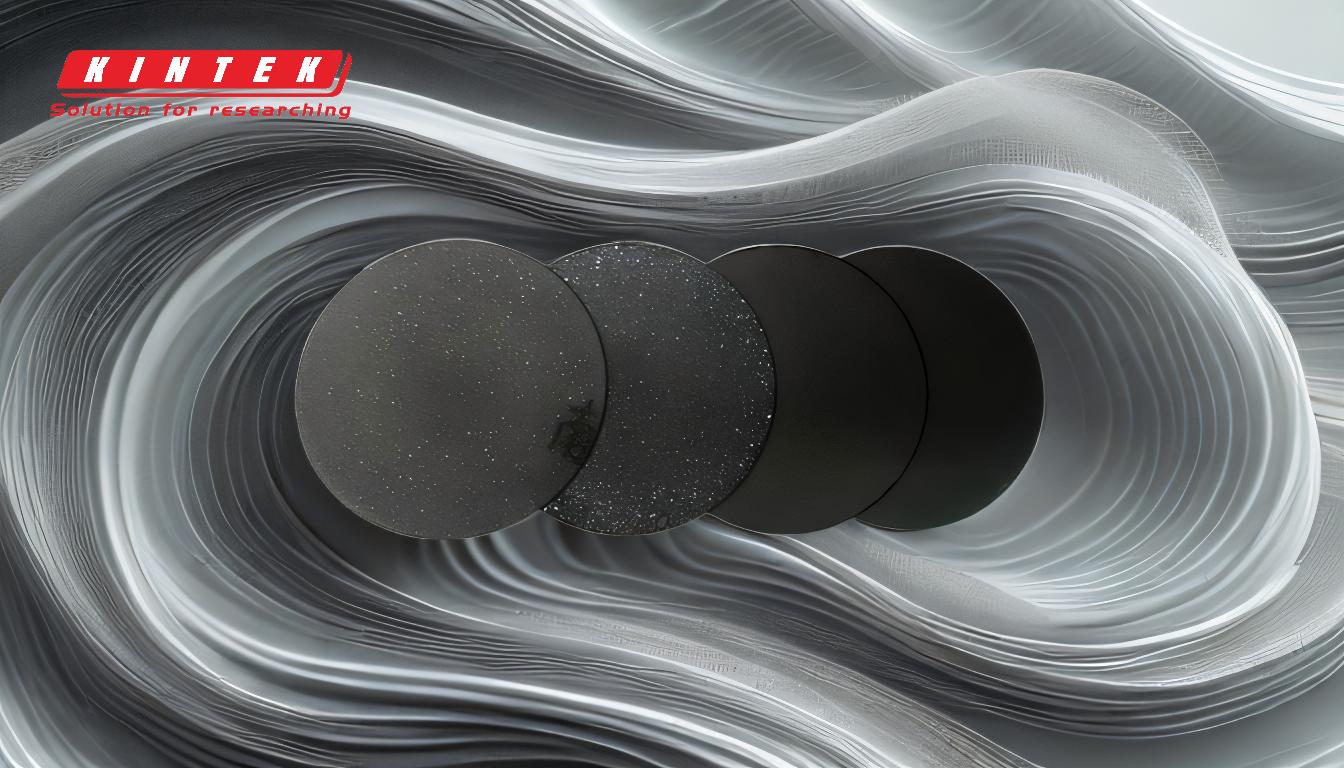
-
Composition and Structure:
- Diamond Coatings: These are composed of pure carbon arranged in a crystalline lattice structure, identical to natural diamond. This structure gives diamond coatings exceptional hardness and thermal conductivity.
- DLC Coatings: DLC is an amorphous or semi-amorphous material containing a mix of sp3 (diamond-like) and sp2 (graphite-like) carbon bonds. The proportion of these bonds determines the coating's properties, such as hardness and lubricity.
-
Hardness and Wear Resistance:
- Diamond Coatings: Diamond coatings are the hardest known material, with a hardness of up to 10,000 HV (Vickers hardness). This makes them ideal for applications requiring extreme wear resistance and durability, such as cutting tools and industrial machinery.
- DLC Coatings: DLC coatings have a hardness ranging from 1,500 to 3,000 HV, which is significantly lower than diamond coatings but still much higher than many other materials. They are used in applications where a balance of hardness and low friction is required, such as automotive components and biomedical devices.
-
Coefficient of Friction:
- Diamond Coatings: While diamond coatings are extremely hard, they do not inherently provide low friction. Their primary advantage lies in their wear resistance rather than lubricity.
- DLC Coatings: DLC coatings are known for their low coefficient of friction, making them ideal for sliding applications. This property is particularly valuable in automotive and machinery industries, where reducing friction can lead to energy savings and longer component life.
-
Applications:
- Diamond Coatings: These are used in high-wear applications such as cutting tools, drill bits, and industrial machinery where maximum hardness and durability are required. They are also used in specialized applications like optical components and high-performance electronics.
- DLC Coatings: DLC coatings are versatile and used in a wide range of industries. In the automotive sector, they are applied to components like camshafts, bearings, and power train elements to reduce friction and wear. In the biomedical field, they are used on prostheses and surgical tools for their biocompatibility and wear resistance. Additionally, DLC coatings are used decoratively in luxury watches for their black, scratch-resistant finish.
-
Deposition Techniques:
- Diamond Coatings: Diamond coatings are typically deposited using chemical vapor deposition (CVD) techniques, which require high temperatures and specialized equipment. This process results in a pure, crystalline diamond layer.
- DLC Coatings: DLC coatings can be deposited using various techniques, including plasma-enhanced chemical vapor deposition (PECVD). PECVD allows for lower deposition temperatures, making it suitable for coating temperature-sensitive materials like polymers. This method also offers advantages such as chemical stability, fewer toxic byproducts, and high deposition rates.
-
Thermal and Chemical Stability:
- Diamond Coatings: Diamond coatings are highly stable at high temperatures and in corrosive environments, making them suitable for extreme conditions.
- DLC Coatings: DLC coatings also exhibit excellent chemical and wear resistance, but their thermal stability is generally lower than that of diamond coatings. However, they perform well in a wide range of environments, including corrosive and high-wear applications.
-
Cost and Scalability:
- Diamond Coatings: The production of diamond coatings is more expensive and less scalable due to the high temperatures and specialized equipment required. This limits their use to high-value applications where their unique properties are essential.
- DLC Coatings: DLC coatings are more cost-effective and scalable, especially with techniques like PECVD. This makes them suitable for a broader range of applications, including large-scale industrial uses.
In summary, while both diamond and DLC coatings offer significant advantages in terms of hardness and wear resistance, they are tailored for different applications. Diamond coatings are best suited for extreme conditions requiring maximum hardness and durability, whereas DLC coatings provide a versatile solution with a balance of hardness, low friction, and wear resistance, making them ideal for a wide range of industrial and decorative applications.
Summary Table:
Aspect | Diamond Coatings | DLC Coatings |
---|---|---|
Composition | Pure carbon in a crystalline structure | Amorphous/semi-amorphous carbon with sp3 (diamond-like) and sp2 (graphite-like) bonds |
Hardness | Up to 10,000 HV (extremely hard) | 1,500–3,000 HV (hard but less than diamond) |
Coefficient of Friction | High (not inherently low friction) | Low (ideal for sliding applications) |
Applications | Cutting tools, industrial machinery, optical components, high-performance electronics | Automotive components, biomedical devices, decorative uses (e.g., luxury watches) |
Deposition Techniques | Chemical Vapor Deposition (CVD) | Plasma-Enhanced Chemical Vapor Deposition (PECVD) |
Thermal Stability | Excellent at high temperatures | Good, but lower than diamond coatings |
Cost and Scalability | Expensive, less scalable | Cost-effective, scalable |
Discover the best coating solution for your needs—contact our experts today!