E-beam evaporation and thermal evaporation are both physical vapor deposition (PVD) techniques used to deposit thin films onto substrates. The primary difference lies in the method of heating the source material. Thermal evaporation uses an electric current to heat a crucible, which melts and evaporates the material, making it suitable for lower-melting-point materials. In contrast, e-beam evaporation employs a high-energy electron beam to directly heat the source material, enabling it to handle high-melting-point materials like oxides. E-beam evaporation offers denser coatings, lower impurity risks, and higher deposition rates compared to thermal evaporation. The choice between the two depends on the material properties and desired film characteristics.
Key Points Explained:
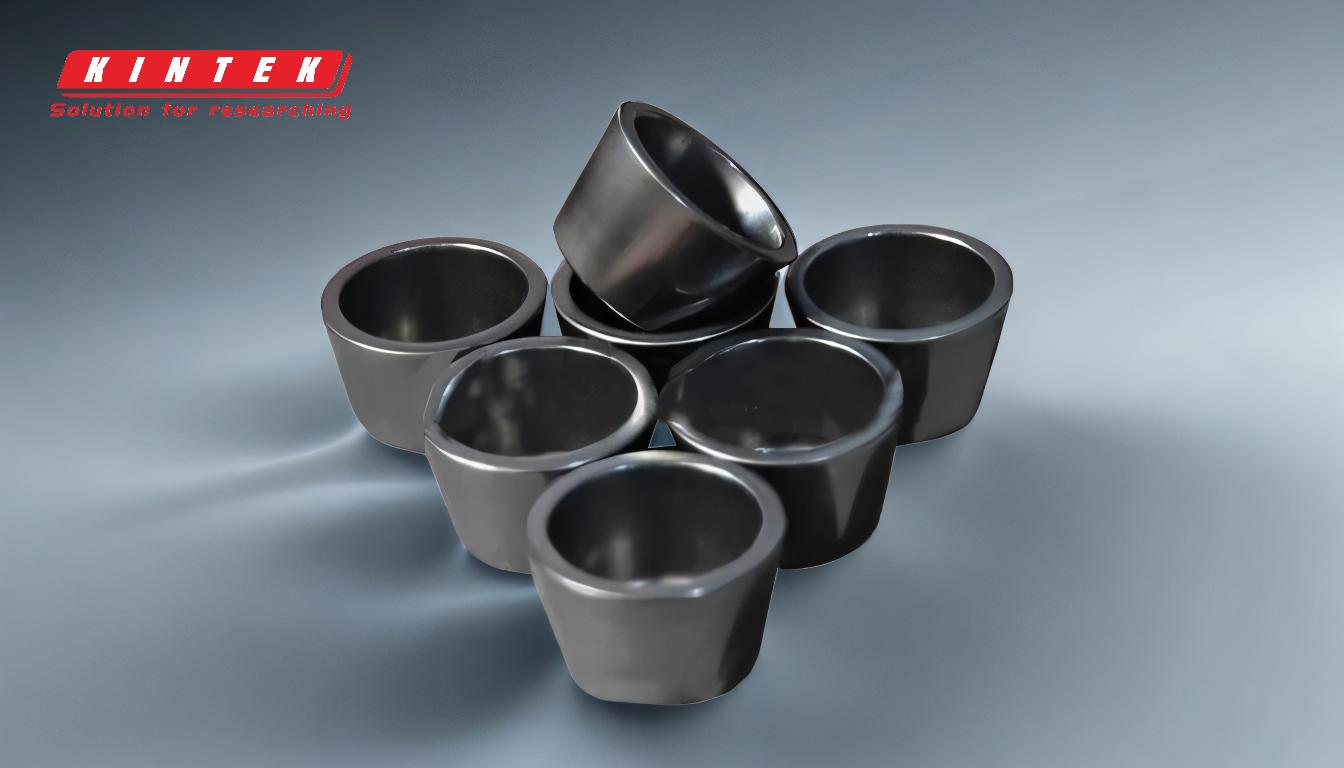
-
Heating Mechanism:
- Thermal Evaporation: Uses an electric current to heat a crucible, which in turn heats and evaporates the source material. This method is indirect and relies on thermal conduction.
- E-beam Evaporation: Utilizes a high-energy electron beam to directly heat the source material. The electron beam transfers kinetic energy to the material, causing it to evaporate. This method is more direct and efficient for high-melting-point materials.
-
Suitability for Materials:
- Thermal Evaporation: Best suited for materials with lower melting temperatures. It is ideal for metals and alloys that can be easily melted and evaporated using resistive heating.
- E-beam Evaporation: Capable of handling high-melting-point materials, such as oxides and refractory metals. The high-energy electron beam can provide the necessary energy to vaporize these materials without requiring a crucible to melt them first.
-
Film Characteristics:
- Thermal Evaporation: Produces thin films that may have lower density and higher impurity levels due to the indirect heating method and potential contamination from the crucible.
- E-beam Evaporation: Results in denser and purer thin films. The direct heating method reduces the risk of contamination, and the higher energy input leads to better film quality and adhesion.
-
Deposition Rate:
- Thermal Evaporation: Generally has a lower deposition rate compared to e-beam evaporation. The rate is limited by the heat transfer efficiency from the crucible to the source material.
- E-beam Evaporation: Offers a higher deposition rate due to the direct and efficient transfer of energy from the electron beam to the source material. This makes it more suitable for applications requiring rapid film formation.
-
Applications:
- Thermal Evaporation: Commonly used in applications where lower-melting-point materials are sufficient, such as in the deposition of aluminum or gold films in microelectronics and optics.
- E-beam Evaporation: Preferred for high-performance applications requiring high-melting-point materials, such as in the deposition of dielectric layers, optical coatings, and protective coatings in aerospace and semiconductor industries.
-
Equipment Complexity and Cost:
- Thermal Evaporation: Generally simpler and less expensive equipment. The setup involves a resistive heating element and a crucible, making it easier to maintain and operate.
- E-beam Evaporation: More complex and costly due to the need for an electron beam generator and associated cooling systems. However, the benefits in terms of film quality and material versatility often justify the higher cost.
-
Operational Considerations:
- Thermal Evaporation: Easier to operate and maintain, with fewer moving parts and simpler control systems. It is suitable for small-scale and less demanding applications.
- E-beam Evaporation: Requires more precise control and maintenance due to the complexity of the electron beam system. It is better suited for high-precision and high-throughput applications.
In summary, while both e-beam evaporation and thermal evaporation are effective PVD techniques, they differ significantly in their heating mechanisms, material suitability, film characteristics, and operational complexity. The choice between the two depends on the specific requirements of the application, including the type of material to be deposited, desired film properties, and budget constraints.
Summary Table:
Aspect | Thermal Evaporation | E-beam Evaporation |
---|---|---|
Heating Mechanism | Electric current heats a crucible, indirectly evaporating the material. | High-energy electron beam directly heats the source material. |
Material Suitability | Best for low-melting-point materials (e.g., metals, alloys). | Ideal for high-melting-point materials (e.g., oxides, refractory metals). |
Film Characteristics | Lower density, higher impurity risks due to indirect heating. | Denser, purer films with better adhesion and quality. |
Deposition Rate | Lower rate due to indirect heat transfer. | Higher rate due to direct energy transfer. |
Applications | Microelectronics, optics (e.g., aluminum, gold films). | Aerospace, semiconductors, optical coatings (e.g., dielectric layers). |
Equipment Cost | Simpler, less expensive setup. | More complex and costly due to electron beam systems. |
Operational Ease | Easier to operate and maintain, suitable for small-scale applications. | Requires precise control, better for high-precision, high-throughput applications. |
Need help choosing the right PVD technique for your application? Contact our experts today for personalized advice!