Filtration and centrifugation are both separation techniques used to separate solids from liquids or different components in a mixture, but they operate on different principles and are suited for different applications. Filtration relies on passing a mixture through a filter medium that traps solid particles while allowing the liquid to pass through. Centrifugation, on the other hand, uses centrifugal force to separate components based on their density differences. While filtration is often simpler and suitable for larger particles, centrifugation is more effective for fine particles or when rapid separation is needed. Both methods have unique advantages and limitations, making them suitable for specific scenarios.
Key Points Explained:
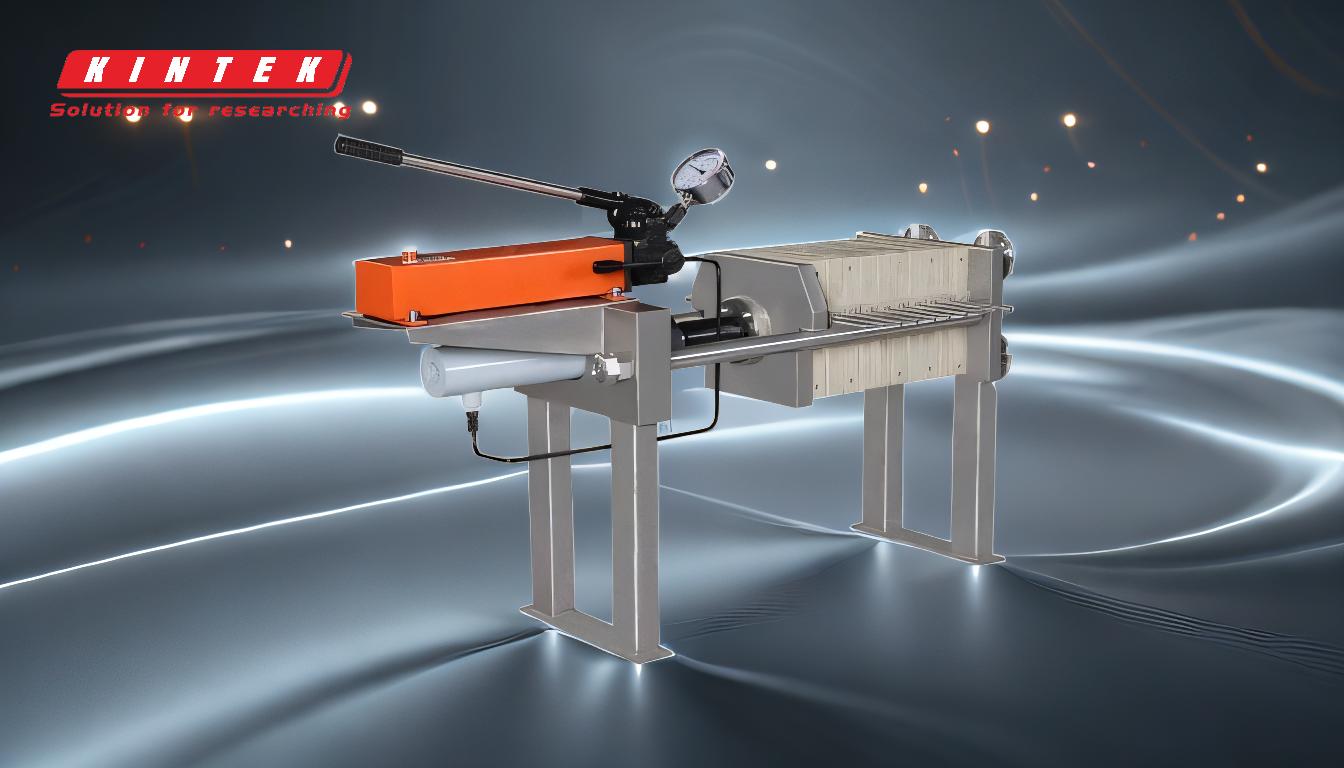
-
Principle of Operation:
- Filtration: Filtration works by passing a mixture through a filter medium (such as paper, cloth, or a membrane) that retains solid particles while allowing the liquid (filtrate) to pass through. The separation is based on particle size.
- Centrifugation: Centrifugation uses centrifugal force to separate components of a mixture based on their density. Denser components move outward and settle at the bottom, while less dense components remain closer to the top.
-
Applications:
- Filtration: Commonly used in water treatment, air purification, and laboratory settings to separate larger particles from liquids or gases. It is ideal for coarse separations.
- Centrifugation: Widely used in laboratories for separating blood components, isolating DNA, or purifying proteins. It is also used in industries like pharmaceuticals and food processing for fine separations.
-
Efficiency:
- Filtration: Effective for larger particles but may struggle with very fine particles or colloidal suspensions. Filter clogging can reduce efficiency over time.
- Centrifugation: Highly efficient for fine particles and colloidal systems. It can achieve rapid separation, even for particles that are difficult to filter.
-
Equipment and Setup:
- Filtration: Requires a filter medium and a support structure (e.g., a funnel or filter press). The setup is relatively simple and cost-effective.
- Centrifugation: Requires a centrifuge machine, which can be more expensive and complex to operate. High-speed centrifuges may also require specialized maintenance.
-
Speed of Separation:
- Filtration: Generally slower, especially for fine particles or viscous liquids. The process depends on gravity or applied pressure.
- Centrifugation: Much faster, as the high-speed rotation generates significant centrifugal force, enabling rapid separation.
-
Scalability:
- Filtration: Easily scalable for industrial applications, such as large-scale water treatment or chemical processing.
- Centrifugation: More challenging to scale up due to the complexity and cost of large centrifuges, though industrial centrifuges are available for specific applications.
-
Energy Consumption:
- Filtration: Typically low energy consumption, especially for gravity-based filtration.
- Centrifugation: Higher energy consumption due to the need for high-speed rotation.
-
Limitations:
- Filtration: Limited by the pore size of the filter medium. Fine particles or dissolved substances cannot be separated by filtration alone.
- Centrifugation: Requires careful balancing of samples to avoid equipment damage. It may also generate heat, which can affect sensitive samples.
-
Cost:
- Filtration: Generally more cost-effective, especially for small-scale or simple applications.
- Centrifugation: Higher initial and operational costs due to the need for specialized equipment.
-
Maintenance:
- Filtration: Low maintenance, primarily involving periodic replacement of filter media.
- Centrifugation: Requires regular maintenance, including balancing, cleaning, and potential repairs to the centrifuge rotor and motor.
In summary, filtration and centrifugation are complementary techniques, each with its own strengths and limitations. The choice between them depends on the specific requirements of the separation task, such as particle size, speed, and scale.
Summary Table:
Aspect | Filtration | Centrifugation |
---|---|---|
Principle | Separates based on particle size using a filter medium. | Separates based on density differences using centrifugal force. |
Applications | Water treatment, air purification, coarse separations. | Blood component separation, DNA isolation, fine particle separations. |
Efficiency | Effective for larger particles; struggles with fine particles or colloids. | Highly efficient for fine particles and colloidal systems. |
Equipment | Simple setup with filter media and support structures. | Requires a centrifuge machine; complex and costly. |
Speed | Slower, especially for fine particles or viscous liquids. | Rapid separation due to high-speed rotation. |
Scalability | Easily scalable for industrial applications. | Challenging to scale up due to cost and complexity. |
Energy Consumption | Low energy consumption. | High energy consumption due to high-speed rotation. |
Limitations | Limited by filter pore size; cannot separate dissolved substances. | Requires careful balancing; may generate heat affecting sensitive samples. |
Cost | Cost-effective for small-scale or simple applications. | Higher initial and operational costs. |
Maintenance | Low maintenance; periodic filter replacement. | Regular maintenance, including balancing and cleaning. |
Need help choosing the right separation technique for your application? Contact our experts today!