DC (Direct Current) and RF (Radio Frequency) magnetron sputtering are two widely used techniques in thin-film deposition, each with distinct characteristics and applications. DC sputtering uses a constant voltage and is ideal for conductive materials, offering high deposition rates and cost-efficiency for large substrates. RF sputtering, on the other hand, uses an alternating voltage at radio frequencies, making it suitable for both conductive and non-conductive materials. It prevents charge buildup on the target surface, especially useful for insulating materials, but has a lower deposition rate and higher cost. The choice between DC and RF sputtering depends on the target material, substrate size, and specific application requirements.
Key Points Explained:
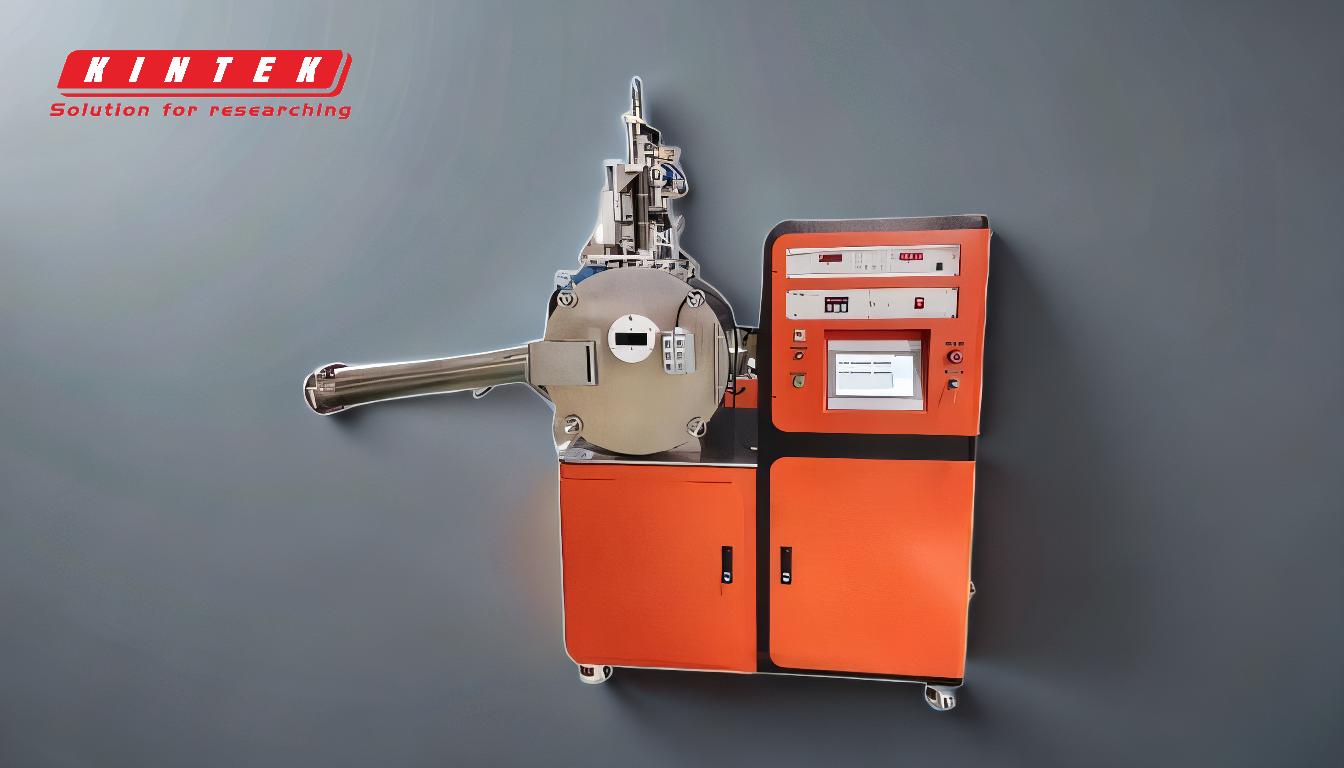
-
Power Source and Voltage Type:
- DC Sputtering: Uses a constant Direct Current (DC) voltage. This method is straightforward and effective for conductive materials.
- RF Sputtering: Uses an Alternating Current (AC) voltage, typically at a frequency of 13.56 MHz. The alternating voltage prevents charge accumulation on the target, making it suitable for both conductive and non-conductive materials.
-
Target Material Compatibility:
- DC Sputtering: Only works with conductive materials, such as pure metals. Non-conductive materials would cause charge buildup, leading to arcing and process instability.
- RF Sputtering: Can be used with both conductive and non-conductive (dielectric) materials. The alternating voltage neutralizes charge buildup, allowing for the sputtering of insulators.
-
Deposition Rate:
- DC Sputtering: Offers higher deposition rates compared to RF sputtering. This makes it more efficient for large-scale production and large substrates.
- RF Sputtering: Has a lower deposition rate due to the lower sputter yield and the need for a two-cycle process (polarization and reverse polarization).
-
Cost and Efficiency:
- DC Sputtering: Generally more cost-effective and economical, especially for large substrate quantities. It is widely used in industries where high throughput is required.
- RF Sputtering: More expensive due to the complexity of the RF power supply and the lower deposition rate. It is typically used for smaller substrates or when depositing non-conductive materials.
-
Process Characteristics:
- DC Sputtering: Involves the acceleration of positively charged gas ions toward the target, leading to the ejection of target atoms and their deposition on the substrate.
- RF Sputtering: Involves a two-cycle process where the target is alternately positively and negatively charged. This prevents charge buildup and allows for the sputtering of insulating materials.
-
Pressure Requirements:
- DC Sputtering: Often requires higher operating pressures, which can be more challenging to maintain and control.
- RF Sputtering: Operates at lower pressures due to the high percentage of ionized particles, which can lead to better film quality and uniformity.
-
Applications:
- DC Sputtering: Preferred for applications involving conductive materials and large substrates, such as in the production of metal coatings, solar panels, and decorative films.
- RF Sputtering: Suitable for applications requiring the deposition of insulating materials, such as in the production of optical coatings, semiconductor devices, and thin-film electronics.
In summary, the choice between DC and RF magnetron sputtering depends on the specific requirements of the application, including the type of target material, desired deposition rate, substrate size, and budget constraints. DC sputtering is generally more cost-effective and efficient for conductive materials, while RF sputtering is essential for depositing non-conductive materials and achieving high-quality thin films.
Summary Table:
Aspect | DC Sputtering | RF Sputtering |
---|---|---|
Power Source | Constant DC voltage | Alternating AC voltage (13.56 MHz) |
Material Compatibility | Conductive materials only | Conductive and non-conductive materials |
Deposition Rate | Higher deposition rates | Lower deposition rates |
Cost | More cost-effective | More expensive |
Pressure Requirements | Higher operating pressures | Lower operating pressures |
Applications | Metal coatings, solar panels, decorative films | Optical coatings, semiconductor devices, thin-film electronics |
Need help choosing the right sputtering technique for your project? Contact our experts today!