Mixers and dispersers are both essential equipment in various industries, but they serve distinct purposes and operate differently. A mixer is primarily used to blend or combine materials to achieve a homogeneous mixture, often relying on mechanical agitation. In contrast, a disperser is designed to break down particles and distribute them evenly within a liquid medium, achieving a fine and stable dispersion. While mixers focus on uniformity, dispersers emphasize particle size reduction and dispersion quality. Understanding their differences is crucial for selecting the right equipment based on the desired outcome, whether it’s blending, emulsifying, or achieving a fine dispersion.
Key Points Explained:
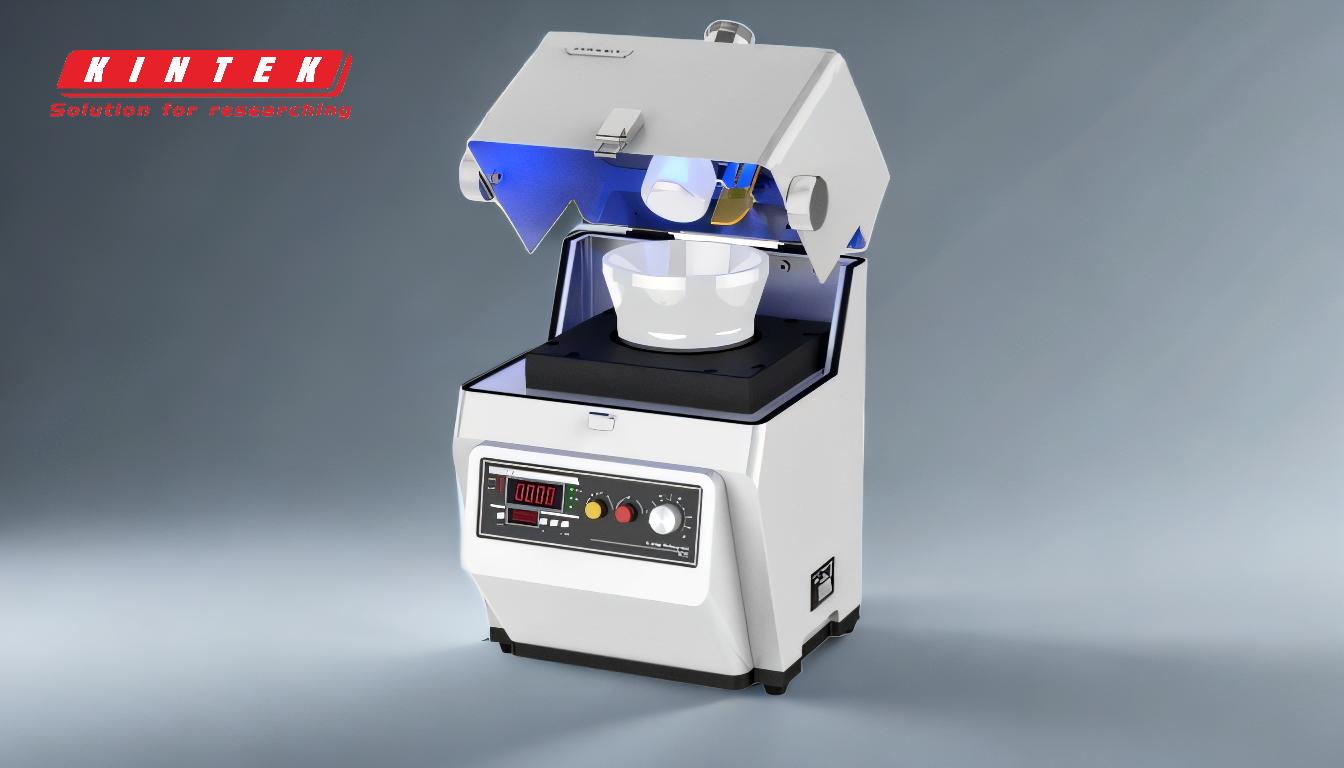
-
Purpose and Functionality:
- Mixer: A mixer is designed to combine two or more materials to create a uniform mixture. It is commonly used in industries like food, pharmaceuticals, and chemicals for blending dry powders, liquids, or semi-solids. Mixers rely on mechanical agitation, such as rotating blades or paddles, to achieve homogeneity.
- Disperser: A disperser is specifically engineered to break down solid particles and distribute them evenly within a liquid medium. It is used to create stable emulsions, suspensions, or dispersions, often requiring high shear forces to reduce particle size and ensure uniformity.
-
Mechanism of Operation:
- Mixer: Mixers typically use low to moderate shear forces. They employ various mechanisms like stirring, tumbling, or kneading, depending on the material's properties. Examples include ribbon blenders, planetary mixers, and paddle mixers.
- Disperser: Dispersers operate using high shear forces generated by high-speed rotating blades or rotors. This intense mechanical energy breaks down agglomerates and disperses particles uniformly in the liquid. Examples include high-speed dispersers and rotor-stator homogenizers.
-
Applications:
- Mixer: Mixers are ideal for applications where the goal is to achieve a uniform blend without altering the particle size. Common uses include mixing dough, blending powders, and combining liquids.
- Disperser: Dispersers are used when the goal is to create fine dispersions or emulsions, such as in paint production, ink manufacturing, or pharmaceutical formulations. They are essential for achieving stable and consistent product quality.
-
Key Differences:
- Shear Force: Mixers use lower shear forces, while dispersers rely on high shear forces to achieve dispersion.
- Outcome: Mixers produce homogeneous mixtures, whereas dispersers create fine, stable dispersions with reduced particle size.
- Equipment Design: Mixers often have simpler designs with slower-moving components, while dispersers feature high-speed rotors or blades to generate the necessary shear.
-
Selection Criteria:
- For Mixers: Choose a mixer if the primary goal is blending or combining materials without altering their particle size or structure.
- For Dispersers: Opt for a disperser if the process requires breaking down particles and achieving a fine, stable dispersion in a liquid medium.
By understanding these differences, purchasers can make informed decisions based on the specific requirements of their processes, ensuring optimal performance and product quality.
Summary Table:
Aspect | Mixer | Disperser |
---|---|---|
Purpose | Combines materials for a uniform mixture | Breaks down particles for fine dispersion in a liquid medium |
Shear Force | Low to moderate | High |
Outcome | Homogeneous mixture | Fine, stable dispersion with reduced particle size |
Applications | Blending powders, mixing dough, combining liquids | Paint production, ink manufacturing, pharmaceutical formulations |
Equipment Design | Simpler design with slower-moving components | High-speed rotors or blades for intense shear forces |
Selection Criteria | Choose for blending without altering particle size | Choose for particle breakdown and fine dispersion in liquids |
Still unsure which equipment is right for your needs? Contact our experts today for personalized guidance!