Pyrolysis and gasification are both thermal conversion processes used to transform solid fuels, such as biomass, into usable energy products. However, they differ significantly in their operating conditions, chemical reactions, and end products. Pyrolysis occurs in the absence of oxygen, producing gases, liquids, and solid char, while gasification involves partial oxidation with controlled amounts of oxygen or steam, resulting in a gaseous mixture known as syngas. The key distinctions lie in the presence or absence of oxygen, the nature of the chemical reactions, and the composition of the output products. Understanding these differences is crucial for selecting the appropriate process for specific applications, such as energy production or waste management.
Key Points Explained:
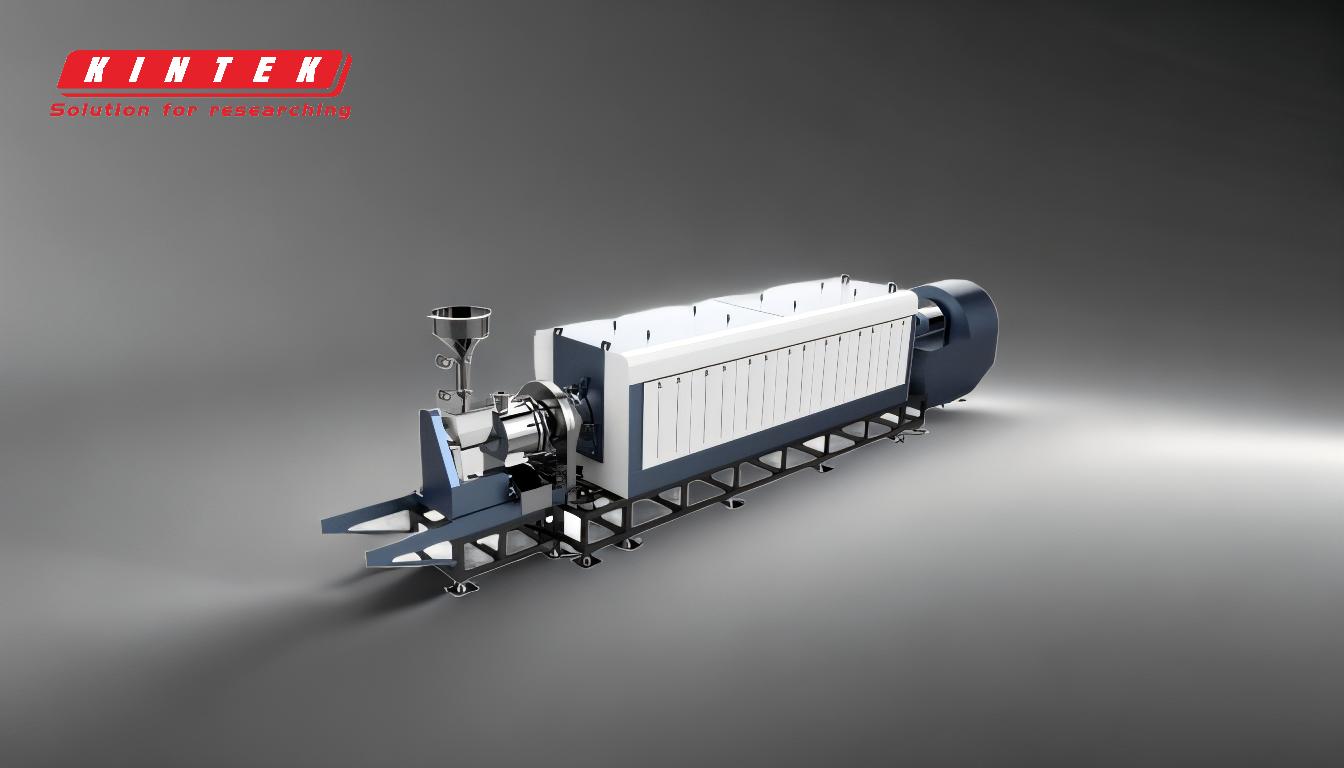
-
Presence of Oxygen:
- Pyrolysis: Operates in the complete absence of oxygen or with a limited supply that prevents significant oxidation. This anaerobic environment ensures that thermal decomposition occurs without combustion.
- Gasification: Involves the controlled introduction of oxygen or steam, enabling partial oxidation. This process allows for the conversion of solid fuels into a gaseous mixture through reactions with oxygen.
-
Chemical Reactions:
- Pyrolysis: Primarily involves thermal decomposition (thermolysis) of organic materials in an inert atmosphere. The absence of oxygen prevents combustion, leading to the breakdown of complex molecules into simpler gases, liquids (bio-oil), and solid char.
- Gasification: Combines thermal decomposition with partial oxidation. The presence of oxygen or steam triggers reactions that convert carbonaceous materials into syngas, a mixture primarily composed of hydrogen (H₂), carbon monoxide (CO), and carbon dioxide (CO₂).
-
End Products:
-
Pyrolysis: Yields three main products:
- Gases: Such as methane (CH₄), hydrogen (H₂), and carbon monoxide (CO).
- Liquids: Bio-oil, which can be further refined for use as fuel or chemical feedstock.
- Solids: Char, a carbon-rich residue that can be used as a soil amendment or fuel.
- Gasification: Produces primarily gaseous output, known as syngas, which is a mixture of hydrogen, carbon monoxide, and carbon dioxide. This syngas can be used directly as a fuel or further processed to produce chemicals and fuels.
-
Pyrolysis: Yields three main products:
-
Process Conditions:
- Pyrolysis: Typically occurs at moderate to high temperatures (400–800°C) in an oxygen-free environment. The process is endothermic, requiring external heat input to drive the decomposition reactions.
- Gasification: Operates at higher temperatures (700–1,200°C) and involves the controlled addition of oxygen or steam. The process is exothermic, as the partial oxidation reactions release heat, which can be used to sustain the process.
-
Applications:
- Pyrolysis: Suitable for producing bio-oil, biochar, and syngas for energy generation, chemical production, and soil enhancement. It is often used in waste management to convert organic waste into valuable products.
- Gasification: Primarily used for generating syngas, which can be utilized in power generation, synthetic fuel production, and industrial processes. It is also employed in waste-to-energy systems to convert municipal solid waste into energy.
-
Advantages and Limitations:
-
Pyrolysis:
- Advantages: Produces a diverse range of products (gases, liquids, and solids) and can handle a variety of feedstocks, including biomass and plastic waste. It is also relatively simple to control.
- Limitations: Requires careful management of the oxygen-free environment, and the bio-oil produced often needs further refining.
-
Gasification:
- Advantages: Efficiently converts carbonaceous materials into syngas, which is versatile and can be used in multiple applications. The process can handle a wide range of feedstocks, including low-quality fuels.
- Limitations: Requires precise control of oxygen levels and temperature to avoid complete combustion. The syngas may contain impurities that need to be removed before use.
-
Pyrolysis:
-
Environmental Impact:
- Pyrolysis: Generally considered environmentally friendly, as it can reduce waste volumes and produce renewable energy products. However, the process may emit volatile organic compounds (VOCs) if not properly managed.
- Gasification: Can be more efficient than pyrolysis in terms of energy recovery and has the potential to reduce greenhouse gas emissions. However, it may produce pollutants such as tar and particulates, which require advanced filtration systems.
In summary, pyrolysis and gasification are distinct thermal conversion processes with unique characteristics and applications. Pyrolysis operates without oxygen, producing a mix of gases, liquids, and solids, while gasification involves partial oxidation to generate syngas. The choice between these processes depends on the desired end products, feedstock availability, and specific application requirements.
Summary Table:
Aspect | Pyrolysis | Gasification |
---|---|---|
Presence of Oxygen | Operates without oxygen (anaerobic) | Uses controlled oxygen or steam (partial oxidation) |
Chemical Reactions | Thermal decomposition (thermolysis) in an inert atmosphere | Combines thermal decomposition with partial oxidation |
End Products | Gases (CH₄, H₂, CO), bio-oil, and solid char | Syngas (H₂, CO, CO₂) |
Process Conditions | Moderate to high temperatures (400–800°C), endothermic | Higher temperatures (700–1,200°C), exothermic |
Applications | Bio-oil, biochar, syngas for energy, chemicals, and soil enhancement | Syngas for power generation, synthetic fuels, and industrial processes |
Advantages | Diverse product range, handles various feedstocks | Efficient syngas production, versatile applications |
Limitations | Requires oxygen-free environment, bio-oil needs refining | Precise oxygen control needed, syngas may contain impurities |
Environmental Impact | Reduces waste, produces renewable energy; may emit VOCs | Efficient energy recovery; may produce tar and particulates |
Need help choosing the right thermal conversion process for your application? Contact our experts today!