Sputtering and electron beam evaporation are two distinct physical vapor deposition (PVD) techniques used to create thin films on substrates. While both methods aim to deposit material onto a surface, they differ significantly in their mechanisms, operational parameters, and applications. Sputtering involves using energized plasma atoms to dislodge atoms from a target material, which then adhere to the substrate. This process occurs at lower temperatures and provides better coating coverage for complex substrates. In contrast, electron beam evaporation uses a focused electron beam to vaporize high-temperature materials, resulting in a higher deposition rate but less uniform coverage. The choice between these methods depends on factors such as the desired film properties, substrate complexity, and application requirements.
Key Points Explained:
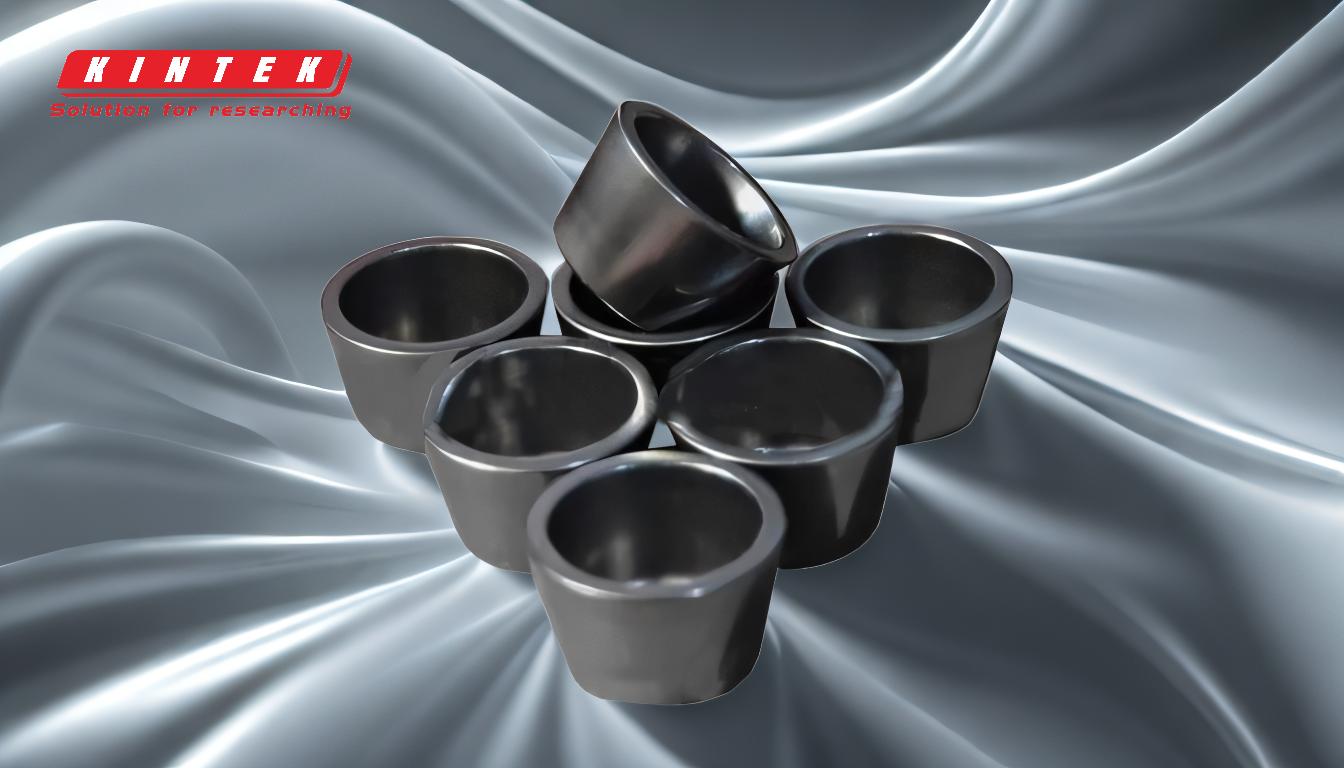
-
Mechanism of Deposition:
- Sputtering: Involves bombarding a target material with energized plasma atoms (typically argon), causing atoms to be ejected and deposited onto the substrate. This process does not rely on evaporation and occurs at lower temperatures.
- Electron Beam Evaporation: Uses a focused electron beam to heat and vaporize the target material, which then condenses onto the substrate. This is a thermal process that requires high temperatures.
-
Vacuum Level:
- Sputtering: Operates at a lower vacuum level compared to electron beam evaporation.
- Electron Beam Evaporation: Requires a high vacuum environment to ensure efficient vaporization and deposition.
-
Deposition Rate:
- Sputtering: Generally has a lower deposition rate, especially for dielectric materials, though it can be higher for pure metals.
- Electron Beam Evaporation: Offers a higher deposition rate, making it suitable for applications requiring rapid coating.
-
Adhesion and Film Quality:
- Sputtering: Provides better adhesion and more uniform film coverage, particularly on complex substrates. The films produced are typically of high purity.
- Electron Beam Evaporation: While it can produce high-quality films, the adhesion may not be as strong, and the coverage might be less uniform on intricate surfaces.
-
Energy of Deposited Species:
- Sputtering: Deposited species have higher energy, which can lead to better film density and adhesion.
- Electron Beam Evaporation: Deposited species have lower energy, which might result in less dense films.
-
Film Homogeneity and Grain Size:
- Sputtering: Produces films with greater homogeneity and smaller grain sizes, which can be advantageous for certain applications like optical coatings.
- Electron Beam Evaporation: Films may have larger grain sizes and less homogeneity, which could be a limitation for some applications.
-
Scalability and Automation:
- Sputtering: Highly scalable and can be easily automated, making it suitable for large-scale industrial applications.
- Electron Beam Evaporation: While it can be automated, it is generally less scalable compared to sputtering.
-
Applications:
- Sputtering: Ideal for applications requiring high-purity thin films, such as in the production of electrical or optical components.
- Electron Beam Evaporation: Commonly used in the manufacturing of solar panels, glass coatings, and other applications where a high deposition rate is beneficial.
In summary, the choice between sputtering and electron beam evaporation depends on the specific requirements of the project, including the desired film properties, substrate complexity, and production scale. Each method has its unique advantages and limitations, making them suitable for different applications within the field of thin film deposition.
Summary Table:
Aspect | Sputtering | Electron Beam Evaporation |
---|---|---|
Mechanism | Uses energized plasma atoms to dislodge target material atoms. | Uses a focused electron beam to vaporize high-temperature materials. |
Vacuum Level | Operates at a lower vacuum level. | Requires a high vacuum environment. |
Deposition Rate | Lower, especially for dielectric materials; higher for pure metals. | Higher, suitable for rapid coating. |
Adhesion & Film Quality | Better adhesion, more uniform coverage, high-purity films. | Strong adhesion, but less uniform coverage on complex surfaces. |
Energy of Deposited Species | Higher energy, leading to better film density and adhesion. | Lower energy, potentially less dense films. |
Film Homogeneity | Greater homogeneity, smaller grain sizes. | Larger grain sizes, less homogeneity. |
Scalability & Automation | Highly scalable and easily automated. | Less scalable compared to sputtering. |
Applications | Ideal for high-purity thin films (e.g., electrical, optical components). | Used in solar panels, glass coatings, and high-deposition-rate applications. |
Need help choosing the right PVD technique for your project? Contact our experts today!