Sputtering and ion plating are both physical vapor deposition (PVD) techniques used to create thin films, but they differ significantly in their mechanisms, processes, and applications. Sputtering involves ejecting material from a target by bombarding it with energetic ions, typically from a reactive gas, and depositing the ejected atoms onto a substrate. In contrast, ion plating uses high electrical currents to vaporize metallic material, and the resulting metal ions are steered onto the substrate while being bombarded with high-energy ions during film growth. This bombardment enhances film density and adhesion, making ion plating suitable for hard-thin films. Sputtering, on the other hand, is known for its ability to coat a wide range of materials, including plastics and glass, due to its lower process temperatures.
Key Points Explained:
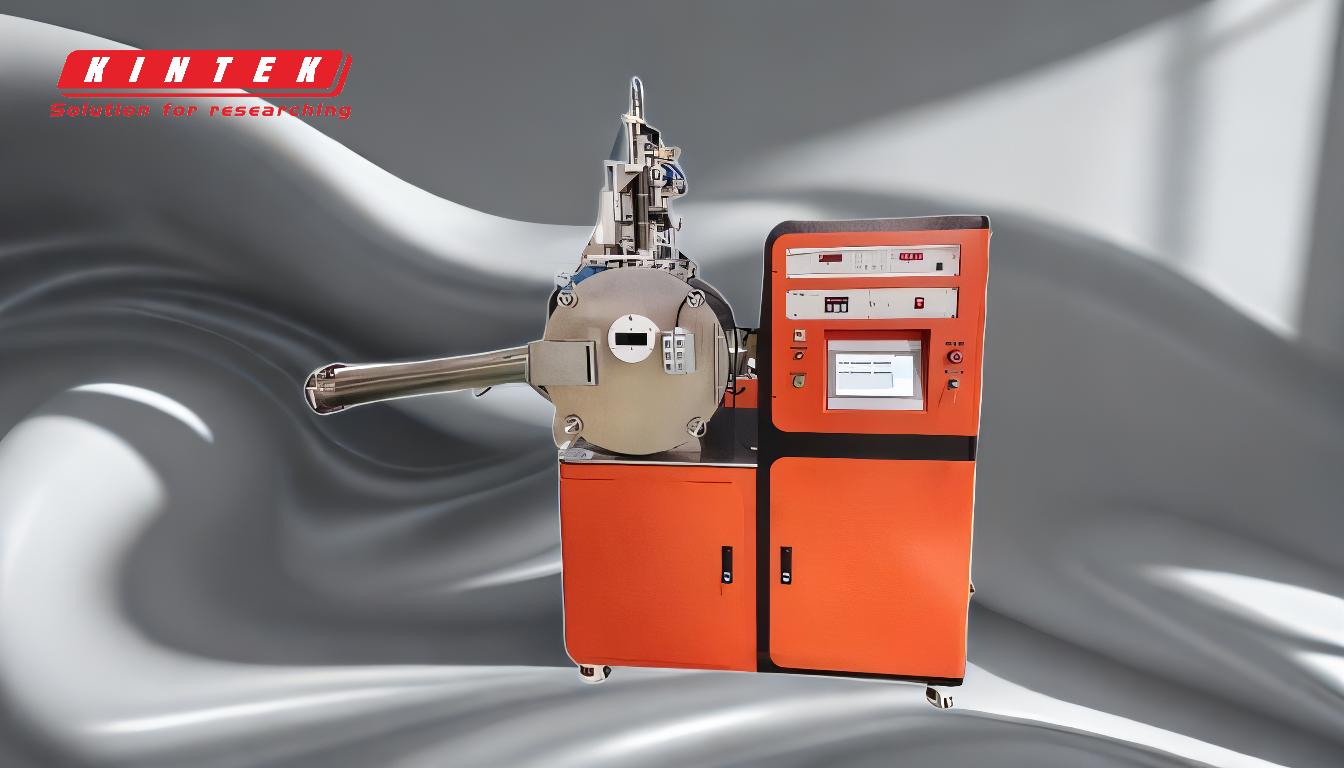
-
Mechanism of Material Vaporization:
- Sputtering: Relies on momentum transfer from bombarding particles (typically gaseous ions) to eject atoms from a target material. The process does not involve melting the material; instead, atoms are physically knocked out of the target.
- Ion Plating: Uses high electrical currents to vaporize metallic material directly. The metal ions are then directed onto the substrate, often accompanied by ion bombardment to enhance film properties.
-
Energy Source and Process Conditions:
- Sputtering: Operates at lower temperatures compared to other PVD methods, making it suitable for temperature-sensitive substrates like plastics and glass. It uses magnetic fields to direct reactive gases, which collide with the target to eject material.
- Ion Plating: Involves higher energy processes, including high electrical currents and ion bombardment. This results in denser films with properties closer to bulk materials, making it ideal for applications requiring hard-thin films.
-
Film Characteristics:
- Sputtering: Produces films with high adhesion, smaller grain sizes, and better homogeneity. The process allows for the deposition of a wide range of materials, including metals, alloys, and compounds.
- Ion Plating: Creates films with enhanced density and adhesion due to continuous or intermittent ion bombardment during deposition. This technique is particularly effective for depositing hard-thin films on compound materials.
-
Applications:
- Sputtering: Widely used in industries requiring precise thin-film coatings, such as semiconductors, optics, and decorative coatings. Its ability to coat temperature-sensitive materials makes it versatile.
- Ion Plating: Preferred for applications requiring durable, hard coatings, such as cutting tools, aerospace components, and wear-resistant surfaces. The ion bombardment during deposition improves film durability and performance.
-
Process Parameters:
- Sputtering: Typically operates at lower vacuum levels and has a lower deposition rate for most materials, except for pure metals. The process is characterized by high adhesion and absorbed gas content in the films.
- Ion Plating: Operates at higher energy levels, with a focus on ion bombardment to enhance film properties. The process is more directional, leading to better control over film thickness and uniformity.
By understanding these key differences, equipment and consumable purchasers can make informed decisions about which technique best suits their specific application needs. Sputtering offers versatility and lower process temperatures, while ion plating provides enhanced film density and durability, making it ideal for demanding applications.
Summary Table:
Aspect | Sputtering | Ion Plating |
---|---|---|
Mechanism | Ejects atoms via momentum transfer from bombarding ions. | Vaporizes material with high electrical currents and uses ion bombardment. |
Energy Source | Lower temperatures, magnetic fields, and reactive gases. | High electrical currents and ion bombardment for denser films. |
Film Characteristics | High adhesion, small grain sizes, and homogeneity. | Enhanced density and adhesion due to ion bombardment. |
Applications | Semiconductors, optics, decorative coatings, and temperature-sensitive materials. | Cutting tools, aerospace components, and wear-resistant surfaces. |
Process Parameters | Lower vacuum levels, lower deposition rates, and high adhesion. | Higher energy levels, directional deposition, and better film uniformity. |
Need help choosing the right PVD technique for your application? Contact our experts today for personalized guidance!