Sputtering and thermal deposition are two distinct thin film deposition techniques used in various industries, each with unique mechanisms, advantages, and applications. Sputtering involves the use of energetic ions to physically dislodge atoms from a target material, which then deposit onto a substrate. This process operates at lower temperatures, making it suitable for heat-sensitive materials. Thermal deposition, on the other hand, relies on heating the target material to generate a vapor stream, which condenses onto the substrate. This method is known for higher deposition rates and shorter run times, making it ideal for applications requiring rapid coating. The choice between these techniques depends on factors such as material compatibility, desired film properties, and production requirements.
Key Points Explained:
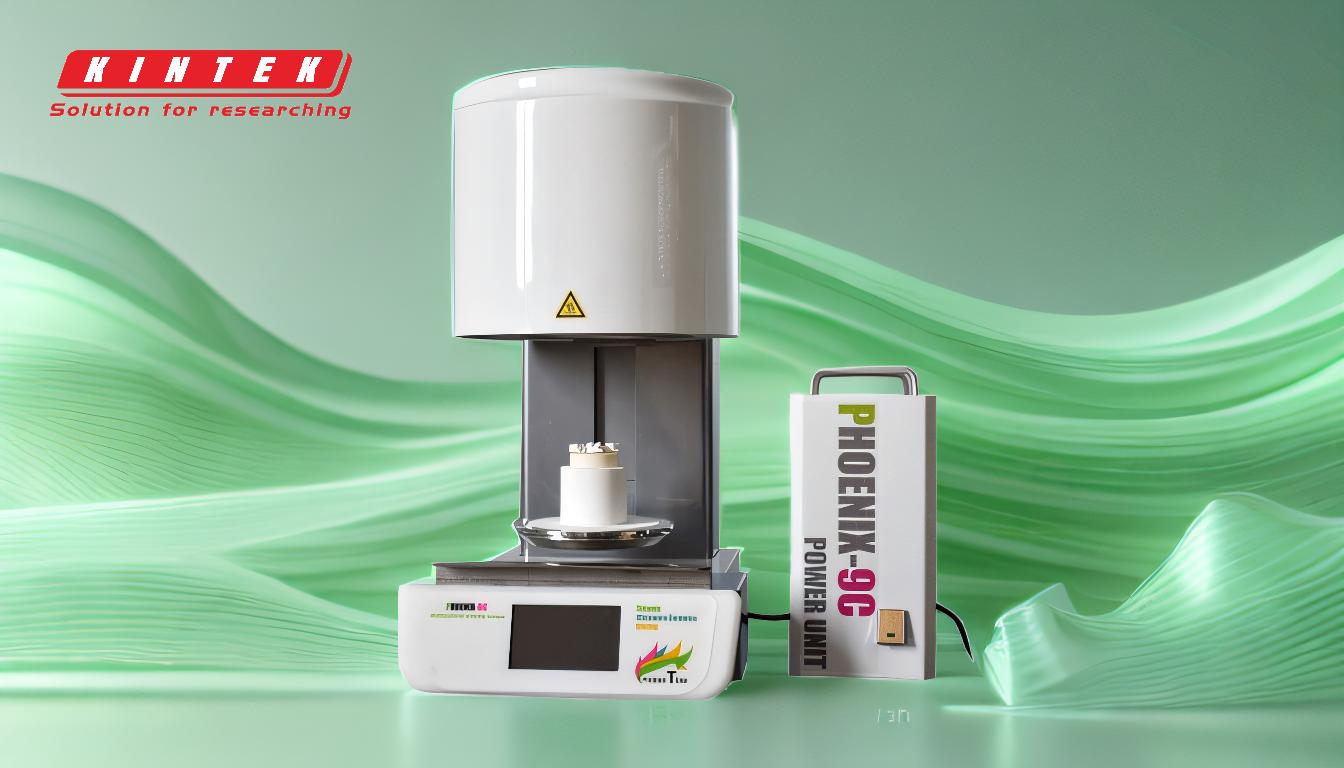
-
Mechanism of Deposition:
-
Sputtering:
- Utilizes a plasma generated by electrically energizing a cathode in a vacuum chamber filled with a controlled gas (typically argon).
- Positively charged gas ions are accelerated toward the target material, physically dislodging atoms or molecules.
- The ejected atoms form a vapor stream that deposits onto the substrate as a thin film.
-
Thermal Deposition:
- Involves heating the target material to its evaporation point, creating a robust vapor stream.
- The vapor condenses onto the substrate, forming a thin film.
- This process is often faster and more efficient for materials that can withstand higher temperatures.
-
Sputtering:
-
Temperature Sensitivity:
-
Sputtering:
- Operates at lower temperatures, making it suitable for coating heat-sensitive materials such as plastics, organics, and certain metals.
- Ideal for applications where thermal stress could damage the substrate or alter material properties.
-
Thermal Deposition:
- Requires higher temperatures to evaporate the target material.
- Best suited for substrates and materials that can tolerate thermal stress, such as metals and ceramics.
-
Sputtering:
-
Deposition Rate and Efficiency:
-
Sputtering:
- Ejects single atoms or small clusters, resulting in a slower deposition rate compared to thermal methods.
- Offers precise control over film thickness and uniformity, making it ideal for applications requiring high-quality coatings.
-
Thermal Deposition:
- Produces a robust vapor stream, enabling higher deposition rates and shorter run times.
- More efficient for large-scale production or applications where speed is critical.
-
Sputtering:
-
Applications:
-
Sputtering:
- Commonly used in electrical and optical production, such as creating thin-film transistors, OLEDs, and reflective coatings.
- Suitable for applications requiring precise control over film properties and compatibility with heat-sensitive substrates.
-
Thermal Deposition:
- Frequently employed in industries like solar panel manufacturing, glass coating, and metal film deposition.
- Ideal for applications where rapid coating and high throughput are essential.
-
Sputtering:
-
Material Compatibility:
-
Sputtering:
- Can deposit a wide range of materials, including metals, alloys, and ceramics, without requiring high temperatures.
- Particularly effective for materials that are difficult to evaporate thermally.
-
Thermal Deposition:
- Limited to materials that can be evaporated without decomposition or degradation.
- Works well with metals and simple compounds that have well-defined evaporation points.
-
Sputtering:
-
Equipment and Process Complexity:
-
Sputtering:
- Requires specialized equipment to generate and control the plasma, making the process more complex and potentially costlier.
- Offers greater flexibility in terms of target materials and substrate compatibility.
-
Thermal Deposition:
- Simpler equipment setup, primarily involving heating elements and vacuum chambers.
- Easier to scale for high-volume production but less versatile in terms of material options.
-
Sputtering:
In summary, sputtering and thermal deposition are complementary techniques, each excelling in specific scenarios. Sputtering is preferred for precision, low-temperature applications, and heat-sensitive materials, while thermal deposition is favored for its speed, efficiency, and suitability for high-temperature-tolerant substrates. The choice between the two depends on the specific requirements of the project, including material properties, desired film characteristics, and production constraints.
Summary Table:
Aspect | Sputtering | Thermal Deposition |
---|---|---|
Mechanism | Uses energetic ions to dislodge atoms from a target material. | Heats target material to create a vapor stream for deposition. |
Temperature Sensitivity | Operates at lower temperatures, ideal for heat-sensitive materials. | Requires higher temperatures, suitable for heat-tolerant substrates. |
Deposition Rate | Slower but offers precise control over film thickness and uniformity. | Faster deposition rates, ideal for high-throughput applications. |
Applications | Electrical/optical production (e.g., OLEDs, thin-film transistors). | Solar panels, glass coating, metal film deposition. |
Material Compatibility | Works with metals, alloys, ceramics, and heat-sensitive materials. | Limited to materials that can be evaporated without degradation. |
Equipment Complexity | Requires specialized plasma-generating equipment, more complex setup. | Simpler setup with heating elements and vacuum chambers. |
Need help choosing the right thin film deposition technique? Contact our experts today for tailored solutions!