Tungsten, while known for its exceptional hardness and high melting point, comes with several disadvantages that limit its use in certain applications. The primary drawbacks include its difficulty in machining, brittleness at low temperatures, and susceptibility to embrittlement and oxidation at high temperatures. These challenges arise from its physical properties, such as high ductile-to-brittle transition temperature (DBTT) and its tendency to compact into diamond tools during machining. Additionally, tungsten heating elements require careful temperature control to prevent embrittlement and oxidation, further complicating its use in high-temperature environments.
Key Points Explained:
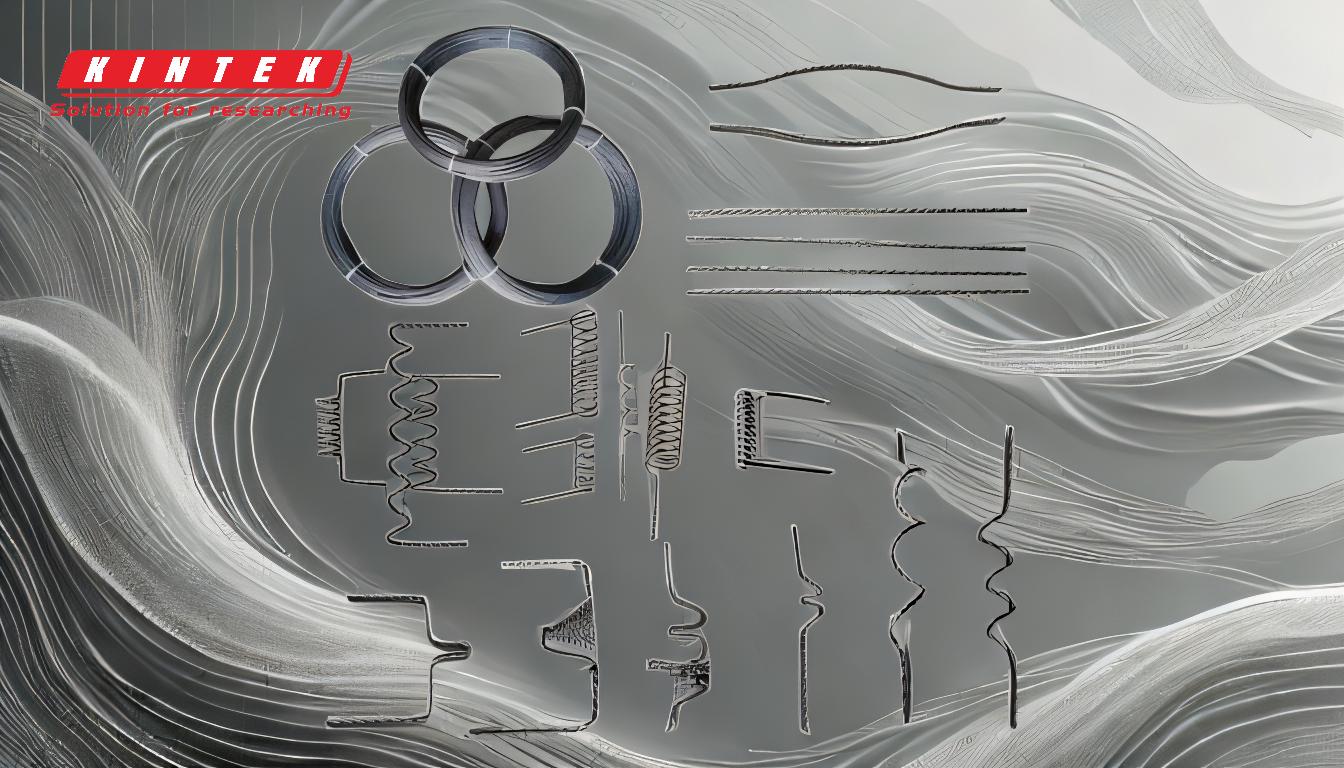
-
Difficulty in Machining:
- Pure tungsten is notoriously difficult to machine. Diamond tools, which are typically effective for machining tungsten carbide, are ineffective for pure tungsten. This is due to a phenomenon called "loading," where the tungsten material compacts into the spaces between the diamonds on the cutting tool. This compaction renders the cutting tool ineffective, making the machining process inefficient and costly.
- Additionally, pure tungsten cannot be drawn over a mandrel or extruded into a tube, limiting its formability and making it challenging to produce complex shapes or components.
-
Brittleness at Low Temperatures:
- Tungsten exhibits a high ductile-to-brittle transition temperature (DBTT), which is typically higher than room temperature. This means that at low temperatures, tungsten becomes brittle and prone to cracking or breaking under stress. This property makes it unsuitable for applications that require flexibility or impact resistance at lower temperatures.
- The brittleness is further exacerbated by impurities or contamination, which can make tungsten even more challenging to handle and work with.
-
Susceptibility to Embrittlement and Oxidation at High Temperatures:
- Tungsten heating elements are particularly vulnerable to embrittlement, mechanical shock, and thermal shock when exposed to high temperatures. This is especially problematic in environments where rapid temperature changes occur, as the material can become brittle and fail.
- Oxidation is another significant issue for tungsten at elevated temperatures. When exposed to air above 500°C (932°F), tungsten oxidizes, leading to degradation of the material. To mitigate this, tungsten heating elements must be operated in a controlled atmosphere or with a ramping temperature control system to avoid embrittlement during cold start-up.
-
Thermal and Mechanical Shock:
- Tungsten's susceptibility to thermal and mechanical shock further limits its use in applications where rapid temperature changes or mechanical stresses are common. The material's brittleness at low temperatures and its tendency to oxidize at high temperatures make it less reliable in environments subject to sudden changes in temperature or mechanical load.
-
Special Handling Requirements:
- Due to its high DBTT and sensitivity to oxidation, tungsten requires special handling and processing techniques. For instance, tungsten heating elements must be carefully controlled to prevent embrittlement during start-up, and they must be protected from exposure to air at high temperatures. These requirements add complexity and cost to the use of tungsten in various applications.
In summary, while tungsten offers several advantageous properties, such as high hardness and melting point, its disadvantages—including difficulty in machining, brittleness at low temperatures, and susceptibility to embrittlement and oxidation at high temperatures—make it a challenging material to work with in many applications. These limitations necessitate careful consideration and specialized handling when using tungsten in industrial or high-temperature environments.
Summary Table:
Disadvantage | Key Details |
---|---|
Difficulty in Machining | - Pure tungsten is hard to machine; diamond tools are ineffective. |
- Limited formability; cannot be drawn or extruded easily. | |
Brittleness at Low Temperatures | - High ductile-to-brittle transition temperature (DBTT). |
- Prone to cracking or breaking under stress at low temperatures. | |
Oxidation at High Temperatures | - Oxidizes above 500°C (932°F), leading to degradation. |
- Requires controlled atmosphere or ramping temperature control. | |
Thermal and Mechanical Shock | - Susceptible to embrittlement and failure under rapid temperature changes. |
Special Handling Requirements | - Needs careful temperature control and protection from air at high temperatures. |
Need help managing tungsten's challenges in your application? Contact our experts today for tailored solutions!