Heat treatment is a critical process in metallurgy that significantly influences the mechanical properties of metallic alloys, including aluminum. By carefully controlling the heating and cooling rates, heat treatment can enhance properties such as hardness, strength, toughness, ductility, and elasticity. These changes are primarily due to alterations in the microstructure of the metal, which affect its overall performance in various applications. Understanding the specific effects of heat treatment on aluminum is essential for optimizing its use in industries ranging from aerospace to automotive.
Key Points Explained:
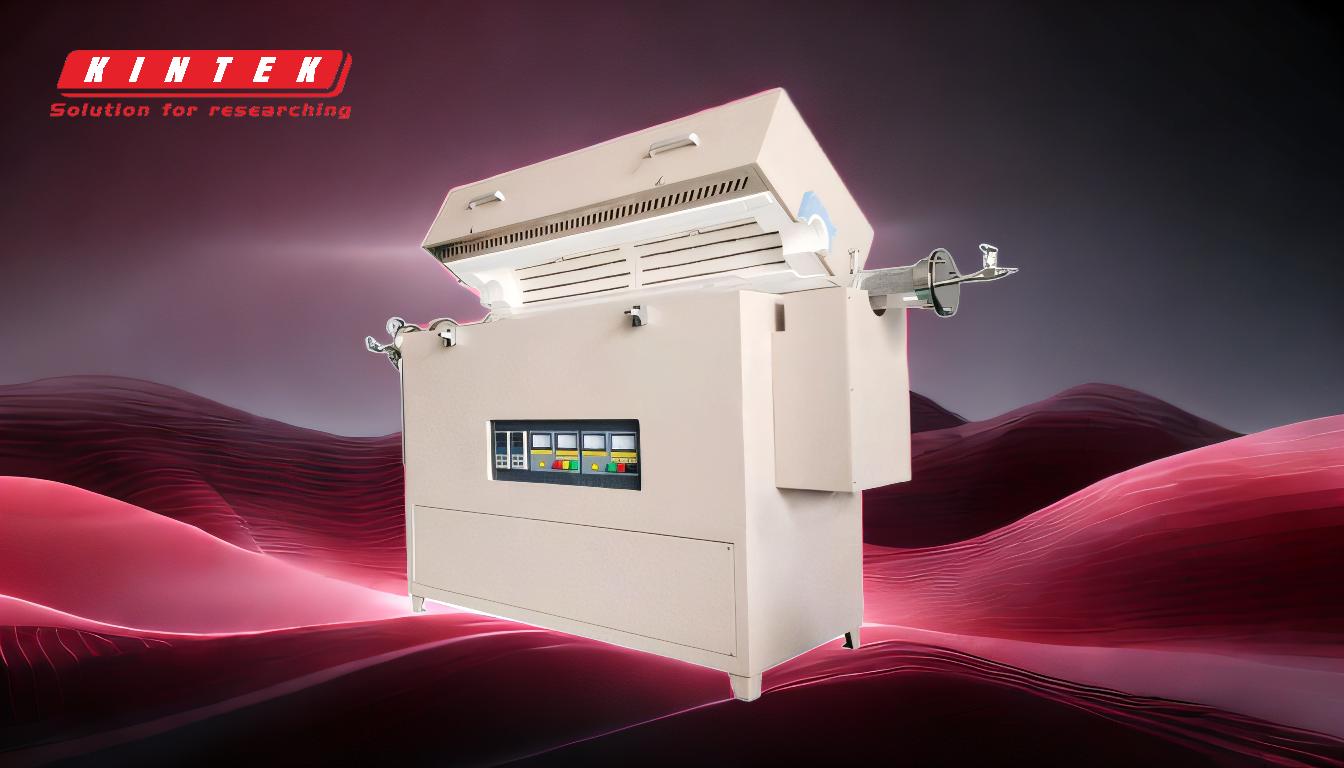
-
Microstructural Changes:
- Heat treatment induces changes in the microstructure of aluminum, which directly impacts its mechanical properties. For instance, processes like annealing can soften the metal by allowing the formation of larger grains, while quenching can harden it by creating a finer grain structure.
-
Hardness and Strength:
- One of the primary effects of heat treatment on aluminum is the enhancement of hardness and strength. Techniques such as precipitation hardening (also known as age hardening) are particularly effective. This process involves heating the aluminum to a specific temperature, holding it there to allow the formation of precipitates, and then cooling it rapidly. The precipitates impede dislocation movement within the metal, thereby increasing its hardness and strength.
-
Toughness and Ductility:
- While heat treatment can increase hardness and strength, it may also affect toughness and ductility. For example, quenching can make aluminum harder but more brittle. To balance these properties, a subsequent tempering process might be employed to reduce brittleness while maintaining a desirable level of hardness.
-
Elasticity:
- The elasticity of aluminum, which is its ability to return to its original shape after deformation, can also be influenced by heat treatment. Processes that refine the grain structure, such as controlled cooling, can enhance elasticity by making the metal more resistant to permanent deformation.
-
Thermal Stability:
- Heat treatment can improve the thermal stability of aluminum, making it more resistant to changes in mechanical properties at elevated temperatures. This is particularly important for applications where the material is exposed to high temperatures, such as in engine components.
-
Application-Specific Optimization:
- Different heat treatment processes are selected based on the intended application of the aluminum. For example, aerospace components may require a combination of high strength and toughness, achieved through specific heat treatment cycles, whereas decorative items might prioritize surface finish and corrosion resistance.
In summary, heat treatment is a versatile and powerful tool for modifying the properties of aluminum to meet specific engineering requirements. By understanding and controlling the microstructural changes induced by heat treatment, manufacturers can tailor aluminum alloys to achieve the optimal balance of hardness, strength, toughness, ductility, and elasticity for their particular applications.
Summary Table:
Effect of Heat Treatment | Key Benefits |
---|---|
Microstructural Changes | Refines grain structure for improved mechanical properties |
Hardness and Strength | Increases hardness and strength through precipitation hardening |
Toughness and Ductility | Balances hardness with reduced brittleness via tempering |
Elasticity | Enhances elasticity through controlled cooling |
Thermal Stability | Improves resistance to high-temperature changes |
Application-Specific Optimization | Tailors properties for aerospace, automotive, and more |
Optimize your aluminum's performance with tailored heat treatment—contact our experts today!