The heating rate in pyrolysis significantly impacts the reaction pathway, product distribution, and overall efficiency of the process. Rapid heating generally leads to reduced char formation and influences the yield and composition of oil and gas products. Conversely, slower heating rates can increase char production and alter the oil yield. Heat transfer is a critical factor, as pyrolysis is an endothermic process requiring sufficient heat to proceed efficiently. Understanding the interplay between heating rate, heat transfer, and other factors like temperature, pressure, and feed rate is essential for optimizing pyrolysis processes for specific applications.
Key Points Explained:
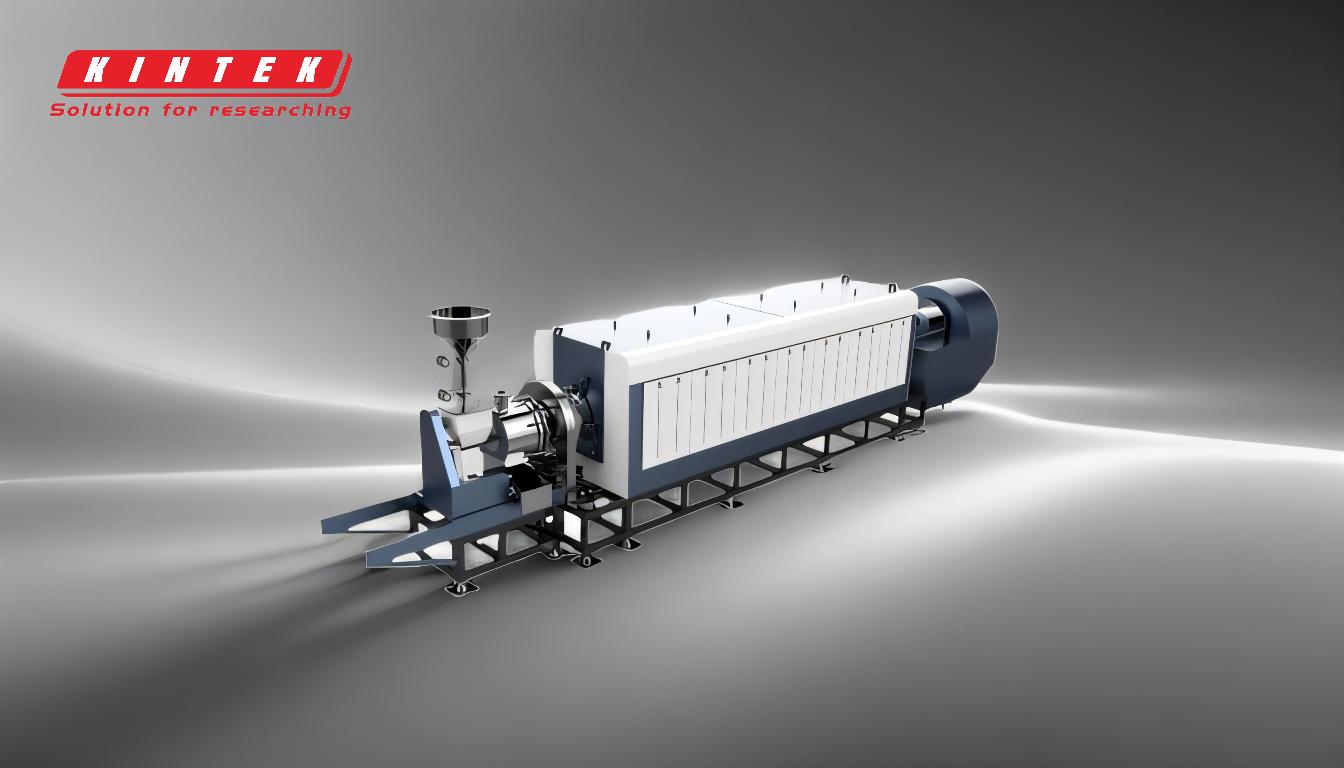
-
Influence of Heating Rate on Product Distribution:
- Rapid Heating: Leads to smaller amounts of char and higher yields of gas and liquid products. This is because rapid heating minimizes secondary reactions that typically lead to char formation.
- Slow Heating: Results in increased char production and potentially lower oil yields. Slower heating allows more time for secondary reactions, which favor char formation.
-
Heat Transfer in Pyrolysis:
- Endothermic Nature: Pyrolysis requires heat to break down organic materials, making efficient heat transfer crucial.
- Heat Transfer Surfaces: Adequate heat transfer surfaces must be provided to ensure the process receives the necessary heat to proceed efficiently. Insufficient heat transfer can lead to incomplete reactions and lower product yields.
-
Interaction with Other Factors:
- Temperature: Higher temperatures generally increase the rate of pyrolysis and can shift product distribution towards more gaseous products.
- Pressure: Elevated pressures can influence the boiling points of the products and the overall reaction kinetics.
- Time: Longer residence times can allow for more complete reactions but may also increase the likelihood of secondary reactions leading to char formation.
- Atmosphere: The presence of reactive gases (e.g., oxygen) can alter the pyrolysis pathway, potentially leading to combustion rather than pure pyrolysis.
- Feed Rate: The rate at which material is fed into the pyrolysis reactor can affect heat distribution and the overall efficiency of the process.
-
Optimization for Specific Applications:
- Char Production: If the goal is to maximize char production, slower heating rates and longer residence times may be beneficial.
- Oil and Gas Production: For higher yields of oil and gas, faster heating rates and optimized heat transfer are crucial.
Understanding these factors allows for the design and operation of pyrolysis systems tailored to specific product goals, whether they be maximizing char, oil, or gas yields.
Summary Table:
Factor | Impact on Pyrolysis |
---|---|
Rapid Heating | Reduces char formation, increases gas and liquid yields. |
Slow Heating | Increases char production, may lower oil yields. |
Heat Transfer | Crucial for efficient endothermic reactions; insufficient heat leads to incomplete pyrolysis. |
Temperature | Higher temperatures increase pyrolysis rate and favor gas production. |
Pressure | Alters boiling points and reaction kinetics. |
Time | Longer residence times may increase char formation. |
Atmosphere | Reactive gases (e.g., oxygen) can shift pyrolysis to combustion. |
Feed Rate | Affects heat distribution and process efficiency. |
Unlock the full potential of your pyrolysis process—contact our experts today for tailored solutions!