The efficiency of ball milling is a measure of how effectively a ball mill can grind materials into the desired particle size while minimizing energy consumption and time. It is influenced by multiple factors, including the design of the mill, the properties of the material being ground, and the operational parameters. Key factors include the drum diameter, length-to-diameter ratio, ball size and density, rotation speed, feed rate, and the hardness of the material. Smaller balls and longer grinding times are often required for finer particles, while optimal productivity is achieved with a specific drum diameter-to-length ratio (1.56–1.64). Understanding these factors helps in optimizing the milling process for better efficiency.
Key Points Explained:
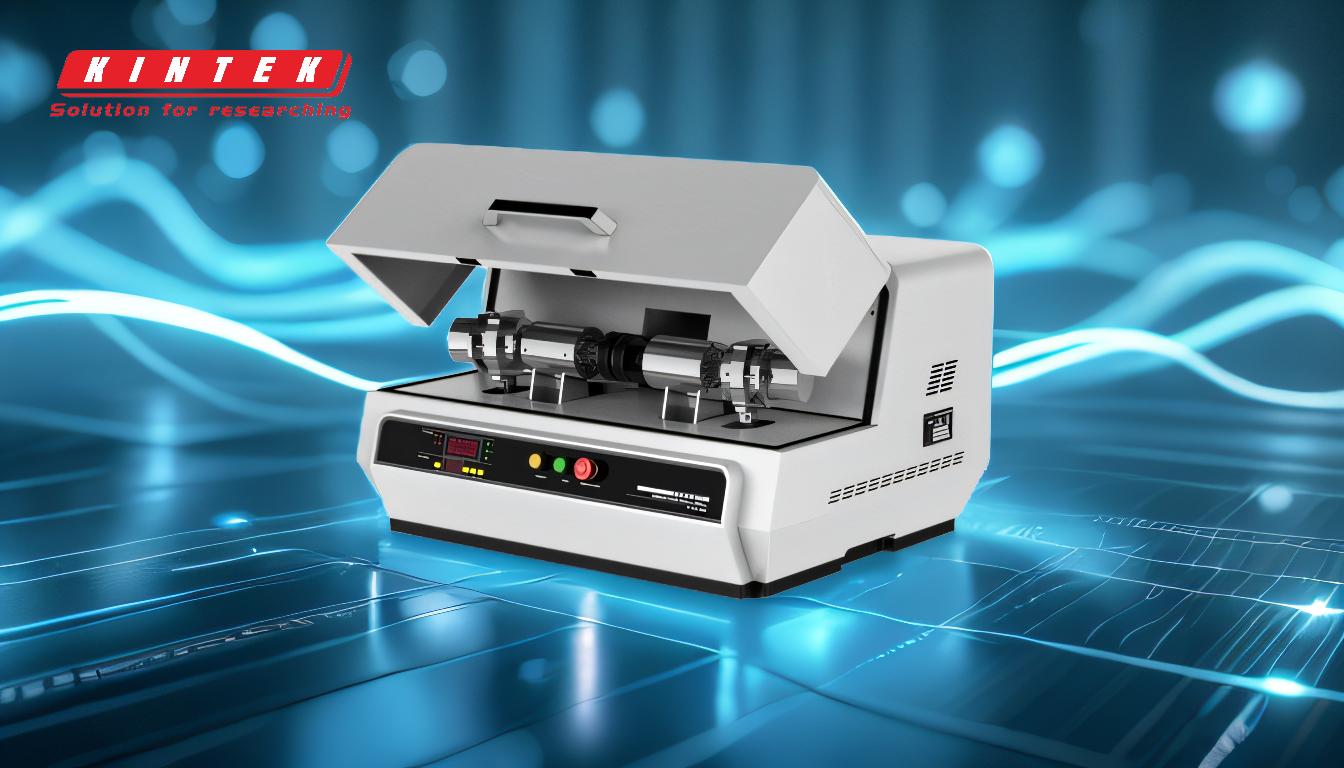
-
Factors Influencing Ball Milling Efficiency
- Residence Time: The time material spends in the mill chamber affects the degree of grinding. Longer residence times generally lead to finer particles but may reduce throughput.
- Ball Characteristics: The size, density, and number of balls impact grinding efficiency. Smaller balls are better for producing finer particles, while larger balls are more effective for coarse grinding.
- Material Properties: The hardness and nature of the grinding material determine the energy required for milling. Harder materials require more energy and longer grinding times.
- Feed Rate and Level: The rate at which material is fed into the mill and the level of material in the vessel influence grinding efficiency. Overloading or underloading can reduce efficiency.
- Rotation Speed: The speed of the mill cylinder affects the kinetic energy of the balls. Optimal speed ensures effective grinding without excessive wear or energy waste.
-
Design Parameters Affecting Efficiency
- Drum Diameter and Length-to-Diameter Ratio: The diameter of the drum and its ratio to length (optimal L:D ratio is 1.56–1.64) significantly impact productivity. A well-designed mill ensures efficient grinding and energy use.
- Armor Surface Shape: The shape of the mill's interior surface (armor) influences the movement of balls and material, affecting grinding efficiency.
- Timely Removal of Ground Product: Efficient removal of ground material prevents over-grinding and ensures consistent product quality.
-
Operational Considerations
- Grinding Time: Longer grinding times are required for finer particles, but this must be balanced against energy consumption and throughput.
- Ball Filling and Sizes: Proper filling of the mill with balls and selecting the right sizes for the material being ground are critical for efficient milling.
- Rotation Speed: Adjusting the rotation speed to match the material and desired particle size ensures optimal grinding without unnecessary energy expenditure.
-
Practical Implications for Purchasers
- Material-Specific Optimization: Understanding the material properties helps in selecting the right mill design and operational parameters.
- Energy Efficiency: Balancing grinding time, ball size, and rotation speed can reduce energy consumption and operational costs.
- Throughput and Quality: Optimizing feed rate, residence time, and product removal ensures consistent quality and high throughput.
By considering these factors, purchasers can select and operate ball mills more effectively, ensuring high efficiency and cost-effectiveness in grinding processes.
Summary Table:
Factor | Impact on Efficiency |
---|---|
Residence Time | Longer times produce finer particles but may reduce throughput. |
Ball Characteristics | Smaller balls for fine particles; larger balls for coarse grinding. |
Material Properties | Harder materials require more energy and longer grinding times. |
Feed Rate and Level | Overloading or underloading reduces efficiency. |
Rotation Speed | Optimal speed ensures effective grinding without excessive energy waste. |
Drum Design | Optimal L:D ratio (1.56–1.64) enhances productivity and energy use. |
Grinding Time | Longer times for finer particles, balanced against energy consumption and throughput. |
Need help optimizing your ball milling process? Contact our experts today for tailored solutions!