The efficiency of plastic pyrolysis is influenced by several factors, including the composition and quality of the plastic waste, the pyrolysis technology employed, and the operational parameters of the pyrolysis furnace. Key factors such as temperature, residence time, and pressure within the furnace play a critical role in determining the efficiency and yield of the pyrolysis process. Additionally, the type of plastic, its moisture content, and cleanliness significantly impact the conversion efficiency and the quality of the end products. Proper control and optimization of these factors are essential for achieving high efficiency and producing desirable pyrolysis products.
Key Points Explained:
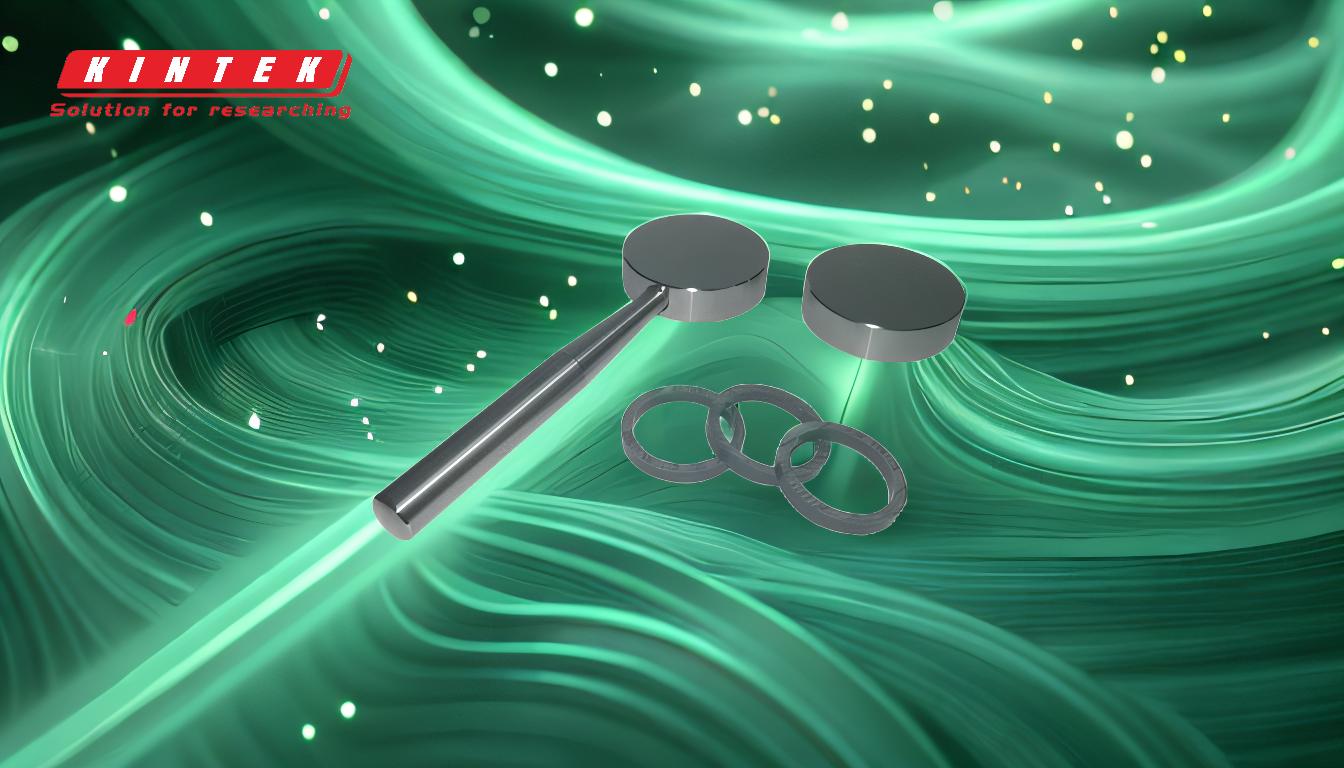
-
Composition and Quality of Plastic Waste:
- The efficiency of plastic pyrolysis is highly dependent on the type and quality of the plastic being processed. Pure, dry, and clean waste plastic generally yields higher-quality pyrolysis products.
- Contaminants, moisture, and mixed plastic types can reduce the efficiency of the process, leading to lower yields and poorer quality end products.
-
Pyrolysis Technology:
- The specific pyrolysis technology used can significantly impact the efficiency of the process. Advanced technologies that allow for better control of temperature, pressure, and residence time can enhance the conversion efficiency.
- Different technologies may be better suited for specific types of plastic waste, and selecting the appropriate technology is crucial for optimizing efficiency.
-
Operational Parameters:
- Temperature: The temperature within the pyrolysis furnace is a critical factor. Optimal temperatures must be maintained to ensure efficient degradation of the plastic into gas and other products.
- Residence Time: The amount of time the plastic spends in the furnace affects the extent of pyrolysis. Longer residence times can lead to more complete degradation but must be balanced against energy consumption and throughput.
- Pressure: The pressure inside the furnace can influence the pyrolysis process. Proper pressure control is necessary to ensure efficient conversion and to manage the release of gases.
-
Moisture Content:
- The moisture content of the plastic waste can affect the pyrolysis process. High moisture levels can lead to energy losses and reduced efficiency, as energy is used to evaporate the water rather than degrade the plastic.
- Pre-drying the plastic waste can improve the efficiency of the pyrolysis process.
-
Type of Plastic:
- Different types of plastics have varying thermal properties and degradation behaviors. For example, polyethylene and polypropylene are more easily pyrolyzed compared to PVC, which can release harmful gases.
- The type of plastic being processed will influence the choice of pyrolysis conditions and the expected efficiency.
-
Cleanliness of Waste Plastic:
- The presence of impurities, such as dirt, metals, or other non-plastic materials, can hinder the pyrolysis process. Cleaner waste plastic results in higher efficiency and better-quality pyrolysis products.
- Pre-processing steps, such as sorting and cleaning, can enhance the overall efficiency of the pyrolysis process.
-
Control and Maintenance:
- Proper operation and maintenance of the pyrolysis furnace are crucial for maintaining high efficiency. Regular maintenance ensures that the furnace operates at optimal conditions, preventing issues such as clogging or temperature fluctuations.
- Monitoring and controlling the operational parameters in real-time can help in adjusting the process to maximize efficiency.
-
End Product Quality:
- The efficiency of the pyrolysis process is also measured by the quality of the end products, such as pyrolysis oil, gas, and char. High-quality products are indicative of an efficient process.
- The desired end products can influence the choice of pyrolysis conditions and the overall efficiency of the process.
In summary, the efficiency of plastic pyrolysis is a multifaceted issue that depends on the quality and type of plastic waste, the pyrolysis technology used, and the precise control of operational parameters. By optimizing these factors, it is possible to achieve high efficiency and produce valuable pyrolysis products.
Summary Table:
Factor | Impact on Efficiency |
---|---|
Composition & Quality | Pure, dry, and clean plastic yields higher-quality products; contaminants reduce efficiency. |
Pyrolysis Technology | Advanced tech enhances control of temperature, pressure, and residence time. |
Operational Parameters | Optimal temperature, residence time, and pressure are critical for efficient pyrolysis. |
Moisture Content | High moisture reduces efficiency; pre-drying improves results. |
Type of Plastic | Polyethylene and polypropylene are easier to pyrolyze than PVC. |
Cleanliness | Impurities hinder the process; cleaner waste improves efficiency. |
Control & Maintenance | Proper operation and maintenance ensure consistent high efficiency. |
End Product Quality | High-quality products indicate an efficient process. |
Optimize your plastic pyrolysis process for maximum efficiency—contact our experts today!