Size reduction is a critical process in various industries, and its efficiency is influenced by several factors. Among these, moisture content, the number of grinding cycles, and residence time in the grinding process are key determinants. Moisture content affects material properties like hardness and stickiness, which directly impact the ease of size reduction. Additionally, the number of grinding cycles and the residence time in the grinding process dictate the final particle size and the specific surface area of the material, such as ground tire rubber (GTR). These factors collectively determine the effectiveness and efficiency of the size reduction process.
Key Points Explained:
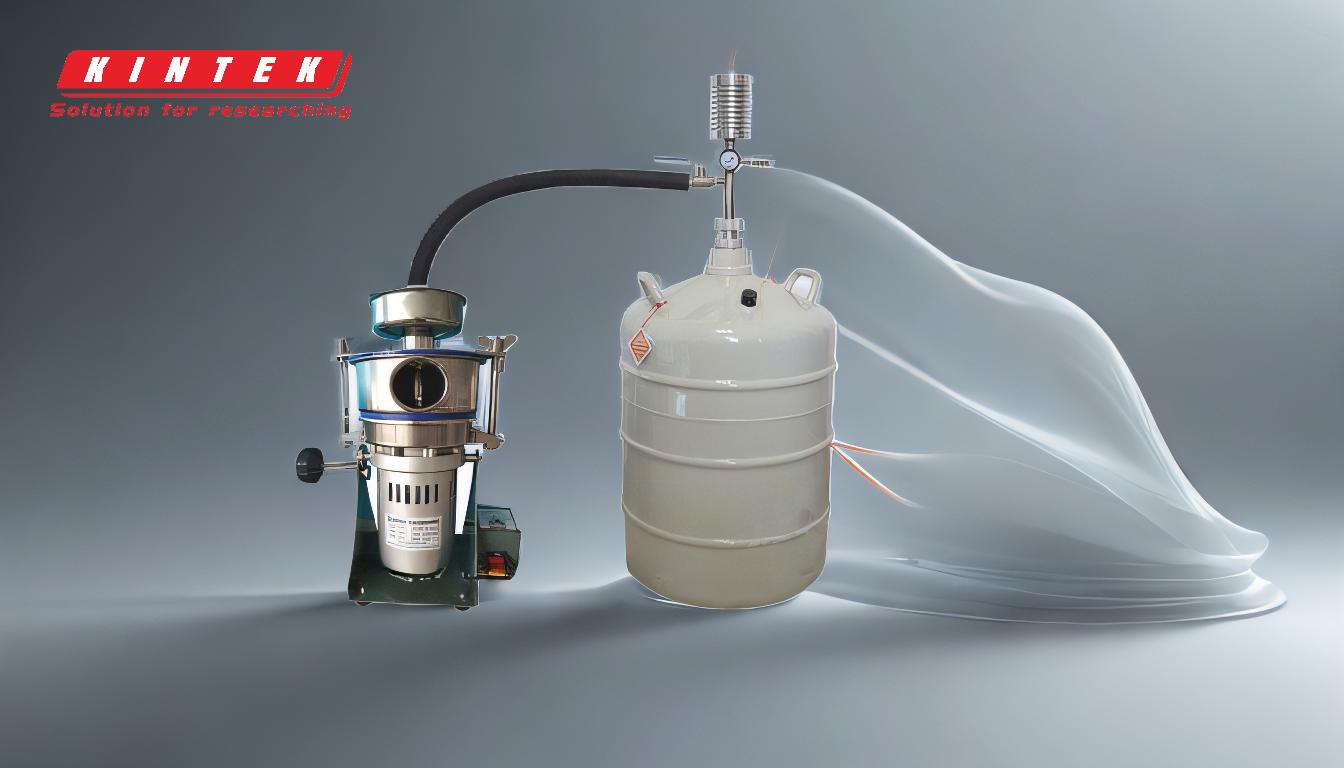
-
Moisture Content:
- Impact on Material Properties: Moisture content significantly influences the physical properties of the material being processed. High moisture levels can increase the stickiness of the material, making it more difficult to grind. Conversely, materials with lower moisture content are typically harder and more brittle, facilitating easier size reduction.
- Effect on Grinding Efficiency: The presence of moisture can lead to clogging of grinding equipment, reducing its efficiency. It can also cause the material to adhere to the grinding surfaces, which can hinder the grinding process and result in uneven particle sizes.
-
Number of Grinding Cycles:
- Determination of Final Particle Size: The number of grinding cycles is directly proportional to the degree of size reduction. More grinding cycles generally result in smaller particle sizes. However, there is a point of diminishing returns where additional cycles may not significantly reduce particle size but can increase energy consumption and processing time.
- Influence on Specific Surface Area: Increasing the number of grinding cycles not only reduces particle size but also increases the specific surface area of the material. This is particularly important in applications where the surface area of the particles is a critical factor, such as in the production of ground tire rubber (GTR).
-
Residence Time in the Grinding Process:
- Effect on Particle Size Distribution: The residence time, or the duration that the material spends in the grinding process, affects the uniformity of the particle size distribution. Longer residence times can lead to more uniform particle sizes, as the material is subjected to grinding forces for a more extended period.
- Impact on Energy Consumption: Longer residence times can also lead to higher energy consumption. It is essential to balance the residence time with the desired particle size and energy efficiency to optimize the grinding process.
-
Interplay Between Factors:
- Synergistic Effects: The factors affecting size reduction do not operate in isolation. For example, the optimal number of grinding cycles may vary depending on the moisture content of the material. Similarly, the residence time may need to be adjusted based on the hardness and stickiness of the material, which are influenced by moisture content.
- Process Optimization: Understanding the interplay between moisture content, grinding cycles, and residence time is crucial for optimizing the size reduction process. By carefully controlling these factors, it is possible to achieve the desired particle size and specific surface area while minimizing energy consumption and processing time.
In conclusion, the efficiency and effectiveness of size reduction are influenced by a combination of factors, including moisture content, the number of grinding cycles, and residence time in the grinding process. By understanding and controlling these factors, it is possible to optimize the size reduction process to meet specific industrial requirements.
Summary Table:
Factor | Impact on Size Reduction | Key Considerations |
---|---|---|
Moisture Content | Affects material hardness and stickiness, influencing grinding ease and equipment efficiency. | High moisture increases stickiness; low moisture enhances brittleness. |
Grinding Cycles | Determines final particle size and specific surface area. | More cycles reduce particle size but may increase energy consumption. |
Residence Time | Influences particle size distribution and energy efficiency. | Longer residence time ensures uniformity but may raise energy costs. |
Interplay of Factors | Synergistic effects optimize particle size and energy use. | Balance moisture, cycles, and residence time for optimal results. |
Ready to optimize your size reduction process? Contact our experts today for tailored solutions!