The filling ratio for a ball mill refers to the percentage of the mill's volume that is occupied by grinding balls and the material being processed. This ratio is critical for optimizing milling efficiency and productivity. Generally, the filling ratio should not exceed 30–35% of the mill's volume to avoid collisions between rising and falling balls, which can reduce efficiency. Additionally, the mass ratio of grinding balls to material should ideally be above 5:1, and the total volume filled with balls and material should not exceed 80% of the mill's volume, with 40%-60% being optimal. These parameters ensure effective grinding while maintaining operational efficiency.
Key Points Explained:
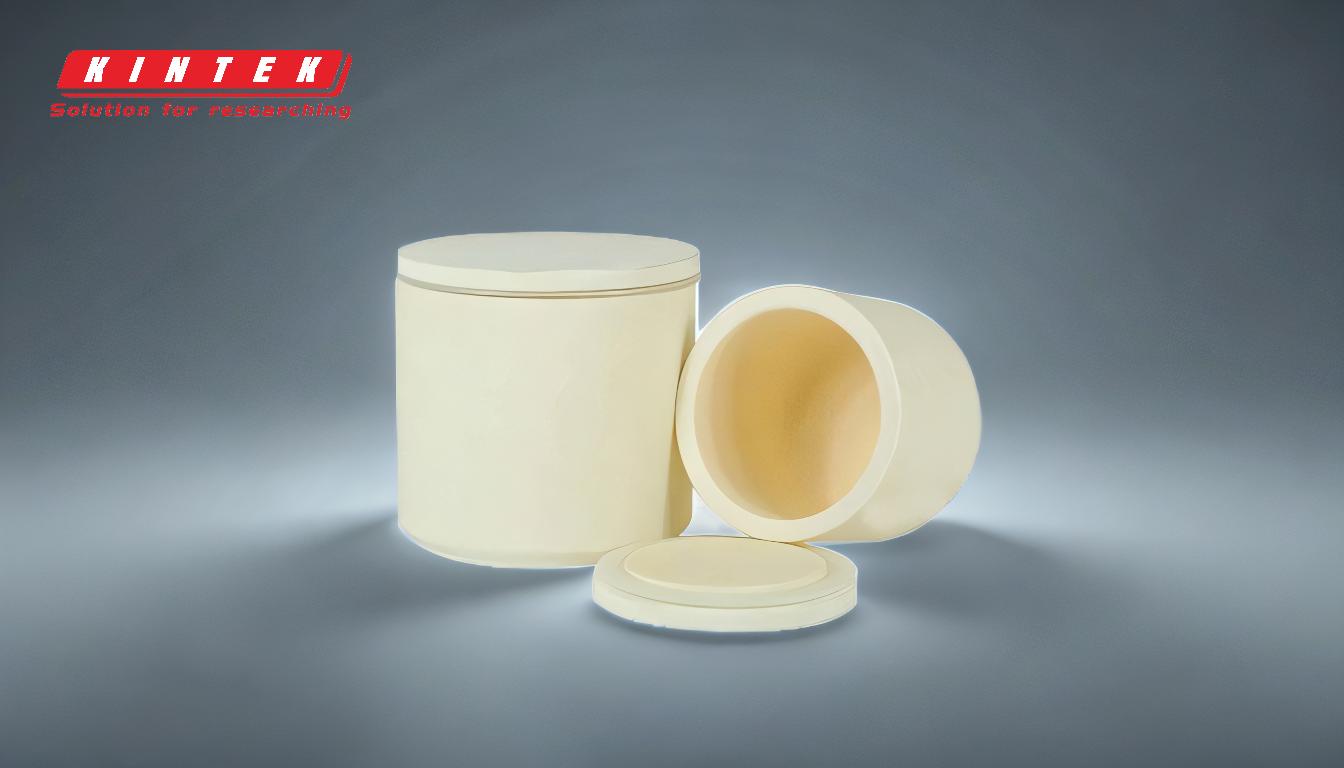
-
Definition of Filling Ratio:
- The filling ratio is the percentage of the ball mill's volume occupied by grinding balls and the material being processed. It is a critical factor in determining the efficiency and productivity of the milling process.
-
Optimal Filling Ratio for Balls:
- The filling ratio for grinding balls should generally not exceed 30–35% of the mill's volume. Exceeding this limit can lead to inefficiencies, as rising balls may collide with falling ones, reducing the overall effectiveness of the grinding process.
-
Mass Ratio of Grinding Balls to Material:
- The mass ratio of grinding balls to the material being processed should ideally be above 5:1. This ensures that there are enough balls to effectively grind the material, leading to better milling results.
-
Total Volume Occupied by Balls and Material:
- The total volume occupied by grinding balls and material should not exceed 80% of the ball mill's volume. A range of 40%-60% is typically considered optimal for achieving efficient grinding while maintaining operational stability.
-
Factors Influencing Milling Efficiency:
- Several factors can influence the degree of milling in a ball mill, including:
- Residence Time: The time the material spends in the mill chamber.
- Ball Size, Density, and Number: Larger or denser balls can increase grinding efficiency, but the number must be balanced to avoid overfilling.
- Nature of the Grinding Material: Harder materials may require more balls or a higher filling ratio.
- Feed Rate and Level: Consistent feed rates and levels help maintain optimal grinding conditions.
- Rotation Speed: The speed at which the mill rotates affects the movement of the balls and the grinding efficiency.
- Several factors can influence the degree of milling in a ball mill, including:
-
Impact of Overfilling:
- Overfilling the mill with balls can lead to inefficiencies, such as increased collisions between balls, which can reduce the overall grinding efficiency. It can also lead to uneven grinding and potential damage to the mill's interior.
-
Practical Considerations for Optimal Filling:
- When determining the optimal filling ratio, it is important to consider the specific requirements of the material being processed and the desired fineness of the grind. Adjustments may be necessary based on the material's hardness, feed rate, and other operational parameters.
By adhering to these guidelines, operators can ensure that their ball mills operate efficiently, producing the desired grinding results while minimizing wear and tear on the equipment.
Summary Table:
Parameter | Optimal Range | Key Insights |
---|---|---|
Filling Ratio for Balls | 30–35% of mill volume | Avoid collisions and inefficiencies by staying within this range. |
Mass Ratio (Balls to Material) | Above 5:1 | Ensures effective grinding with sufficient balls for material processing. |
Total Volume (Balls + Material) | 40%-60% of mill volume | Balances grinding efficiency and operational stability. |
Factors Influencing Efficiency | Residence time, ball size, material hardness, feed rate, rotation speed | Adjust parameters based on material and desired grind fineness. |
Need help optimizing your ball mill's filling ratio? Contact our experts today for tailored solutions!