The pyrolysis reactor is a critical component in the pyrolysis process, serving as the core unit where waste materials such as plastics, rubber, tires, and sludge are thermally decomposed in an oxygen-free, high-temperature environment. Its primary function is to convert these waste materials into valuable products like fuel oil, syngas, and biochar, while minimizing environmental pollution. The reactor operates under controlled conditions, relying on external heat sources and thermodynamic principles to ensure efficient and safe processing. Different types of reactors, such as drum and rotary reactors, are designed to optimize specific pyrolysis processes, improve feedstock heating, and enhance product yields. The design and quality of the reactor directly impact the efficiency, safety, and environmental performance of the pyrolysis system.
Key Points Explained:
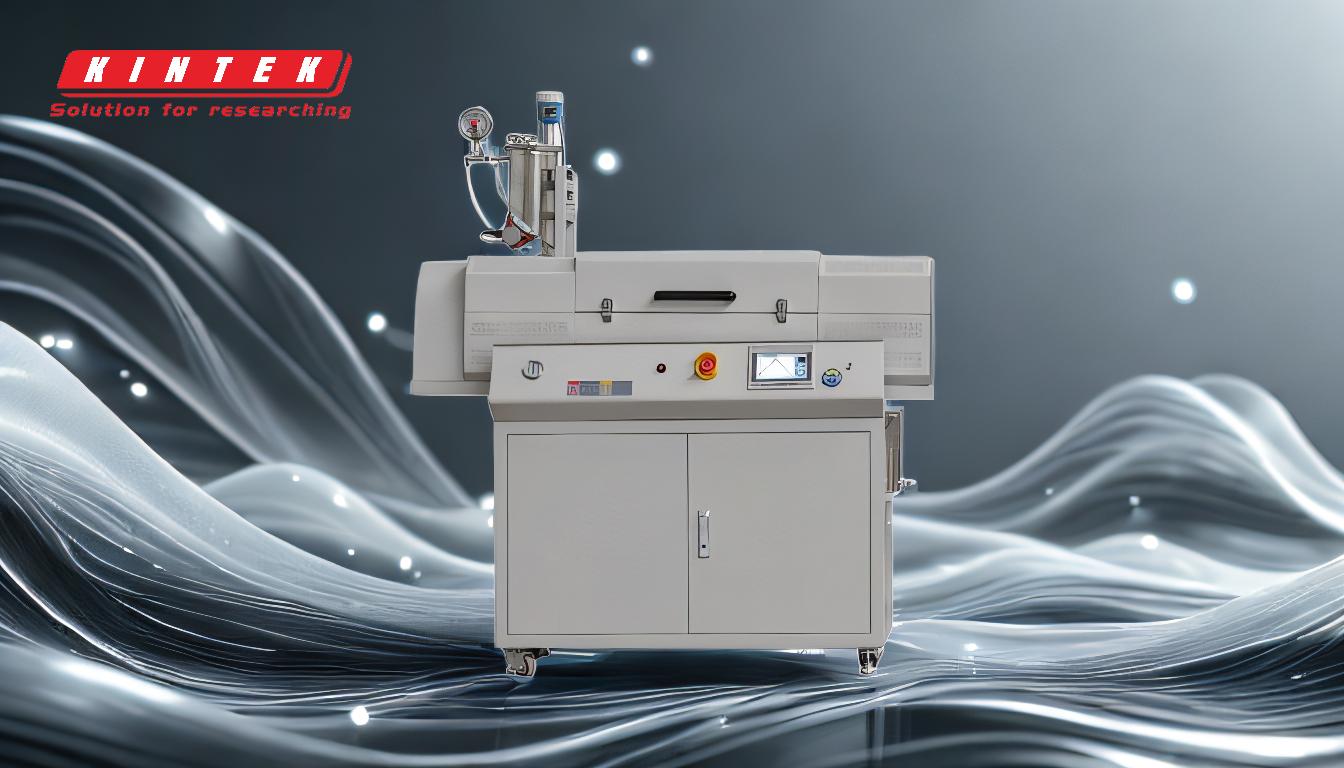
-
Core Function of the Pyrolysis Reactor:
- The pyrolysis reactor is the central unit where thermal decomposition of waste materials occurs. It operates in an oxygen-free environment at high temperatures (typically between 475°C and 550°C) to break down materials like plastics, rubber, tires, and sludge.
- This process transforms waste into useful products such as fuel oil, syngas, and biochar, contributing to waste recycling and environmental sustainability.
-
Types of Pyrolysis Reactors:
- Drum Reactor: A drum-shaped vessel that rotates internally to circulate heat. It is particularly effective for slow pyrolysis of biomass, producing syngas and biochar. The drum reactor is housed in a furnace that supplies the necessary heat.
- Rotary Reactor: Operates in a horizontal 360-degree rotation mode, ensuring even heating of raw materials. This design improves pyrolysis efficiency, increases oil yield, and reduces processing time. It is ideal for semi-continuous and small-scale pyrolysis systems.
-
Operational Principles:
- The reactor relies on an external heat source to maintain the required high temperatures. It operates as a closed system, adhering to thermodynamic principles to ensure efficient heat transfer and material decomposition.
- The rotation of the reactor (driven by a motor) ensures uniform heating of the feedstock, which is essential for achieving consistent product quality and maximizing yields.
-
Environmental and Economic Benefits:
- By converting waste into valuable products, pyrolysis reactors help reduce landfill waste and mitigate environmental pollution. The process supports a circular economy by enabling the reuse of materials that would otherwise contribute to environmental degradation.
- The production of fuel oil and syngas from waste materials provides an alternative energy source, reducing reliance on fossil fuels and promoting energy sustainability.
-
Impact of Reactor Design on Performance:
- The quality and design of the reactor are critical for the overall performance of the pyrolysis system. A well-designed reactor ensures efficient heat transfer, uniform feedstock heating, and optimal product yields.
- Safety and environmental protection are also influenced by reactor design. Proper sealing and robust construction prevent leaks and emissions, ensuring safe operation and compliance with environmental regulations.
-
Role in the Pyrolysis Production Line:
- The reactor is the main engine of the pyrolysis plant, dictating the efficiency and effectiveness of the entire production line. Its type and design determine the system's ability to handle different feedstocks, achieve desired product outputs, and maintain operational safety.
- Advanced reactor designs, such as those with continuous rotation mechanisms, enhance the longevity of the equipment and improve the overall pyrolysis rate, making the process more economically viable.
In summary, the pyrolysis reactor is a vital component in waste-to-energy systems, enabling the conversion of waste materials into valuable resources. Its design, operation, and efficiency are key to achieving environmental and economic benefits while ensuring safe and sustainable waste management.
Summary Table:
Aspect | Details |
---|---|
Core Function | Converts waste (plastics, rubber, tires, sludge) into fuel oil, syngas, biochar. |
Types of Reactors | Drum Reactor: Slow pyrolysis for biomass; Rotary Reactor: Efficient oil yield. |
Operational Principles | High-temperature, oxygen-free environment; external heat source; rotation. |
Benefits | Reduces landfill waste, mitigates pollution, supports circular economy. |
Design Impact | Ensures efficiency, safety, and environmental compliance. |
Learn how a pyrolysis reactor can revolutionize your waste management—contact us today!