The growth rate of chemical vapor deposition (CVD) is influenced by various factors, including the type of material being deposited, process parameters (such as temperature, pressure, and gas flow rates), and the specific CVD technique used. CVD is known for its high deposition rates, which make it suitable for industrial applications requiring uniform and high-quality thin films. The process's versatility and ability to produce dense, pure films at relatively high rates are key advantages. However, the exact growth rate can vary significantly depending on the specific application and materials involved.
Key Points Explained:
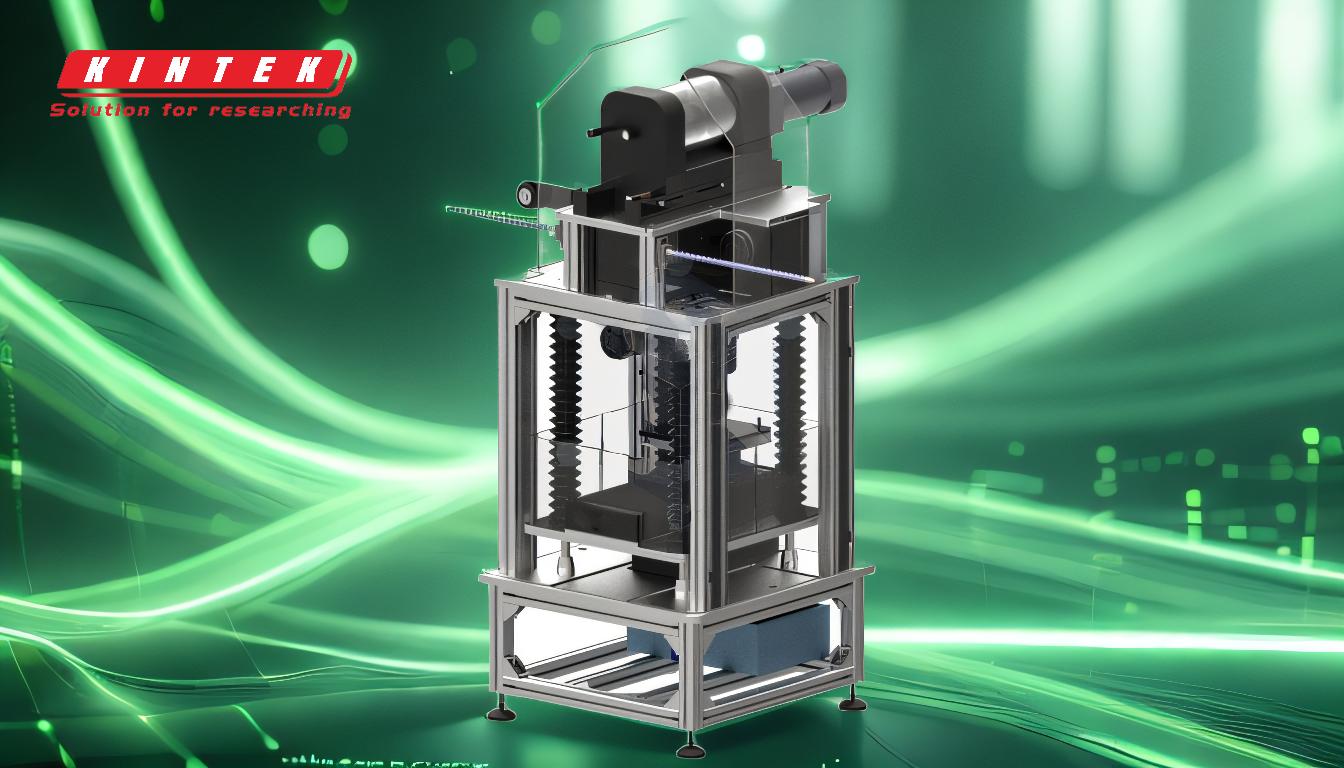
-
Definition and Process of CVD:
- Chemical vapor deposition (CVD) is a manufacturing process that deposits materials onto a surface or substrate using vacuum technology. It involves exposing a workpiece to particulate chemicals in a vacuumed environment, where a chemical reaction occurs, hardening the chemicals on the surface. This process is widely used for creating thin films and coatings.
-
Factors Influencing Growth Rate:
- Temperature: Higher temperatures generally increase the reaction rate, leading to faster deposition. However, excessively high temperatures can degrade the substrate or cause unwanted reactions.
- Pressure: Lower pressures often enhance the uniformity of the deposition but may reduce the overall growth rate.
- Gas Flow Rates: Optimal gas flow rates are crucial for maintaining a consistent supply of reactants, which directly impacts the deposition rate.
- Material Properties: Different materials have varying deposition rates due to their unique chemical and physical properties.
-
Advantages of CVD Affecting Growth Rate:
- High Versatility: CVD can deposit a wide variety of materials, which allows for tailored growth rates depending on the application.
- Uniform Coating: The process provides uniform coating, which is essential for consistent growth rates across the substrate.
- High Purity and Denseness: The ability to produce high-purity and dense films at high deposition rates makes CVD suitable for demanding applications.
- Non-Line-of-Sight Process: CVD can evenly coat components with complex shapes, ensuring consistent growth rates even on intricate surfaces.
-
Applications and Growth Rate Variability:
- Electrical Circuits: CVD is ideal for producing ultra-thin layers required in electrical circuits, where precise control over growth rates is necessary.
- Industrial Coatings: The high deposition rate and good adhesion properties make CVD suitable for industrial coatings, where rapid and uniform growth is essential.
- Nanoparticles and Thin Films: The ability to create pure thin films or nanoparticles at high deposition rates is a significant advantage in nanotechnology and materials science.
-
Comparison with Other Deposition Techniques:
- Affordability and Versatility: Compared to other deposition techniques, CVD is relatively affordable and versatile, offering high deposition rates with commendable adhesion.
- Scalability: The simplicity in scaling up CVD processes makes it attractive for industrial applications requiring consistent and high growth rates.
In summary, the growth rate of chemical vapor deposition is highly dependent on process parameters and material properties. Its advantages, such as high versatility, uniform coating, and high purity, contribute to its ability to achieve rapid and consistent deposition rates, making it a preferred choice for various industrial and technological applications.
Summary Table:
Factor | Impact on Growth Rate |
---|---|
Temperature | Higher temperatures increase reaction rates, but excessive heat can degrade substrates. |
Pressure | Lower pressures enhance uniformity but may reduce overall growth rate. |
Gas Flow Rates | Optimal flow rates ensure consistent reactant supply, directly affecting deposition rate. |
Material Properties | Different materials have unique deposition rates due to their chemical and physical traits. |
CVD Technique | Specific techniques can optimize growth rates for different applications. |
Learn how CVD can enhance your industrial processes—contact our experts today for tailored solutions!