Sputtering and evaporation are both physical vapor deposition (PVD) techniques used to create thin films, but they differ fundamentally in their mechanisms, operational parameters, and resulting film properties. Sputtering involves the collision of energetic ions with a target material to eject atoms, which then deposit onto a substrate. In contrast, evaporation relies on heating a source material past its vaporization temperature, creating a vapor that condenses on the substrate. These differences lead to variations in deposition rates, film adhesion, homogeneity, and scalability, making each method suitable for specific applications.
Key Points Explained:
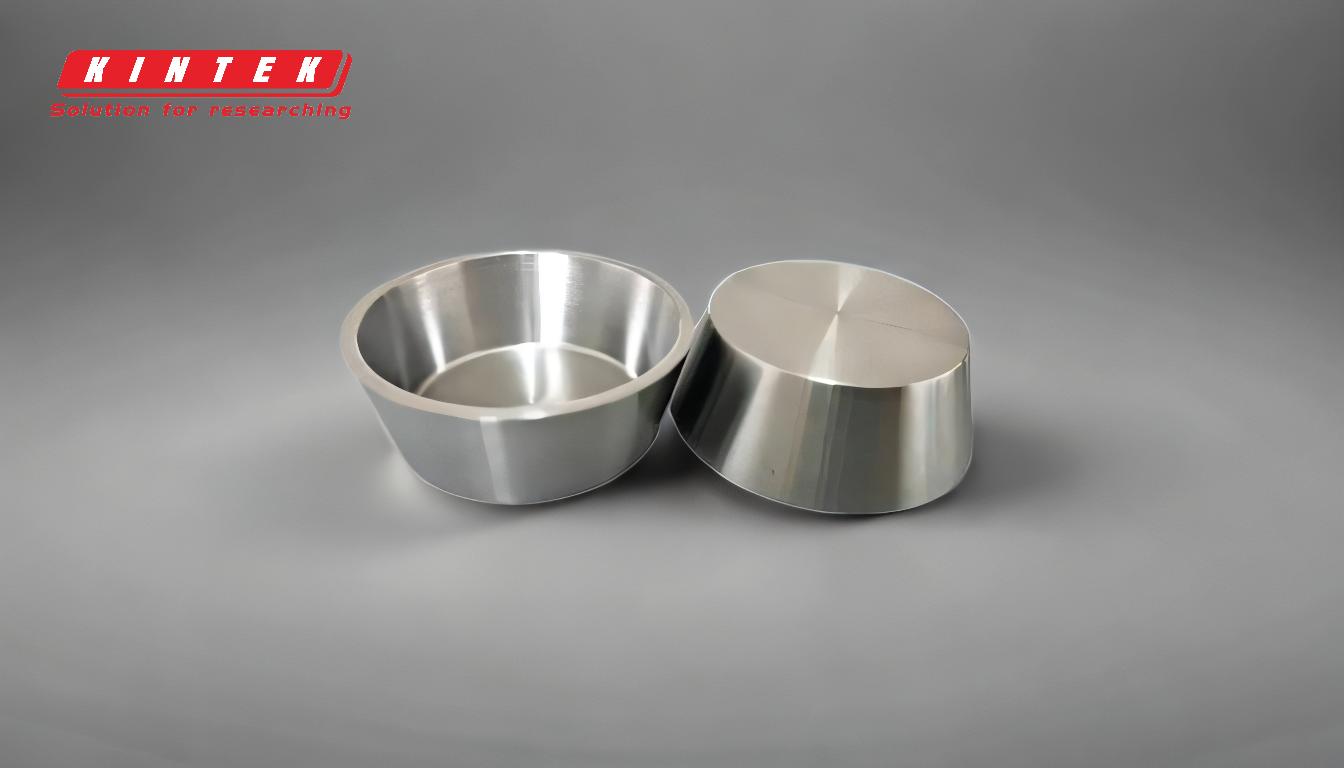
-
Mechanism of Deposition:
- Sputtering: Involves bombarding a target material with energetic ions (usually argon) in a plasma environment. The collision ejects atoms from the target, which then deposit onto the substrate. This process occurs within a closed magnetic field.
- Evaporation: Relies on heating the source material (using methods like electron beam or resistive heating) until it vaporizes. The vapor then condenses onto the substrate, typically within a high-vacuum chamber.
-
Energy of Deposited Species:
- Sputtering: Produces high-energy atoms due to the momentum transfer during ion bombardment. This results in better film adhesion and denser coatings.
- Evaporation: Deposits low-energy atoms, which can lead to less dense films and weaker adhesion unless additional measures (like ion-assisted deposition) are employed.
-
Deposition Rate:
- Sputtering: Generally has a lower deposition rate compared to evaporation, except for pure metals. However, it offers better control over film thickness and uniformity.
- Evaporation: Typically has a higher deposition rate, making it faster for certain applications, but it may lack the precision of sputtering.
-
Vacuum Requirements:
- Sputtering: Operates at lower vacuum levels (5-15 mTorr), where gas-phase collisions thermalize the sputtered particles before they reach the substrate.
- Evaporation: Requires a high vacuum to minimize contamination and ensure a line-of-sight trajectory for the vaporized material.
-
Film Properties:
- Adhesion: Sputtering generally provides better adhesion due to the higher energy of the deposited atoms.
- Homogeneity: Sputtering tends to produce more homogeneous films, while evaporation can result in less uniform coatings.
- Grain Size: Sputtered films typically have smaller grain sizes, leading to smoother surfaces, whereas evaporated films often have larger grains.
-
Scalability and Automation:
- Sputtering: Highly scalable and easily automated, making it suitable for large-scale industrial applications.
- Evaporation: Less scalable and more challenging to automate, though it remains effective for specific, high-precision tasks.
-
Applications:
- Sputtering: Commonly used in industries requiring high-quality, durable coatings, such as semiconductor manufacturing, optical coatings, and decorative finishes.
- Evaporation: Preferred for applications needing high deposition rates and simpler setups, such as thin-film solar cells, metallization, and certain types of research.
-
Absorbed Gas and Contamination:
- Sputtering: More prone to gas absorption due to the lower vacuum levels, which can affect film purity.
- Evaporation: Less prone to gas absorption, resulting in purer films, but contamination risks still exist if the vacuum is compromised.
In summary, the choice between sputtering and evaporation depends on the specific requirements of the application, including desired film properties, deposition rate, scalability, and operational environment. Sputtering excels in producing high-quality, uniform, and adherent films, while evaporation offers faster deposition rates and simpler setups for less demanding applications.
Summary Table:
Aspect | Sputtering | Evaporation |
---|---|---|
Mechanism | Bombards target with ions to eject atoms. | Heats source material to vaporize and condense on substrate. |
Energy of Atoms | High-energy atoms, better adhesion, denser films. | Low-energy atoms, less dense films, weaker adhesion. |
Deposition Rate | Lower rate, better control over thickness and uniformity. | Higher rate, faster for certain applications. |
Vacuum Requirements | Operates at lower vacuum levels (5-15 mTorr). | Requires high vacuum to minimize contamination. |
Film Properties | Better adhesion, homogeneous films, smaller grain sizes. | Less uniform coatings, larger grain sizes. |
Scalability | Highly scalable and easily automated. | Less scalable, challenging to automate. |
Applications | Semiconductor manufacturing, optical coatings, decorative finishes. | Thin-film solar cells, metallization, research. |
Absorbed Gas | More prone to gas absorption, affecting film purity. | Less prone to gas absorption, purer films. |
Need help choosing the right PVD technique for your application? Contact our experts today!