Sputtering is a physical vapor deposition (PVD) technique used to deposit thin films of material onto a substrate. The process involves bombarding a target material with high-energy ions, typically from an inert gas like argon, in a vacuum environment. These ions transfer their kinetic energy to the target atoms, causing them to be ejected from the surface. The ejected atoms then travel through the vacuum chamber and deposit onto a substrate, forming a thin film. This mechanism relies on the creation of a plasma, ionization of the sputtering gas, and the precise control of energy transfer to achieve accurate and uniform film deposition.
Key Points Explained:
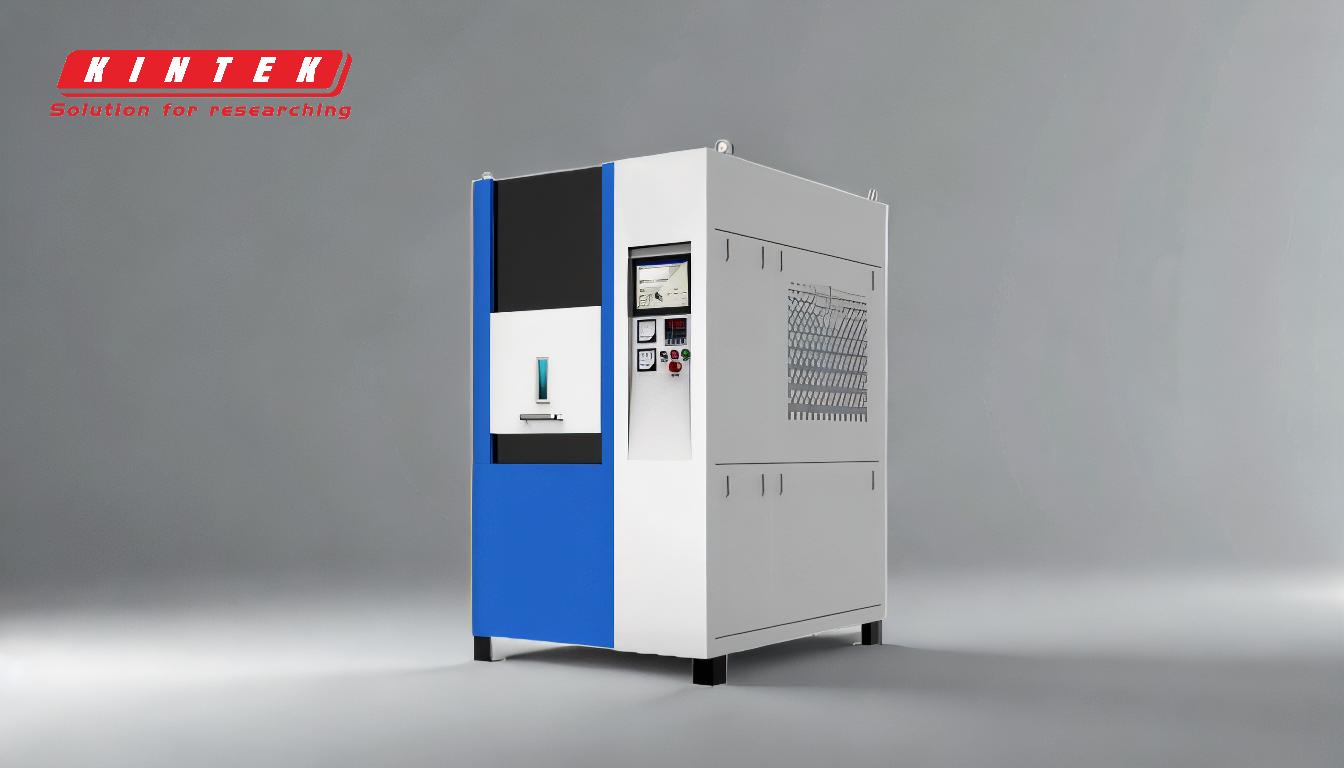
-
Vacuum Environment:
- Sputtering occurs in a vacuum chamber to minimize contamination and ensure a controlled environment.
- The vacuum allows for the efficient movement of sputtered particles from the target to the substrate without interference from air molecules.
-
Target and Substrate Setup:
- The target material, which is the source of the sputtered atoms, is placed in the chamber as the cathode.
- The substrate, where the thin film will be deposited, is positioned as the anode.
- A voltage is applied between the target and substrate to create an electric field that drives the sputtering process.
-
Plasma Creation:
- A plasma is generated by ionizing a sputtering gas, typically an inert gas like argon or xenon.
- Free electrons from the target collide with the gas atoms, ionizing them and creating positively charged ions.
-
Ion Bombardment:
- The positively charged ions are accelerated toward the negatively charged target due to the applied voltage.
- When these ions strike the target, they transfer their kinetic energy to the target atoms.
-
Ejection of Target Atoms:
- The energy transfer from the ions to the target atoms causes the latter to overcome the binding forces holding them in the target material.
- As a result, atoms or molecules near the surface are ejected from the target.
-
Deposition on Substrate:
- The ejected atoms travel through the vacuum chamber and deposit onto the substrate.
- These atoms condense on the substrate surface, forming a thin film with precise thickness and uniformity.
-
Energy Transfer and Film Quality:
- The energy of the bombarding ions determines the quality and properties of the deposited film.
- Higher energy ions can lead to denser and more adherent films, while lower energy ions may result in porous or less adherent films.
-
Neutral Particle Ejection:
- While some ejected particles are ions, many are neutral atoms or molecules.
- These neutral particles are crucial for achieving uniform deposition and minimizing charge buildup on the substrate.
-
Applications of Sputtering:
- Sputtering is widely used in industries such as semiconductors, optics, and coatings due to its ability to produce highly accurate and uniform thin films.
- It is particularly valuable for depositing materials that are difficult to evaporate or require precise control over film properties.
-
Advantages of Sputtering:
- High precision and control over film thickness and composition.
- Ability to deposit a wide range of materials, including metals, alloys, and ceramics.
- Excellent adhesion and uniformity of the deposited films.
By understanding these key points, one can appreciate the intricate mechanism of sputtering and its significance in modern manufacturing and material science. The process's ability to produce high-quality thin films with precise control makes it indispensable in various high-tech applications.
Summary Table:
Key Aspect | Description |
---|---|
Vacuum Environment | Ensures contamination-free and controlled sputtering conditions. |
Target and Substrate Setup | Target (cathode) and substrate (anode) are positioned with an applied voltage. |
Plasma Creation | Inert gas (e.g., argon) is ionized to create positively charged ions. |
Ion Bombardment | Ions strike the target, transferring energy to eject target atoms. |
Deposition on Substrate | Ejected atoms deposit on the substrate, forming a thin, uniform film. |
Applications | Used in semiconductors, optics, and coatings for precise thin film deposition. |
Advantages | High precision, excellent adhesion, and ability to deposit diverse materials. |
Discover how sputtering can enhance your thin film processes—contact us today!