Scanning Electron Microscopy (SEM) is a powerful tool for imaging and analyzing the surface of materials at high resolution. However, non-conductive samples can pose challenges in SEM imaging due to charging effects, which can distort the image and reduce its quality. To mitigate this, a thin metal coating is often applied to the sample surface. This coating enhances conductivity, reduces charging, and improves the signal-to-noise ratio, resulting in clearer and more detailed images. Common metals used for coating include gold, gold-palladium, platinum, and carbon, each chosen based on the specific requirements of the sample and the imaging conditions.
Key Points Explained:
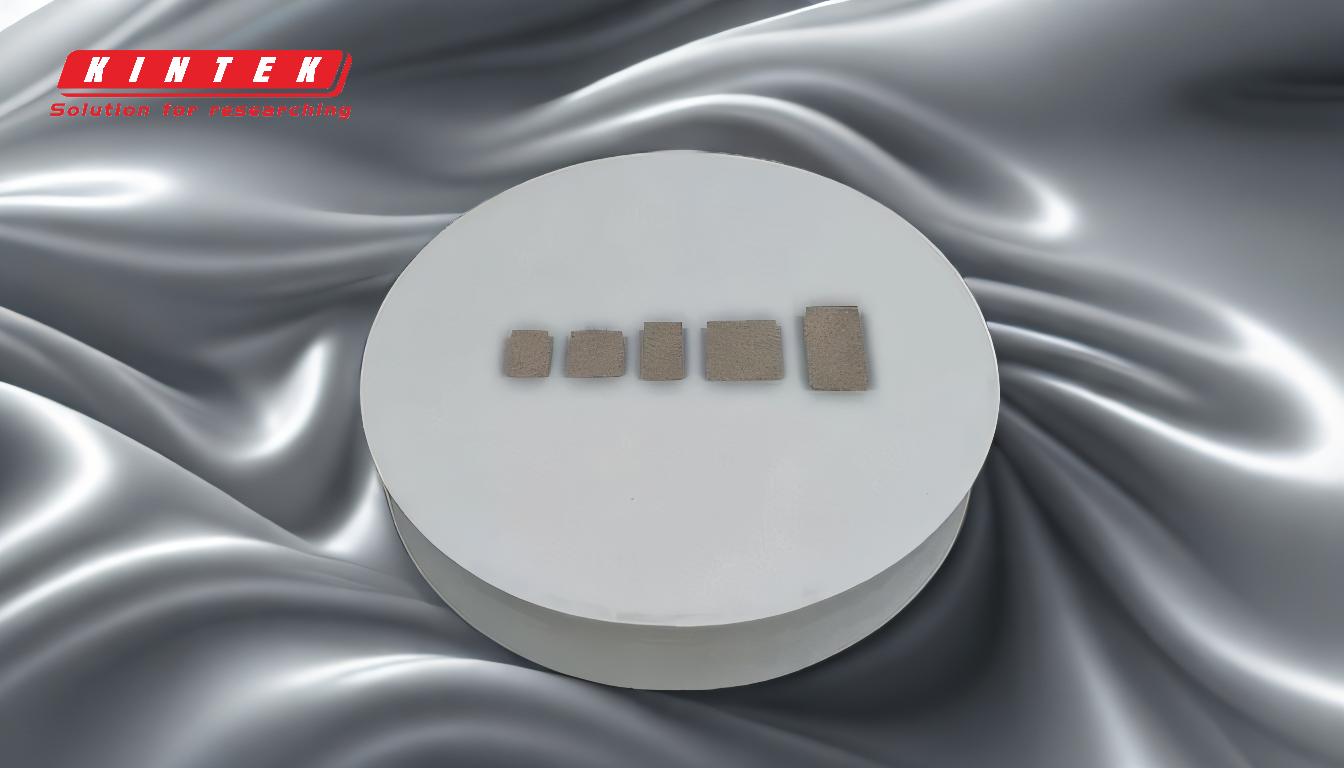
-
Purpose of Metal Coating in SEM:
- Conductivity Enhancement: Non-conductive samples can accumulate charge under the electron beam, leading to image distortion. A metal coating provides a conductive layer that dissipates this charge.
- Improved Signal-to-Noise Ratio: Metal coatings enhance secondary electron emission, which is crucial for high-resolution imaging.
- Reduction of Beam Damage: Thin metal coatings can protect sensitive samples from beam damage by acting as a barrier.
-
Common Metals Used for Coating:
- Gold (Au): Gold is the most commonly used metal for SEM coating due to its high conductivity and excellent secondary electron emission properties. It is ideal for high-resolution imaging but can form large grains, which may obscure fine details.
- Gold-Palladium (Au-Pd): This alloy combines the benefits of gold and palladium, offering finer grain size and better adhesion to the sample surface. It is often used for high-magnification imaging.
- Platinum (Pt): Platinum coatings are used when extremely fine grain size is required, making them suitable for ultra-high-resolution imaging.
- Carbon (C): Carbon coatings are used for samples that require minimal interference with the sample's elemental composition, such as in energy-dispersive X-ray spectroscopy (EDS) analysis.
-
Coating Techniques:
- Sputter Coating: This is the most common method, where a thin layer of metal is deposited onto the sample surface using a sputter coater. It provides a uniform coating and is suitable for most SEM applications.
- Evaporation Coating: In this method, metal is evaporated in a vacuum and deposited onto the sample. It is less common but can be used for specific applications requiring very thin coatings.
- Carbon Coating: Carbon coatings are typically applied using a carbon evaporator, which deposits a thin layer of carbon onto the sample surface.
-
Factors Influencing Coating Choice:
- Sample Type: The nature of the sample (e.g., organic, inorganic, biological) influences the choice of coating material. For example, biological samples often require gold or gold-palladium coatings.
- Imaging Requirements: The desired resolution and type of analysis (e.g., secondary electron imaging, backscattered electron imaging) dictate the coating thickness and material.
- Compatibility with Analysis: If the sample will undergo additional analysis, such as EDS, the coating material must not interfere with the results. Carbon is often preferred in such cases.
-
Advantages and Limitations:
-
Advantages:
- Enhanced image quality with reduced charging effects.
- Protection of sensitive samples from beam damage.
- Improved secondary electron emission for better contrast.
-
Limitations:
- The coating process can introduce artifacts or obscure fine surface details.
- Some coatings may interfere with subsequent analysis techniques.
- The choice of coating material and thickness requires careful consideration to avoid compromising the sample's integrity.
-
Advantages:
In conclusion, metal coating is a critical step in preparing non-conductive samples for SEM analysis. The choice of coating material and technique depends on the sample type, imaging requirements, and the need for compatibility with additional analytical methods. By selecting the appropriate coating, researchers can achieve high-quality images and accurate analysis, making SEM a versatile tool for material characterization.
Summary Table:
Aspect | Details |
---|---|
Purpose | Enhances conductivity, reduces charging, and improves signal-to-noise ratio. |
Common Metals | Gold, Gold-Palladium, Platinum, Carbon. |
Coating Techniques | Sputter Coating, Evaporation Coating, Carbon Coating. |
Key Factors | Sample type, imaging requirements, compatibility with analysis. |
Advantages | Better image quality, reduced beam damage, improved contrast. |
Limitations | Potential artifacts, interference with analysis, careful material selection. |
Need help selecting the right metal coating for your SEM analysis? Contact our experts today!