The most important safety issue in welding, cutting, and brazing is the prevention of fires and explosions. These processes involve high temperatures, open flames, and sparks, which can easily ignite flammable materials in the surrounding environment. Proper handling of equipment, maintaining a clean workspace, and ensuring adequate ventilation are critical to mitigating these risks. Additionally, personal protective equipment (PPE) such as flame-resistant clothing, gloves, and face shields must be used to protect workers from burns and other injuries. Regular training and adherence to safety protocols are essential to minimize hazards and ensure a safe working environment.
Key Points Explained:
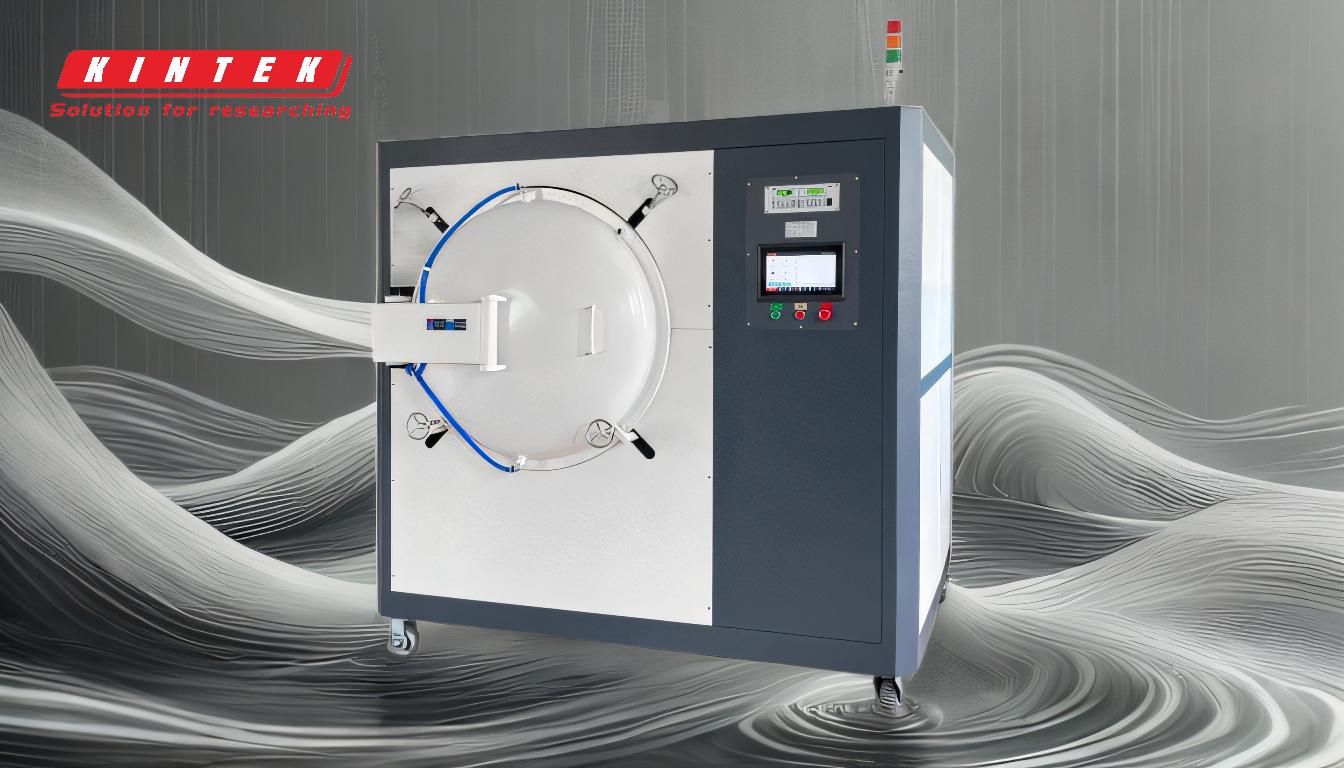
-
Fire and Explosion Hazards:
- Welding, cutting, and brazing generate intense heat, sparks, and open flames, which can ignite flammable materials like gases, liquids, or dust in the vicinity.
- To prevent fires, ensure that the work area is free of combustible materials, and use fire-resistant barriers or shields when necessary.
- Always have fire extinguishers or other firefighting equipment readily available.
-
Proper Ventilation:
- These processes often produce hazardous fumes and gases, such as ozone, nitrogen oxides, and metal vapors, which can be harmful if inhaled.
- Adequate ventilation, such as local exhaust ventilation (LEV) systems, is crucial to remove these contaminants from the workspace and protect workers' respiratory health.
-
Personal Protective Equipment (PPE):
- Workers must wear appropriate PPE, including flame-resistant clothing, gloves, safety glasses, and face shields, to protect against burns, UV radiation, and flying debris.
- Respiratory protection may also be necessary in poorly ventilated areas or when working with toxic materials.
-
Equipment Maintenance and Safety:
- Regularly inspect welding and cutting equipment to ensure it is in good working condition. Faulty equipment can lead to accidents, such as gas leaks or electrical shocks.
- Follow manufacturer guidelines for the safe operation of tools and machinery.
-
Training and Safety Protocols:
- Workers should receive thorough training on the hazards associated with welding, cutting, and brazing, as well as the proper use of equipment and PPE.
- Establish and enforce safety protocols, such as hot work permits, to ensure that all necessary precautions are taken before starting work.
-
Emergency Preparedness:
- Have a clear emergency response plan in place, including evacuation routes and first aid procedures.
- Conduct regular drills to ensure that workers know how to respond in case of an accident or fire.
By addressing these key points, workplaces can significantly reduce the risks associated with welding, cutting, and brazing, ensuring the safety and well-being of all personnel involved.
Summary Table:
Key Safety Issue | Prevention Measures |
---|---|
Fire and Explosion Hazards | Keep work area free of combustibles; use fire-resistant barriers; have fire extinguishers ready. |
Proper Ventilation | Use local exhaust ventilation (LEV) to remove hazardous fumes and gases. |
Personal Protective Equipment (PPE) | Wear flame-resistant clothing, gloves, safety glasses, and face shields. Use respiratory protection if needed. |
Equipment Maintenance | Regularly inspect tools; follow manufacturer guidelines for safe operation. |
Training and Safety Protocols | Provide thorough training; enforce hot work permits and safety protocols. |
Emergency Preparedness | Establish emergency response plans; conduct regular drills. |
Ensure your workplace safety—contact our experts today for tailored solutions and training!