Physical sputtering is a process used in thin film deposition, where atoms are ejected from a solid target material due to bombardment by energetic ions. These ejected atoms then deposit onto a substrate, forming a thin film. The process occurs in a vacuum environment and involves ionized gas (typically inert gases like argon) accelerated by an electric field to strike the target. The target material is eroded, and the ejected particles travel to the substrate, where they condense into a film. Sputtering is highly precise and is used in applications requiring controlled film properties such as reflectivity, electrical resistivity, and grain structure.
Key Points Explained:
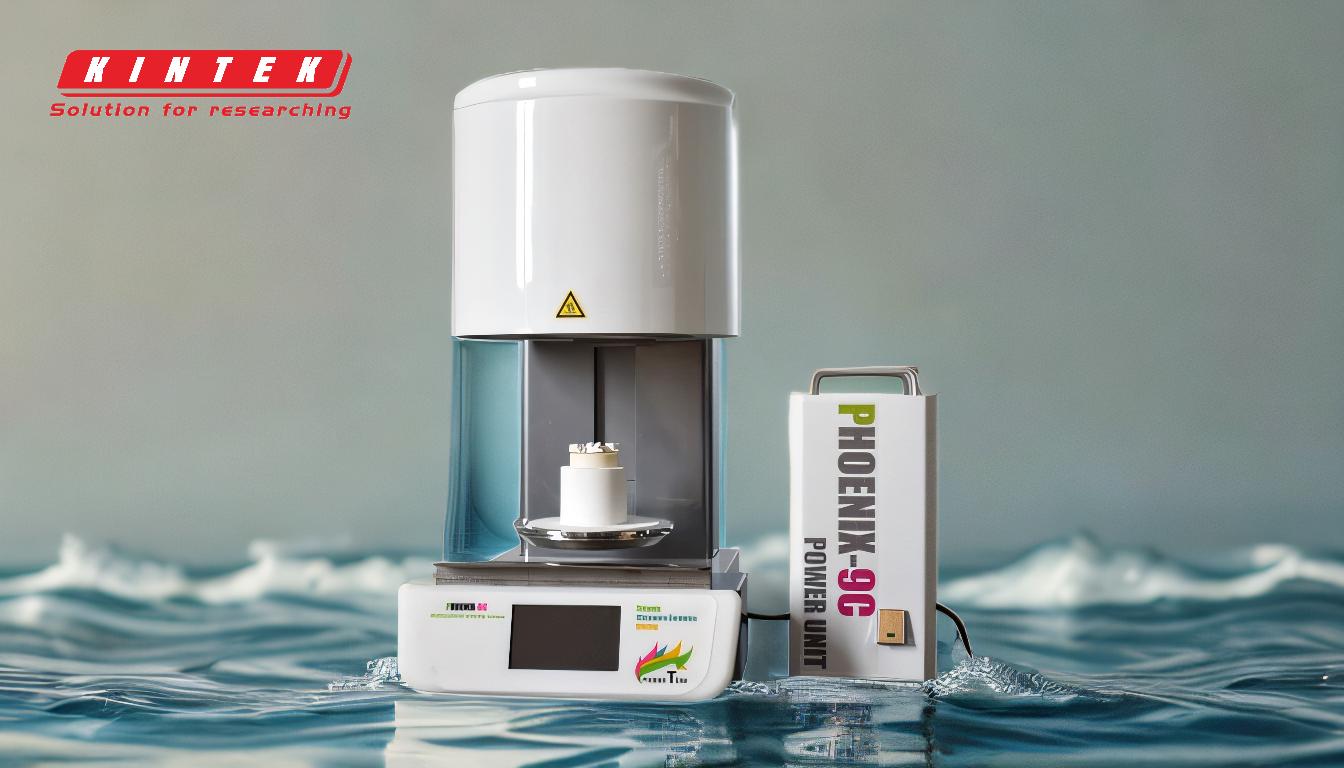
-
Definition of Physical Sputtering:
- Physical sputtering is a thin film deposition technique where atoms are ejected from a target material due to bombardment by high-energy ions.
- The ejected atoms travel to a substrate and condense into a thin film.
-
Process Overview:
- The target material and substrate are placed in a vacuum chamber.
- A voltage is applied, making the target the cathode and the substrate the anode.
- A plasma is created by ionizing a sputtering gas (usually argon or xenon).
- The ionized gas bombards the target, causing atoms to be ejected.
- These atoms travel to the substrate and form a thin film.
-
Key Components:
- Target Material: The source material from which atoms are ejected.
- Substrate: The surface onto which the ejected atoms are deposited.
- Sputtering Gas: Typically an inert gas like argon, ionized to create the plasma.
- Vacuum Chamber: The environment where the process occurs to minimize contamination and control pressure.
-
Mechanism of Sputtering:
- Ions from the sputtering gas are accelerated by an electric field.
- These ions collide with the target material, transferring energy to the target atoms.
- If the energy transferred is sufficient, target atoms are ejected from the surface.
-
Types of Sputtering:
- Cathodic Sputtering: Involves a cathode (target) and anode (substrate) setup.
- Diode Sputtering: Uses a simple two-electrode system.
- RF or DC Sputtering: Utilizes radio frequency or direct current to ionize the gas.
- Ion-Beam Sputtering: A focused ion beam is used to sputter the target.
- Reactive Sputtering: Involves a reactive gas to form compound films.
-
Applications of Sputtering:
- Used in the production of precision thin films for semiconductors, optical coatings, and solar cells.
- Enables control over film properties like reflectivity, electrical resistivity, and grain structure.
-
Advantages of Sputtering:
- High precision and control over film thickness and composition.
- Ability to deposit a wide range of materials, including metals, alloys, and compounds.
- Suitable for large-scale production and complex geometries.
-
Challenges and Considerations:
- Requires a high vacuum environment, which can be costly to maintain.
- The process can be slow compared to other deposition methods.
- Target material erosion can lead to contamination if not managed properly.
By understanding these key points, one can appreciate the complexity and precision of the physical sputtering method, making it a valuable technique in modern manufacturing and material science.
Summary Table:
Aspect | Details |
---|---|
Definition | Ejection of atoms from a target material by ion bombardment. |
Key Components | Target material, substrate, sputtering gas, vacuum chamber. |
Process | Ionized gas bombards target, ejecting atoms that deposit on the substrate. |
Types | Cathodic, Diode, RF/DC, Ion-Beam, Reactive sputtering. |
Applications | Semiconductors, optical coatings, solar cells. |
Advantages | High precision, wide material range, large-scale production suitability. |
Challenges | High vacuum cost, slower process, potential contamination risks. |
Discover how physical sputtering can enhance your manufacturing process—contact our experts today!