Sputtering deposition is a widely used physical vapor deposition (PVD) technique for creating thin films on substrates. It involves bombarding a target material with high-energy ions, typically from an inert gas like argon, in a vacuum environment. This bombardment ejects atoms from the target, which then travel through the vacuum and deposit onto a substrate, forming a thin film. The process relies on the transfer of energy from the ions to the target material, causing atoms to be ejected and deposited uniformly on the substrate. Sputtering deposition is highly versatile, enabling the deposition of various materials, including metals, semiconductors, and insulators, with precise control over film thickness and composition.
Key Points Explained:
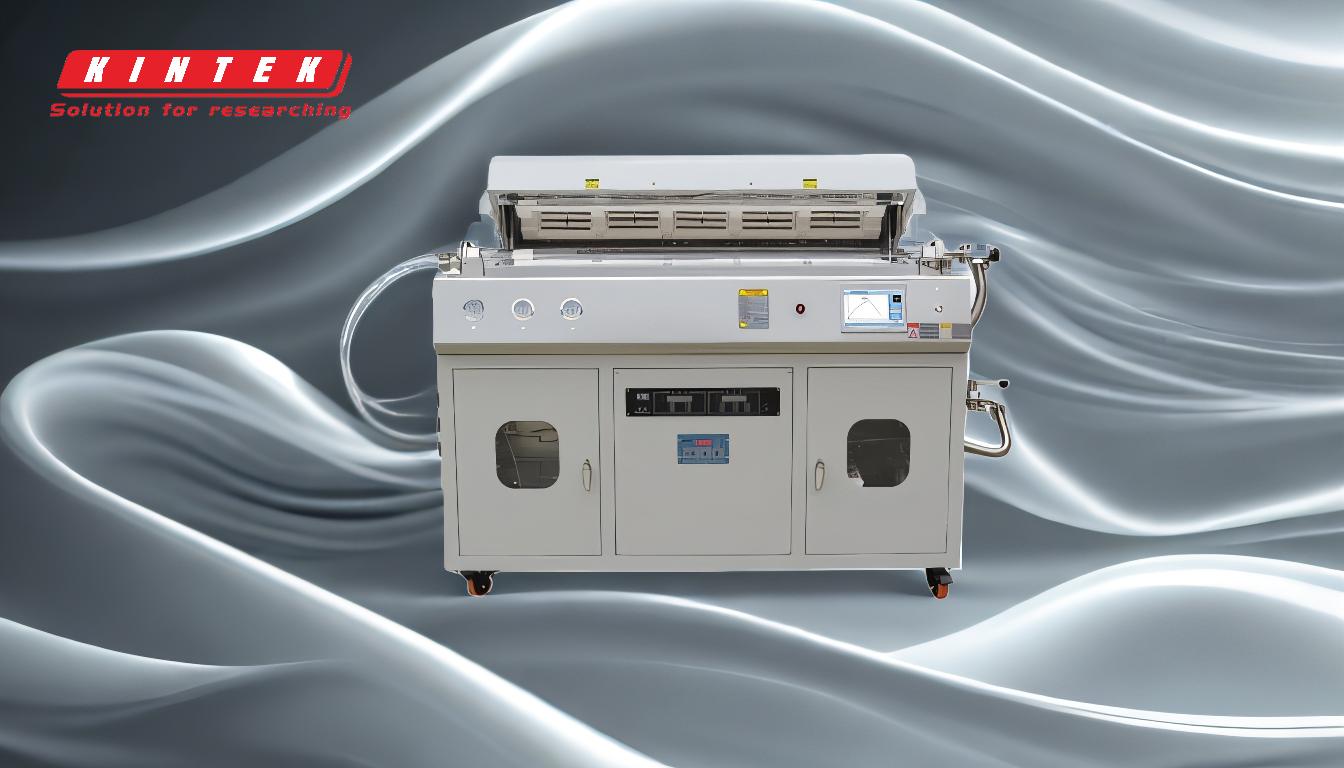
-
Basic Principle of Sputtering Deposition:
- Sputtering deposition is a PVD method where a target material is bombarded by high-energy ions, causing atoms to be ejected and deposited onto a substrate.
- The process occurs in a vacuum chamber to ensure a clean and controlled environment, minimizing contamination and interference from atmospheric gases.
-
Role of Plasma and Inert Gas:
- A plasma is created by ionizing an inert gas, typically argon, within the vacuum chamber.
- The plasma generates high-energy ions that are accelerated toward the target material, initiating the sputtering process.
-
Energy Transfer and Ejection of Atoms:
- When the high-energy ions collide with the target material, they transfer their kinetic energy to the target atoms.
- This energy transfer causes atoms from the target to be ejected into the gas phase, a process known as sputtering.
-
Deposition of Thin Films:
- The ejected atoms travel through the vacuum and deposit onto the substrate, forming a thin film.
- The substrate is often placed opposite the target, and a shutter mechanism may be used to control the exposure time and deposition rate.
-
Cathode and Anode Configuration:
- The target material is typically connected to a negatively charged cathode, while the substrate is connected to a positively charged anode.
- This configuration facilitates the acceleration of ions toward the target and ensures efficient deposition of the ejected atoms onto the substrate.
-
Collision Cascade and Film Adhesion:
- The impact of ions on the target creates a collision cascade, which helps eject multiple atoms from the target surface.
- The ejected atoms adhere securely to the substrate, forming a uniform and durable thin film.
-
Advantages of Sputtering Deposition:
- High precision in controlling film thickness and composition.
- Ability to deposit a wide range of materials, including metals, alloys, and compounds.
- Excellent film uniformity and adhesion, making it suitable for applications in microelectronics, optics, and coatings.
-
Applications of Sputtering Deposition:
- Widely used in the semiconductor industry for depositing thin films on silicon wafers.
- Applied in the production of optical coatings, such as anti-reflective and mirror coatings.
- Utilized in the fabrication of hard coatings for tools and wear-resistant surfaces.
By understanding these key points, one can appreciate the scientific and practical significance of sputtering deposition in modern material science and industrial applications.
Summary Table:
Key Aspect | Details |
---|---|
Basic Principle | Bombardment of target material with high-energy ions in a vacuum chamber. |
Role of Plasma | Ionized inert gas (e.g., argon) generates ions for sputtering. |
Energy Transfer | Kinetic energy from ions ejects atoms from the target. |
Deposition Process | Ejected atoms deposit onto a substrate, forming a thin film. |
Cathode & Anode Setup | Target (cathode) and substrate (anode) ensure efficient deposition. |
Collision Cascade | Ion impact creates a cascade, ejecting multiple atoms for uniform adhesion. |
Advantages | Precise control, versatile material deposition, excellent film adhesion. |
Applications | Semiconductors, optical coatings, hard coatings for tools. |
Discover how sputtering deposition can enhance your projects—contact our experts today!