The manufacturing process of alumina tubes involves several precise steps to ensure the final product meets the required specifications for industrial applications. Alumina tubes are made from aluminum oxide (Al₂O₃), a material known for its high thermal stability, electrical insulation, and mechanical strength. The process typically includes raw material preparation, shaping, sintering, and finishing. Each step is critical to achieving the desired properties, such as high purity, thermal resistance, and structural integrity. Below, the key points of the manufacturing process are explained in detail.
Key Points Explained:
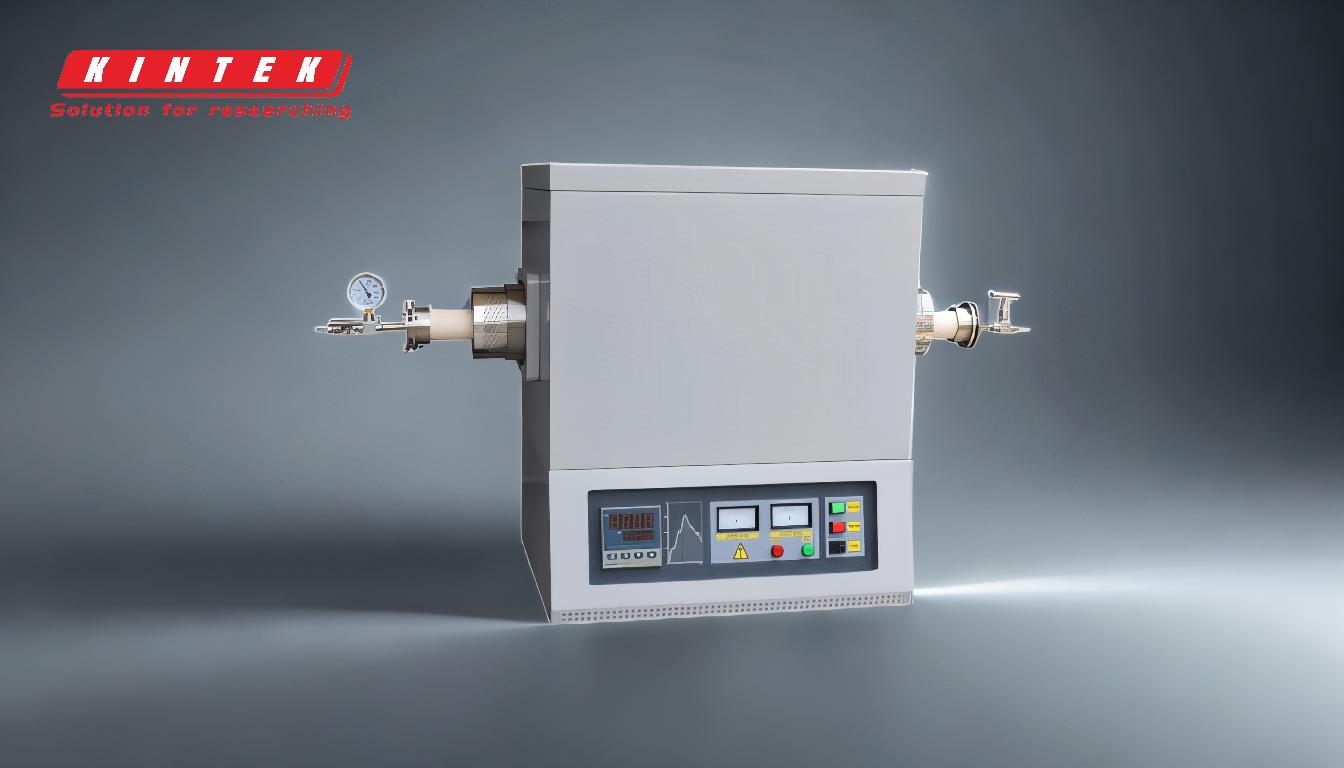
-
Raw Material Preparation
- Alumina powder, typically with a purity of 99.6%, is the primary raw material used.
- The powder is carefully selected to ensure consistency in particle size and chemical composition.
- Additives, such as binders and plasticizers, may be mixed with the alumina powder to improve its workability during shaping.
-
Shaping the Tubes
- The prepared alumina mixture is shaped into tubes using one of several methods:
- Extrusion: The mixture is forced through a die to form a continuous tube shape.
- Isostatic Pressing: The powder is compacted under high pressure in a mold to form the tube.
- Slip Casting: A slurry of alumina is poured into a porous mold, and the liquid is absorbed, leaving a solid tube shape.
- The shaping method depends on the desired dimensions, wall thickness, and application requirements.
- The prepared alumina mixture is shaped into tubes using one of several methods:
-
Drying
- After shaping, the tubes are dried to remove moisture and binders.
- Drying must be controlled to prevent cracking or warping due to uneven shrinkage.
-
Sintering
- The dried tubes are sintered at high temperatures (around 1810℃) in a kiln.
- Sintering causes the alumina particles to bond together, resulting in a dense, strong, and durable tube.
- The sintering process also determines the final properties, such as thermal stability and mechanical strength.
-
Finishing
- After sintering, the tubes may undergo additional processes, such as:
- Machining: Precision grinding or cutting to achieve exact dimensions.
- Polishing: Smoothing the surface for specific applications.
- Coating: Applying protective or functional coatings, if required.
- After sintering, the tubes may undergo additional processes, such as:
-
Quality Control
- The finished tubes are inspected for defects, dimensional accuracy, and performance characteristics.
- Tests may include measuring thermal resistance, electrical insulation, and mechanical strength.
-
Applications of Alumina Tubes
- Alumina tubes are used in high-temperature and corrosive environments, such as:
- Thermocouple protection tubes.
- Vacuum and semiconductor processing equipment.
- Industrial furnaces and heating elements.
- Their high purity and thermal stability make them ideal for demanding applications.
- Alumina tubes are used in high-temperature and corrosive environments, such as:
By following these steps, manufacturers can produce alumina tubes with the required properties for a wide range of industrial uses. The process ensures that the tubes meet the high standards needed for applications such as turbine casting supports, surgical devices, and high-power resistors.
Summary Table:
Step | Key Details |
---|---|
Raw Material Prep | Alumina powder (99.6% purity) mixed with binders and plasticizers for workability. |
Shaping | Extrusion, isostatic pressing, or slip casting to form tubes based on application requirements. |
Drying | Controlled drying to prevent cracking or warping. |
Sintering | High-temperature sintering (1810℃) to bond particles, ensuring density and strength. |
Finishing | Machining, polishing, or coating for precision and surface quality. |
Quality Control | Inspections and tests for thermal resistance, electrical insulation, and mechanical strength. |
Applications | Used in thermocouple protection, semiconductor processing, and industrial furnaces. |
Discover how alumina tubes can meet your industrial needs—contact us today for more information!