Electron-beam welding (EBW) is a highly precise and efficient welding technique that utilizes a focused beam of high-velocity electrons to join materials. The process involves generating an electron beam in a vacuum environment, accelerating it to high speeds, and directing it onto the workpiece. The kinetic energy of the electrons converts into heat upon impact, melting the materials and allowing them to fuse together. EBW is particularly valued for its ability to produce deep, narrow welds with minimal heat-affected zones, making it ideal for applications in aerospace, automotive, and medical industries where precision and material integrity are critical.
Key Points Explained:
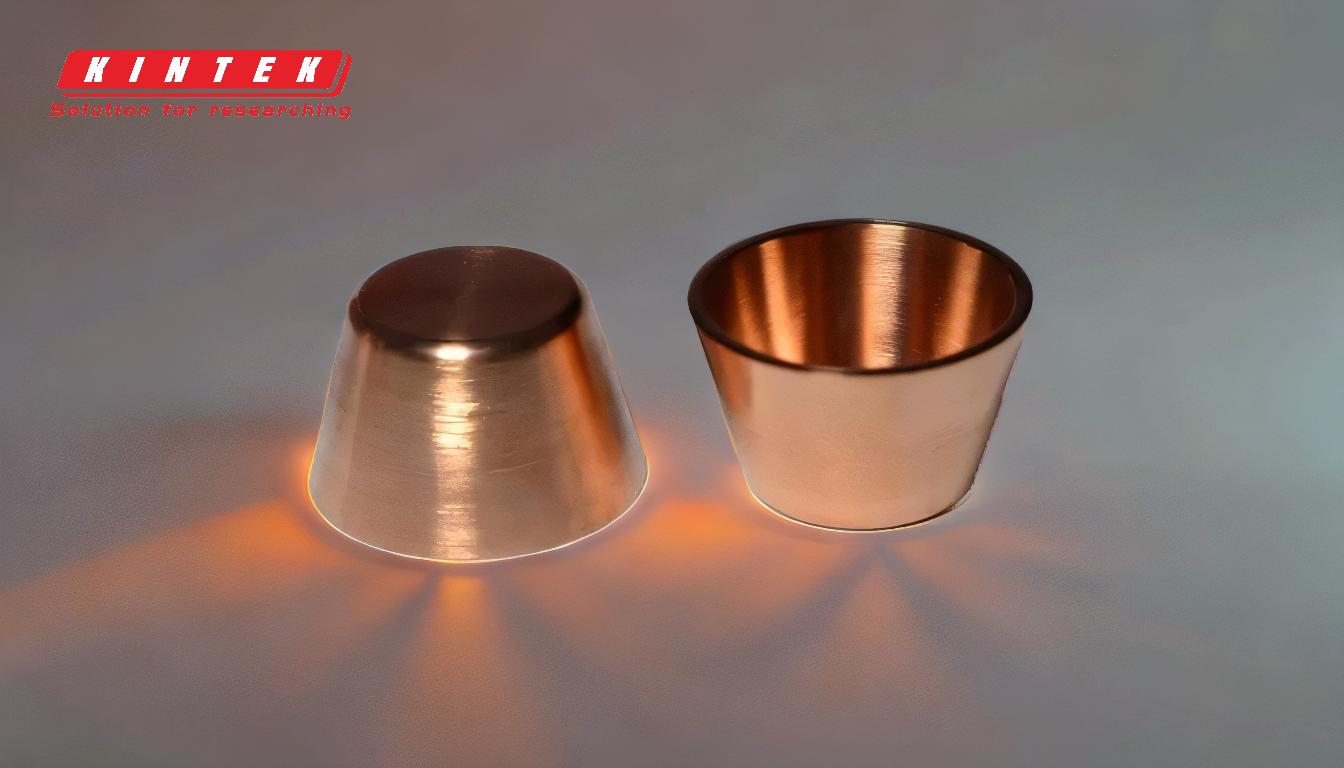
-
Generation of the Electron Beam:
- The process begins in an electron gun, where a heated filament (cathode) emits electrons.
- These electrons are accelerated through a high-voltage field (typically 30-150 kV) toward an anode, forming a high-velocity beam.
- The beam is then focused and directed using electromagnetic lenses and deflection coils to ensure precision.
-
Vacuum Environment:
- EBW is performed in a vacuum chamber to prevent electron scattering and oxidation of the workpiece.
- The vacuum environment ensures a clean weld and protects sensitive materials from contamination.
-
Energy Conversion and Heat Generation:
- When the high-velocity electron beam strikes the workpiece, the kinetic energy of the electrons is converted into heat.
- This localized heating causes the material to melt and fuse, creating a weld.
-
Weld Characteristics:
- EBW produces deep, narrow welds with a high depth-to-width ratio, often exceeding 10:1.
- The process minimizes the heat-affected zone (HAZ), reducing thermal distortion and preserving material properties.
-
Applications and Advantages:
- EBW is widely used in industries requiring high precision, such as aerospace (turbine blades, engine components), automotive (gears, transmission parts), and medical (implants, surgical tools).
- Advantages include the ability to weld dissimilar metals, high repeatability, and the capability to weld thick materials in a single pass.
-
Process Control and Automation:
- Modern EBW systems are often automated, using computer numerical control (CNC) for precise beam positioning and movement.
- Parameters such as beam current, voltage, focus, and travel speed are carefully controlled to achieve optimal weld quality.
-
Challenges and Limitations:
- The requirement for a vacuum environment limits the size of workpieces and increases setup time and cost.
- EBW equipment is expensive and requires skilled operators, making it less suitable for low-volume or cost-sensitive applications.
By understanding these key points, equipment and consumable purchasers can better evaluate whether EBW is suitable for their specific needs and make informed decisions about investing in the technology.
Summary Table:
Key Aspect | Details |
---|---|
Process | High-velocity electron beam melts materials in a vacuum environment. |
Weld Characteristics | Deep, narrow welds with minimal heat-affected zones (HAZ). |
Applications | Aerospace, automotive, medical (e.g., turbine blades, implants). |
Advantages | Welds dissimilar metals, high repeatability, single-pass thick welds. |
Challenges | Requires vacuum, expensive equipment, skilled operators. |
Automation | CNC-controlled for precise beam positioning and movement. |
Interested in how Electron-Beam Welding can elevate your manufacturing process? Contact us today to learn more!