The process of depositing polysilicon in Chemical Vapor Deposition (CVD) involves several key steps, including the introduction of precursor gases like trichlorosilane (SiHCl3) or silane (SiH4) into a reactor, where they decompose at high temperatures to form silicon on a substrate. This process typically occurs in Low-Pressure Chemical Vapor Deposition (LPCVD) systems at temperatures between 600 and 650 °C and pressures between 25 and 150 Pa, with growth rates of 10 to 20 nm per minute. Doping can be achieved by introducing gases such as phosphine, arsine, or diborane. The CVD process is highly controllable and produces high-quality films, though it can be time-consuming and costly due to the need for sophisticated equipment.
Key Points Explained:
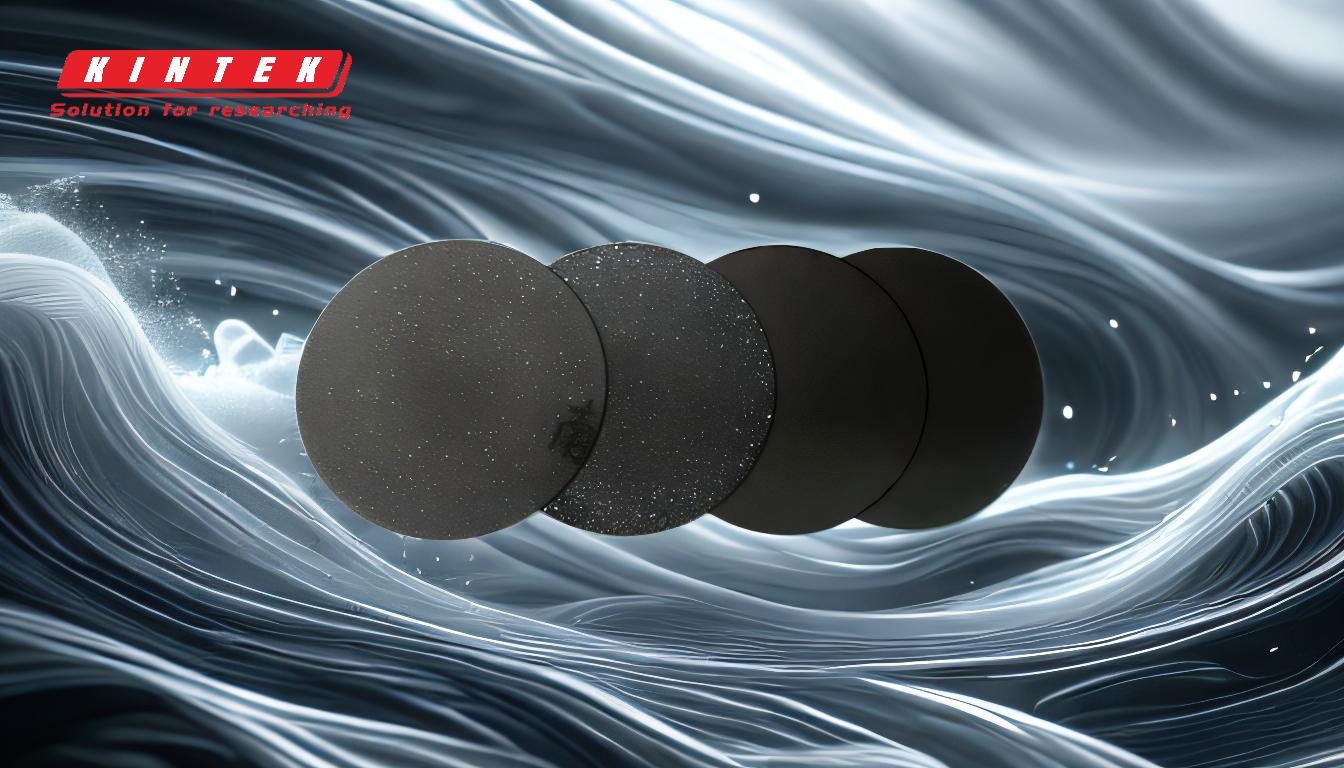
-
Precursor Gases and Reactions:
- Trichlorosilane (SiHCl3): Decomposes into silicon (Si), chlorine (Cl2), and hydrogen chloride (HCl) at high temperatures.
- Silane (SiH4): Decomposes into silicon (Si) and hydrogen (H2).
- These reactions are fundamental to the deposition of polysilicon in CVD.
-
LPCVD Systems:
- Temperature: Typically between 600 and 650 °C.
- Pressure: Between 25 and 150 Pa.
- Growth Rate: 10 to 20 nm per minute.
- These conditions are optimized to ensure efficient decomposition of the precursor gases and deposition of polysilicon.
-
Alternative Process:
- Hydrogen-Based Solution: Operates at higher temperatures (850–1050 °C).
- This method can be used for specific applications where higher temperatures are beneficial.
-
Doping:
- Dopant Gases: Phosphine (PH3), arsine (AsH3), or diborane (B2H6) are added to the CVD chamber.
- These gases introduce impurities into the silicon lattice, altering its electrical properties to create n-type or p-type semiconductors.
-
CVD Process Steps:
- Precursor Injection: Volatile precursors are introduced into the chamber.
- Reaction/Decomposition: The precursors react or decompose at high temperatures to form the desired coating material.
- Surface Bonding: The decomposed material bonds to the substrate surface.
- Film Growth: Over time, the coating builds up on the exposed surfaces.
-
Advantages of CVD:
- High-Quality Films: Produces stoichiometric, dense, and high-quality insulator films.
- Controllability: Film thickness can be managed by adjusting time and power.
- Uniformity: Ensures a uniform coating, enhancing the material's performance.
-
Challenges:
- Production Time: Lower decomposition rates can lead to longer production times.
- Cost: Requires sophisticated facilities, making it more expensive.
- Scalability: Less suitable for large-scale production due to the aforementioned factors.
-
Environmental and Economic Considerations:
- Environmental Friendliness: Some CVD processes, like the one used by Tian et al., are environmentally friendly and controllable.
- Economic Impact: The need for advanced equipment and longer production times can increase costs, making it less viable for large-scale applications.
By understanding these key points, one can appreciate the complexity and precision required in the CVD process for polysilicon deposition, as well as the trade-offs involved in achieving high-quality semiconductor materials.
Summary Table:
Aspect | Details |
---|---|
Precursor Gases | Trichlorosilane (SiHCl3), Silane (SiH4) |
LPCVD Conditions | Temperature: 600–650 °C, Pressure: 25–150 Pa, Growth Rate: 10–20 nm/min |
Doping Gases | Phosphine (PH3), Arsine (AsH3), Diborane (B2H6) |
Process Steps | Precursor Injection → Reaction/Decomposition → Surface Bonding → Film Growth |
Advantages | High-quality films, precise controllability, uniform coating |
Challenges | Time-consuming, costly, less scalable |
Interested in optimizing your CVD process for polysilicon deposition? Contact our experts today for tailored solutions!