Thermal pyrolysis is a thermochemical decomposition process where organic materials, such as biomass, plastics, or tires, are heated in the absence of oxygen to break down into smaller molecules. This process generates three primary outputs: gases (syngas), liquids (bio-oil), and solids (bio-char). The specific composition of these products depends on the feedstock and process conditions. Pyrolysis is widely used to convert waste materials into valuable resources, such as fuel, chemicals, and other industrial products. However, it is energy-intensive and requires precise control of temperature, pressure, and oxygen levels to optimize efficiency and product yield.
Key Points Explained:
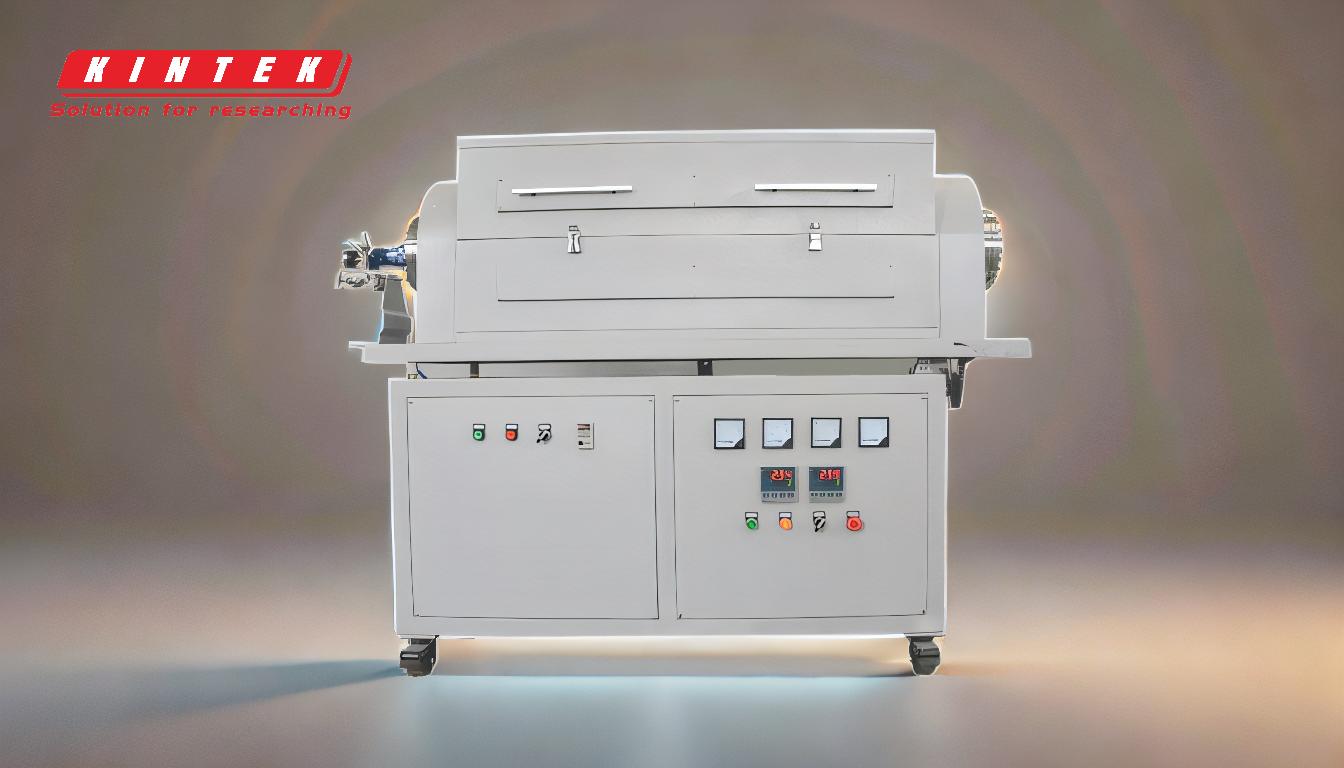
-
Definition and Mechanism of Pyrolysis:
- Pyrolysis is a thermochemical process that decomposes organic materials by heating them in the absence of oxygen.
- The absence of oxygen prevents combustion, allowing the material to break down into smaller molecules through thermal cracking.
- This process is similar to thermal cracking used in petroleum refining but operates at lower temperatures (typically 200-900°C).
-
Feedstock Preparation:
- The process begins with the collection and preparation of feedstock, such as plastic waste, biomass, or tires.
- Feedstock is pre-treated to remove impurities, dried to reduce moisture, and shredded or ground to a uniform size for efficient processing.
- Non-plastic materials (e.g., metals, glass) are separated during preprocessing to ensure the purity of the feedstock.
-
Pyrolysis Reactor Operation:
- The prepared feedstock is loaded into a pyrolysis reactor, often with a catalyst to enhance the breakdown of molecules.
- The reactor is heated to a temperature range of 200-900°C, depending on the feedstock and desired products.
- The heat causes the feedstock to melt and vaporize, breaking down complex molecules into smaller components.
-
Product Formation:
- Gases (Syngas): The vaporized material includes light gases like hydrogen, methane, and carbon monoxide, which can be used as fuel or recycled to heat the reactor.
- Liquids (Bio-oil): The vapors are condensed into a liquid known as pyrolysis oil or bio-oil, which can be further refined for use as fuel or chemical feedstock.
- Solids (Bio-char): Solid residues, such as bio-char, settle at the bottom of the reactor and can be used as a soil amendment or for carbon sequestration.
-
Post-Processing and Refinement:
- The pyrolysis oil undergoes distillation and purification to remove impurities and improve its quality.
- The purified oil is stored and dispatched for use in industrial applications or as a renewable fuel source.
- Non-condensable gases are often recycled back into the combustion chamber to provide additional heat for the process.
-
Applications and Benefits:
- Pyrolysis is used to convert waste materials into valuable products, reducing landfill waste and environmental pollution.
- The process generates renewable fuels, chemicals, and other industrial materials, contributing to a circular economy.
- It offers a sustainable solution for managing non-recyclable plastics and organic waste.
-
Challenges and Considerations:
- Pyrolysis is energy-intensive and requires significant heat input, which can increase operational costs.
- The process must be carefully controlled to avoid side reactions, such as combustion or hydrolysis, which can reduce product yield.
- The quality and composition of the final products depend on the feedstock and process conditions, requiring optimization for each application.
-
Industrial Implementation:
- Industrial pyrolysis systems often include advanced equipment, such as cyclotrons for separating gases and liquids, and combustion chambers for heat supply.
- Automation and monitoring systems are used to maintain optimal temperature, pressure, and oxygen levels throughout the process.
- Scalability and cost-effectiveness are key considerations for large-scale implementation.
By understanding these key points, stakeholders can evaluate the feasibility and benefits of thermal pyrolysis for their specific needs, whether for waste management, resource recovery, or industrial applications.
Summary Table:
Key Aspect | Details |
---|---|
Process | Thermochemical decomposition in the absence of oxygen (200-900°C). |
Feedstock | Biomass, plastics, tires—pre-treated, dried, and shredded for uniformity. |
Primary Outputs | Gases (syngas), liquids (bio-oil), and solids (bio-char). |
Applications | Renewable fuels, chemicals, soil amendment, and carbon sequestration. |
Challenges | Energy-intensive, requires precise control of temperature and pressure. |
Industrial Use | Advanced reactors, automation, and scalability for large-scale operations. |
Ready to explore thermal pyrolysis for your waste management needs? Contact us today to learn more!