X-ray Fluorescence (XRF) testing is a non-destructive analytical technique used to determine the elemental composition of materials. It is widely employed in industries such as metallurgy, mining, environmental monitoring, and quality control. The purpose of XRF testing is to provide accurate, rapid, and reliable analysis of the elemental makeup of a sample, which is crucial for ensuring material quality, compliance with standards, and process optimization. This method is particularly valuable in large enterprises where efficiency and precision are paramount.
Key Points Explained:
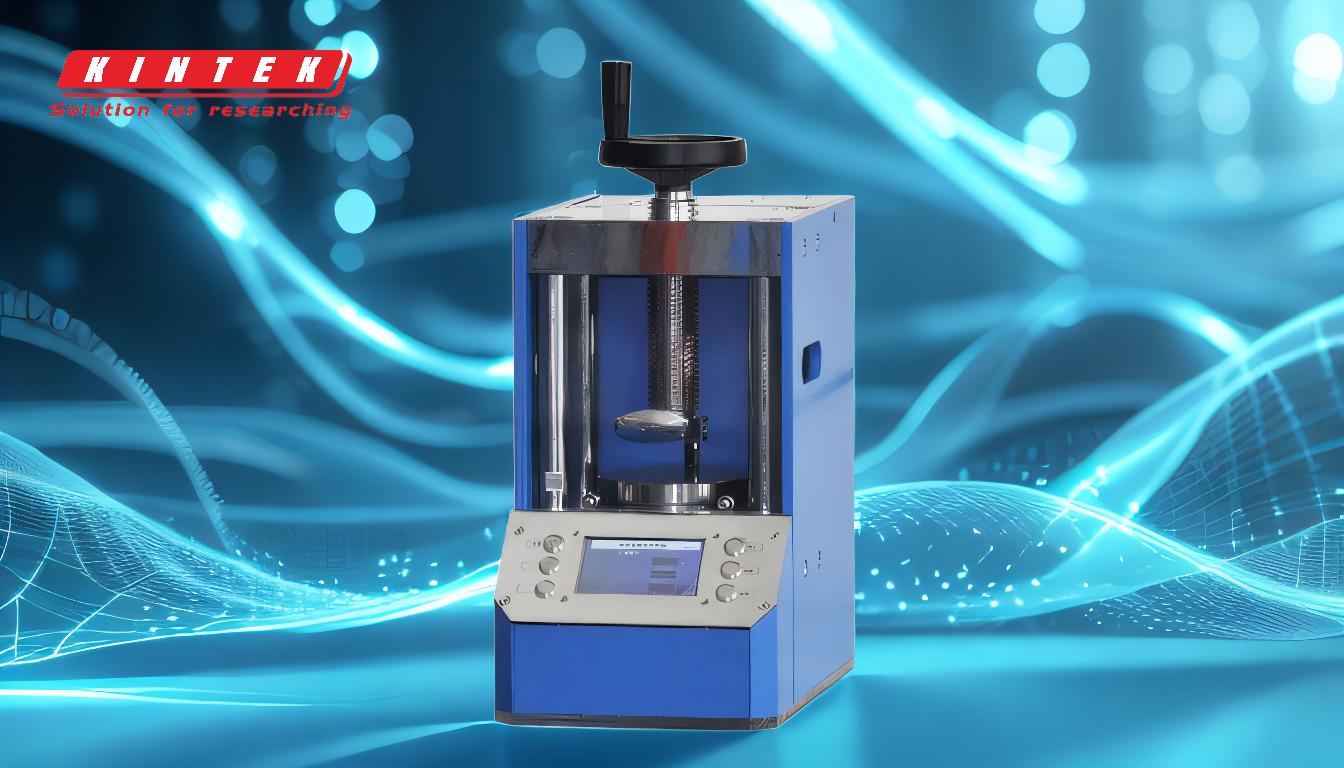
-
Non-Destructive Analysis:
- XRF testing does not damage the sample being analyzed, making it ideal for valuable or irreplaceable materials. This is especially important in industries like archaeology, art conservation, and manufacturing, where preserving the integrity of the sample is critical.
-
Elemental Composition Determination:
- XRF can identify and quantify elements present in a sample, from light elements like magnesium to heavy elements like uranium. This capability is essential for verifying the composition of metals, alloys, and other materials, ensuring they meet specific standards or specifications.
-
Versatility in Applications:
- XRF is used across a wide range of industries. For example:
- In metallurgy, it helps identify alloy grades and detect impurities.
- In mining, it aids in ore analysis and exploration.
- In environmental science, it is used to measure contaminants in soil, water, and air.
- In consumer goods, it ensures compliance with safety regulations, such as lead-free electronics.
- XRF is used across a wide range of industries. For example:
-
Speed and Efficiency:
- Handheld XRF spectrometers, in particular, provide real-time results, enabling quick decision-making in production processes. This is crucial for industries that require high throughput and minimal downtime.
-
Quality Control and Compliance:
- XRF testing ensures that materials meet regulatory and industry standards. For instance, in the automotive and aerospace industries, it verifies that alloys used in critical components meet stringent safety and performance requirements.
-
Cost-Effectiveness:
- By reducing the need for destructive testing and minimizing laboratory analysis, XRF testing lowers operational costs. It also helps prevent costly errors by ensuring material consistency early in the production process.
-
Portability and Ease of Use:
- Handheld XRF devices are portable and user-friendly, allowing for on-site analysis in remote or challenging environments. This is particularly beneficial for field applications in mining, construction, and environmental monitoring.
In summary, the purpose of XRF testing is to provide a reliable, efficient, and non-destructive method for analyzing the elemental composition of materials. Its versatility, speed, and accuracy make it an indispensable tool in various industries, ensuring quality control, compliance, and process optimization.
Summary Table:
Key Aspect | Details |
---|---|
Non-Destructive Analysis | Preserves sample integrity; ideal for valuable or irreplaceable materials. |
Elemental Composition | Identifies and quantifies elements from magnesium to uranium. |
Versatility | Used in metallurgy, mining, environmental science, and consumer goods. |
Speed and Efficiency | Handheld devices provide real-time results for quick decision-making. |
Quality Control | Ensures compliance with regulatory and industry standards. |
Cost-Effectiveness | Reduces operational costs by minimizing destructive testing. |
Portability | Handheld XRF devices enable on-site analysis in remote environments. |
Learn how XRF testing can optimize your processes—contact our experts today!