The ratio for ball milling, often referred to as the ball-to-powder ratio (BPR), is a critical parameter in determining the efficiency and outcome of the milling process. It is influenced by factors such as the type of mill, the material being milled, and the desired particle size. A common BPR for small capacity mills like SPEX is 10:1, while larger mills like attritors can operate at ratios as high as 50:1 or 100:1. The optimal ratio ensures effective grinding by balancing the energy input from the balls with the material's resistance to milling. Other factors like ball size, density, and mill rotation speed also play significant roles in achieving the desired milling results.
Key Points Explained:
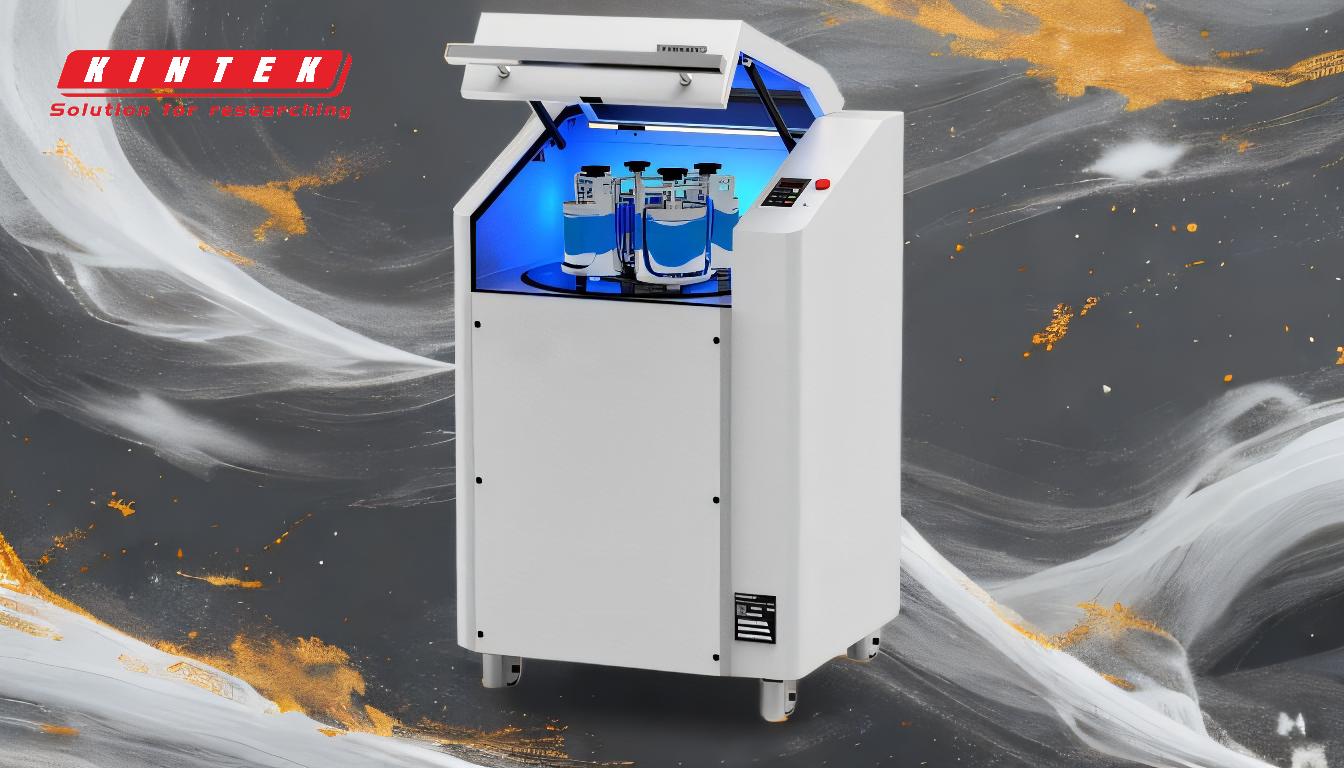
-
Definition of Ball-to-Powder Ratio (BPR):
- The BPR is the ratio of the mass of grinding balls to the mass of the material being milled. It is a key factor in determining the efficiency of the milling process.
-
Common Ratios for Different Mills:
- Small capacity mills (e.g., SPEX mills) typically use a BPR of 10:1.
- Large capacity mills (e.g., attritors) can operate at much higher BPRs, such as 50:1 or 100:1.
-
Influence of Mill Type and Capacity:
- The type of mill and its capacity significantly influence the optimal BPR. Larger mills can handle higher ratios due to their greater energy input and larger chamber sizes.
-
Material Properties:
- The hardness and nature of the material being milled affect the BPR. Harder materials may require higher ratios to achieve the desired particle size.
-
Ball Size and Density:
- Smaller balls are generally used for finer grinding, while larger balls are used for coarser grinding. The density of the balls also affects the energy transfer during milling.
-
Mill Rotation Speed:
- The rotation speed of the mill cylinder influences the BPR. Higher speeds can increase the energy input, potentially allowing for lower ratios.
-
Residence Time and Feed Rate:
- The time the material spends in the mill (residence time) and the rate at which it is fed into the mill also impact the BPR. Longer residence times and controlled feed rates can optimize the milling process.
-
Optimal Drum Dimensions:
- The ratio of drum diameter to length (L:D ratio) is crucial for productivity. An optimal L:D ratio of 1.56–1.64 is recommended for efficient milling.
-
Practical Considerations:
- Practical considerations such as the timely removal of ground product and the shape of the armor surface also play roles in determining the effective BPR.
-
General Guidelines:
- While specific ratios can vary based on the factors mentioned, general guidelines like a 7:1 ratio for mechanical milling or a 10:1 ratio for small mills provide a starting point for optimization.
Understanding and optimizing the ball-to-powder ratio is essential for achieving efficient and effective milling results. By considering the type of mill, material properties, and operational parameters, one can determine the most suitable BPR for a given application.
Summary Table:
Factor | Details |
---|---|
BPR Definition | Ratio of grinding balls mass to material mass. |
Common Ratios | 10:1 for small mills (e.g., SPEX), 50:1 or 100:1 for large mills (attritors). |
Material Properties | Harder materials may require higher BPR for effective grinding. |
Ball Size & Density | Smaller balls for finer grinding; larger balls for coarser grinding. |
Mill Rotation Speed | Higher speeds increase energy input, potentially lowering BPR. |
Optimal L:D Ratio | 1.56–1.64 for efficient milling. |
General Guidelines | 7:1 for mechanical milling; 10:1 for small mills. |
Need help optimizing your milling process? Contact our experts today for tailored solutions!