Reactive sputtering is a specialized thin film deposition technique used in Physical Vapor Deposition (PVD) processes. It involves the introduction of a reactive gas, such as oxygen or nitrogen, into a vacuum chamber containing a target material and an inert gas like argon. When the target material is sputtered, the ejected atoms react with the reactive gas to form compounds, which are then deposited as thin films on a substrate. This method allows for precise control over film composition and stoichiometry, enabling the production of oxide, nitride, or other compound films with tailored functional properties. The process is widely used in industries such as semiconductors, optics, and coatings due to its ability to create high-quality, functional thin films.
Key Points Explained:
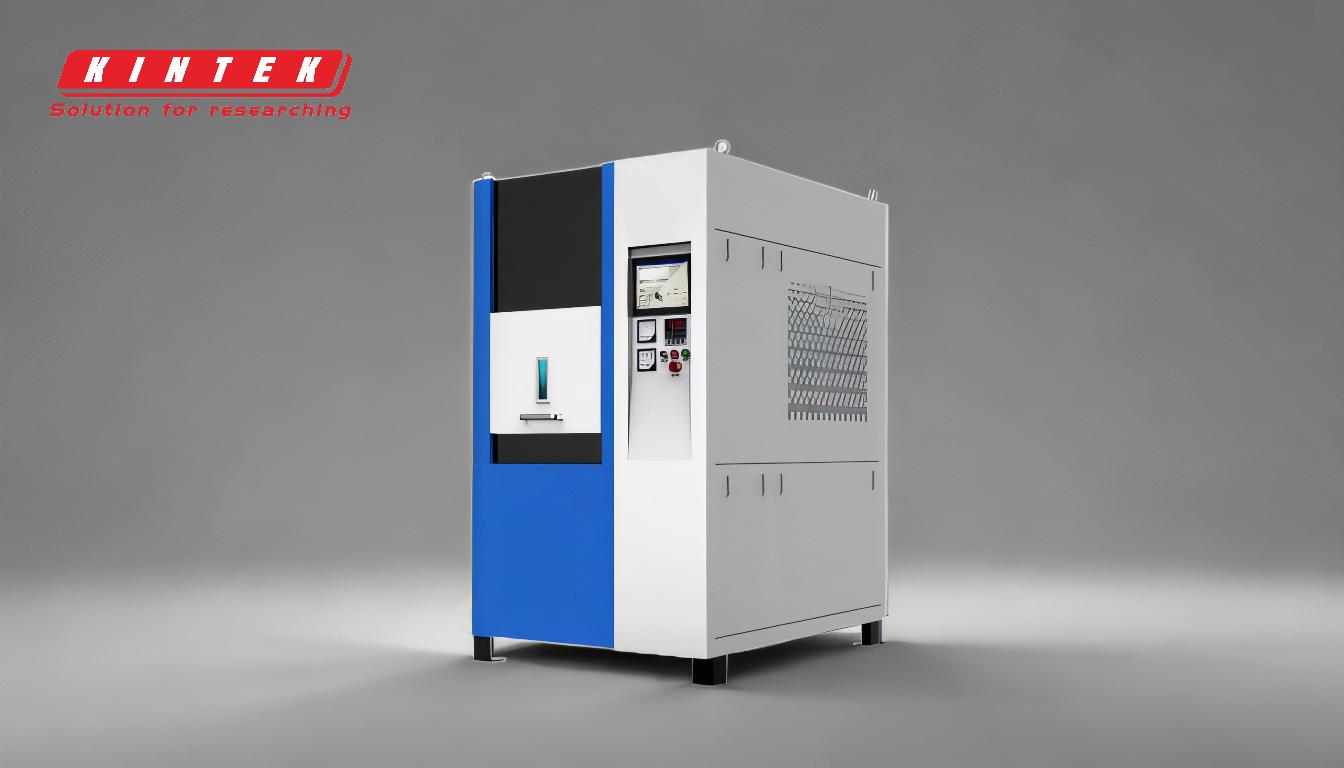
-
Definition and Basic Principle of Reactive Sputtering:
- Reactive sputtering is a variation of the plasma sputtering process where a reactive gas (e.g., oxygen, nitrogen) is introduced into the vacuum chamber alongside an inert gas (e.g., argon).
- The target material is bombarded with ions, causing atoms to be ejected from the target. These atoms then react with the reactive gas to form compounds (e.g., oxides, nitrides), which are deposited as thin films on the substrate.
-
Role of Reactive and Inert Gases:
- Inert Gas (Argon): Provides the plasma environment necessary for sputtering the target material.
- Reactive Gas (Oxygen, Nitrogen): Chemically reacts with the sputtered target atoms to form compounds (e.g., silicon oxide, titanium nitride) that are deposited as thin films.
- The ratio of reactive to inert gas can be adjusted to control the stoichiometry and properties of the deposited film.
-
Chemical Reactions in the Process:
- The reactive gas becomes ionized in the plasma and reacts with the sputtered target atoms. For example:
- Silicon + Oxygen → Silicon Oxide (SiO₂)
- Titanium + Nitrogen → Titanium Nitride (TiN)
- These reactions occur in the vacuum chamber, and the resulting compounds are deposited on the substrate.
- The reactive gas becomes ionized in the plasma and reacts with the sputtered target atoms. For example:
-
Control of Film Properties:
- By varying the partial pressures of the reactive and inert gases, the composition and stoichiometry of the film can be precisely controlled.
- This control is crucial for optimizing functional properties such as stress, refractive index, and electrical conductivity.
-
Hysteresis-Like Behavior and Process Challenges:
- The introduction of a reactive gas complicates the sputtering process, often leading to hysteresis-like behavior.
- This behavior requires careful control of parameters such as gas flow rates, partial pressures, and power levels to maintain stable deposition conditions.
-
Applications of Reactive Sputtering:
- Semiconductors: Used to deposit dielectric layers, barrier layers, and conductive coatings.
- Optics: Produces anti-reflective coatings, mirrors, and optical filters.
- Coatings: Creates wear-resistant, corrosion-resistant, and decorative coatings.
-
Variants of Reactive Sputtering:
- DC Reactive Sputtering: Uses direct current to generate the plasma and is suitable for conductive target materials.
- RF (Radio Frequency) Reactive Sputtering: Used for insulating target materials and provides better control over the deposition process.
-
Advantages of Reactive Sputtering:
- Enables the deposition of compound films with precise stoichiometry.
- Allows for the creation of films with tailored functional properties.
- Compatible with a wide range of target materials and reactive gases.
-
Disadvantages and Limitations:
- The process is more complex than conventional sputtering due to the need to control reactive gas interactions.
- Hysteresis behavior can make process optimization challenging.
- Requires sophisticated equipment and precise parameter control.
-
The Berg Model:
- The Berg Model is a theoretical framework used to predict the effects of reactive gas introduction on target erosion and film deposition rates.
- It helps in understanding and optimizing the reactive sputtering process by modeling the interactions between the target, reactive gas, and plasma.
In summary, reactive sputtering is a powerful and versatile technique for depositing thin films with controlled composition and properties. Its ability to produce high-quality compound films makes it indispensable in various high-tech industries. However, the process requires careful parameter control and advanced equipment to achieve optimal results.
Summary Table:
Aspect | Details |
---|---|
Process | Combines inert gas (argon) and reactive gas (oxygen/nitrogen) to form thin films. |
Key Reactions | Silicon + Oxygen → Silicon Oxide (SiO₂), Titanium + Nitrogen → Titanium Nitride (TiN). |
Applications | Semiconductors, optics (anti-reflective coatings), wear-resistant coatings. |
Advantages | Precise stoichiometry, tailored functional properties, wide material compatibility. |
Challenges | Hysteresis behavior, complex parameter control, advanced equipment required. |
Discover how reactive sputtering can elevate your thin film production—contact our experts today!