The critical speed of a ball mill is a fundamental concept in grinding operations, defining the rotational speed at which the grinding medium (typically steel balls) begins to centrifuge against the inner wall of the mill. At this speed, the grinding medium no longer tumbles and impacts the material, rendering the grinding process ineffective. To ensure efficient grinding, the ball mill must operate above its critical speed, allowing the grinding medium to cascade and impact the material effectively. Understanding and controlling the critical speed is essential for optimizing grinding efficiency, energy consumption, and the quality of the final product.
Key Points Explained:
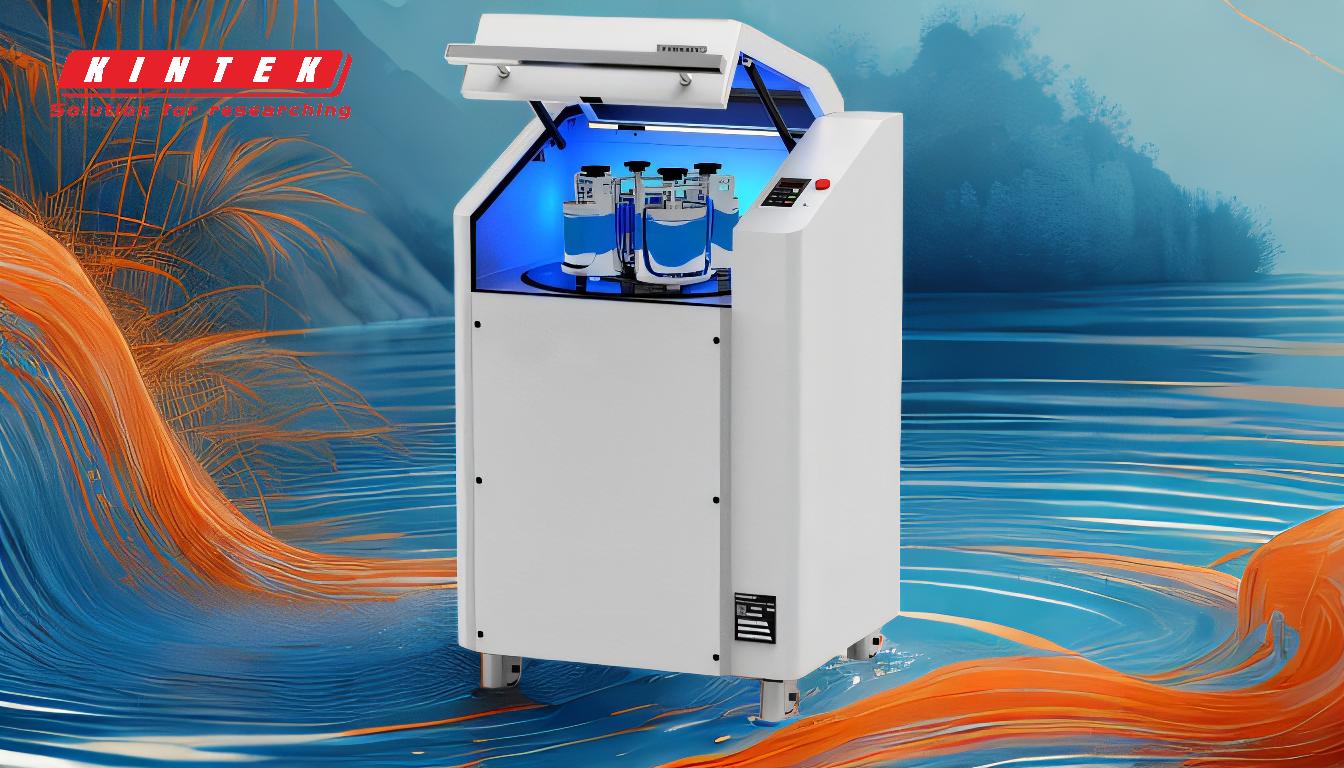
-
Definition of Critical Speed:
- Critical speed is the rotational speed at which the grinding medium (balls) in a ball mill begins to centrifuge against the inner wall of the mill.
- At this speed, the centrifugal force equals the gravitational force, causing the balls to stick to the mill's inner wall and rotate with it.
- This results in no grinding action, as the balls are not tumbling or impacting the material.
-
Impact on Grinding Efficiency:
- When the ball mill operates at or below its critical speed, the grinding medium remains stationary at the bottom or rotates with the mill without tumbling.
- This lack of movement means there is no impact or abrasion on the material, leading to ineffective grinding.
- To achieve effective grinding, the mill must operate above the critical speed, ensuring the balls cascade and impact the material, breaking it down into smaller particles.
-
Importance in Ball Mill Operation:
- Optimal Speed Range: Ball mills are typically operated at 65% to 75% of the critical speed. This range ensures that the grinding medium cascades and impacts the material effectively without excessive wear on the mill's lining.
- Energy Efficiency: Operating above the critical speed ensures that energy is used efficiently for grinding rather than being wasted on ineffective rotation of the grinding medium.
- Product Quality: Proper control of the operating speed relative to the critical speed ensures consistent particle size distribution and high-quality grinding results.
-
Factors Influencing Critical Speed:
- Mill Diameter: The critical speed is inversely proportional to the square root of the mill diameter. Larger mills have lower critical speeds.
- Grinding Medium Size and Density: The size and density of the grinding balls also affect the critical speed. Heavier or larger balls may require higher speeds to achieve the same centrifugal effect.
- Mill Lining: The type of lining inside the mill can influence the critical speed by affecting the friction between the grinding medium and the mill wall.
-
Practical Considerations for Equipment Purchasers:
- Mill Design: When selecting a ball mill, it is crucial to consider the critical speed in relation to the mill's diameter and the intended grinding application. Mills designed for finer grinding may require higher operating speeds relative to their critical speed.
- Operational Flexibility: Purchasers should look for mills that allow easy adjustment of the operating speed to optimize performance for different materials and grinding requirements.
- Maintenance and Wear: Operating above the critical speed can lead to increased wear on the mill's lining and grinding medium. Purchasers should consider mills with durable materials and designs that minimize wear and maintenance costs.
-
Calculating Critical Speed:
- The critical speed (Nc) of a ball mill can be calculated using the formula: [ N_c = \frac{42.3}{\sqrt{D}} ] where ( D ) is the internal diameter of the mill in meters.
- This formula helps in determining the optimal operating speed for a given mill, ensuring efficient grinding without exceeding the critical speed.
In summary, the critical speed of a ball mill is a pivotal parameter that directly impacts the efficiency and effectiveness of the grinding process. Understanding and controlling this speed is essential for optimizing grinding operations, ensuring energy efficiency, and achieving high-quality grinding results. For equipment purchasers, considering the critical speed in relation to mill design, operational flexibility, and maintenance requirements is crucial for selecting the right ball mill for their specific needs.
Summary Table:
Aspect | Details |
---|---|
Definition | Rotational speed where grinding medium centrifuges against the mill wall. |
Optimal Speed Range | 65% to 75% of critical speed for effective grinding. |
Key Factors | Mill diameter, grinding medium size/density, and mill lining. |
Impact on Efficiency | Ensures cascading and impacting of grinding medium for effective grinding. |
Energy Efficiency | Reduces wasted energy by operating above critical speed. |
Product Quality | Maintains consistent particle size and high-quality grinding results. |
Calculation Formula | ( N_c = \frac{42.3}{\sqrt{D}} ), where ( D ) is mill diameter in meters. |
Ready to optimize your grinding operations? Contact us today to find the perfect ball mill for your needs!