The size reduction mechanism in a ball mill primarily relies on the principles of impact and attrition. When the mill operates at an optimal speed, the grinding balls inside the cylinder are lifted to a certain height and then cascade down, impacting the material and breaking it into smaller particles. Simultaneously, the rolling and sliding of the balls against each other and the material cause attrition, further reducing particle size. The efficiency of size reduction depends on factors such as the speed of the mill, the size and quantity of grinding balls, and the material properties. Proper operation ensures maximum particle size reduction through a combination of these mechanisms.
Key Points Explained:
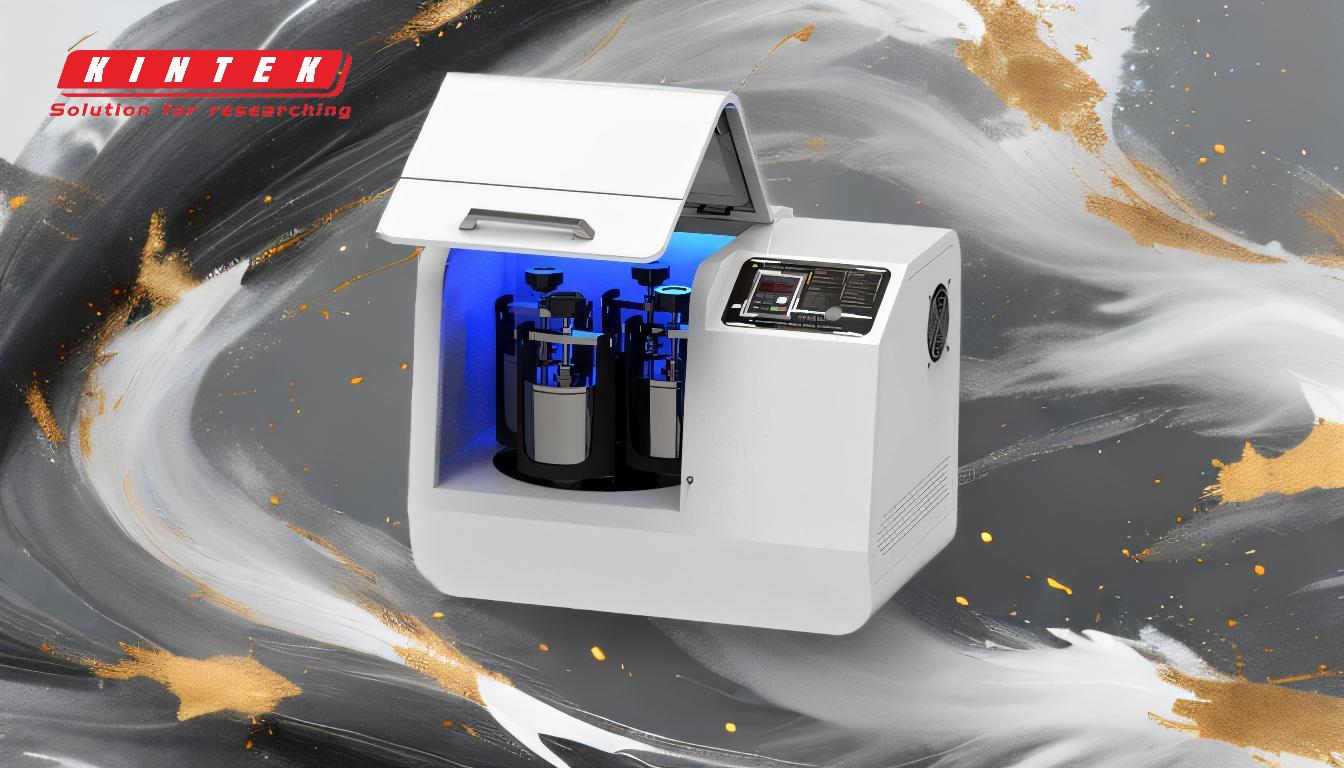
-
Mechanisms of Size Reduction:
- Impact: When the grinding balls are lifted to a certain height and cascade down, they collide with the material, breaking it into smaller particles. This is the primary mechanism for size reduction in a ball mill.
- Attrition: The rolling and sliding of the grinding balls against each other and the material cause friction, which grinds the particles into finer sizes. This secondary mechanism complements the impact process.
-
Role of Mill Speed:
- Low Speed: At low speeds, the balls slide or roll over each other, resulting in minimal size reduction due to insufficient energy for effective impact or attrition.
- High Speed: At high speeds, centrifugal force causes the balls to stick to the cylinder wall, preventing them from cascading and reducing grinding efficiency.
- Optimal Speed: At the correct speed, the balls are carried to the top of the cylinder and then fall in a cascade, maximizing impact and attrition for effective size reduction.
-
Grinding Balls:
- The size, quantity, and material of the grinding balls significantly influence the size reduction process. Larger balls are more effective for coarse grinding, while smaller balls are better for fine grinding.
- The balls must be of sufficient hardness to avoid excessive wear and contamination of the material being ground.
-
Material Properties:
- The hardness, brittleness, and moisture content of the material being ground affect the efficiency of size reduction. Brittle materials are more easily reduced in size compared to ductile ones.
- Overloading the mill with material can reduce grinding efficiency, as there may not be enough space for the balls to move freely.
-
Operational Considerations:
- The mill must be operated at the correct speed to achieve the desired particle size. This requires careful adjustment and monitoring.
- The duration of grinding also plays a role. Longer grinding times generally result in finer particles but may also lead to increased wear on the mill and balls.
-
Comparison with Other Mills:
- Unlike vibrating mills, which rely on high-frequency vibrations for size reduction, ball mills use rotational energy to achieve grinding.
- Ball mills are versatile and can handle a wide range of materials, making them suitable for both laboratory and industrial applications.
By understanding these key points, equipment and consumable purchasers can make informed decisions about selecting the right ball mill and operating parameters to achieve the desired particle size reduction efficiently.
Summary Table:
Key Factor | Description |
---|---|
Mechanisms | Impact (primary) and attrition (secondary) break materials into smaller particles. |
Mill Speed | Optimal speed maximizes impact and attrition; low or high speeds reduce efficiency. |
Grinding Balls | Size, quantity, and material affect grinding efficiency; larger balls for coarse, smaller for fine grinding. |
Material Properties | Hardness, brittleness, and moisture content influence grinding efficiency. |
Operational Considerations | Correct speed, grinding time, and material load are critical for effective size reduction. |
Comparison with Other Mills | Ball mills use rotational energy, making them versatile for various materials and applications. |
Need help selecting the right ball mill for your needs? Contact our experts today!