Sputtering is a physical vapor deposition (PVD) technique used to deposit thin films of materials onto a substrate. It involves creating a vacuum in a chamber, introducing an inert gas (typically argon), and applying a high voltage to ionize the gas. The ionized gas atoms are accelerated toward a target material, causing atoms to be ejected from the target due to collisions. These ejected atoms then travel through the vacuum and deposit onto a substrate, forming a thin, uniform coating. The process is widely used in industries such as semiconductors, optics, and decorative coatings due to its precision and ability to deposit a wide range of materials.
Key Points Explained:
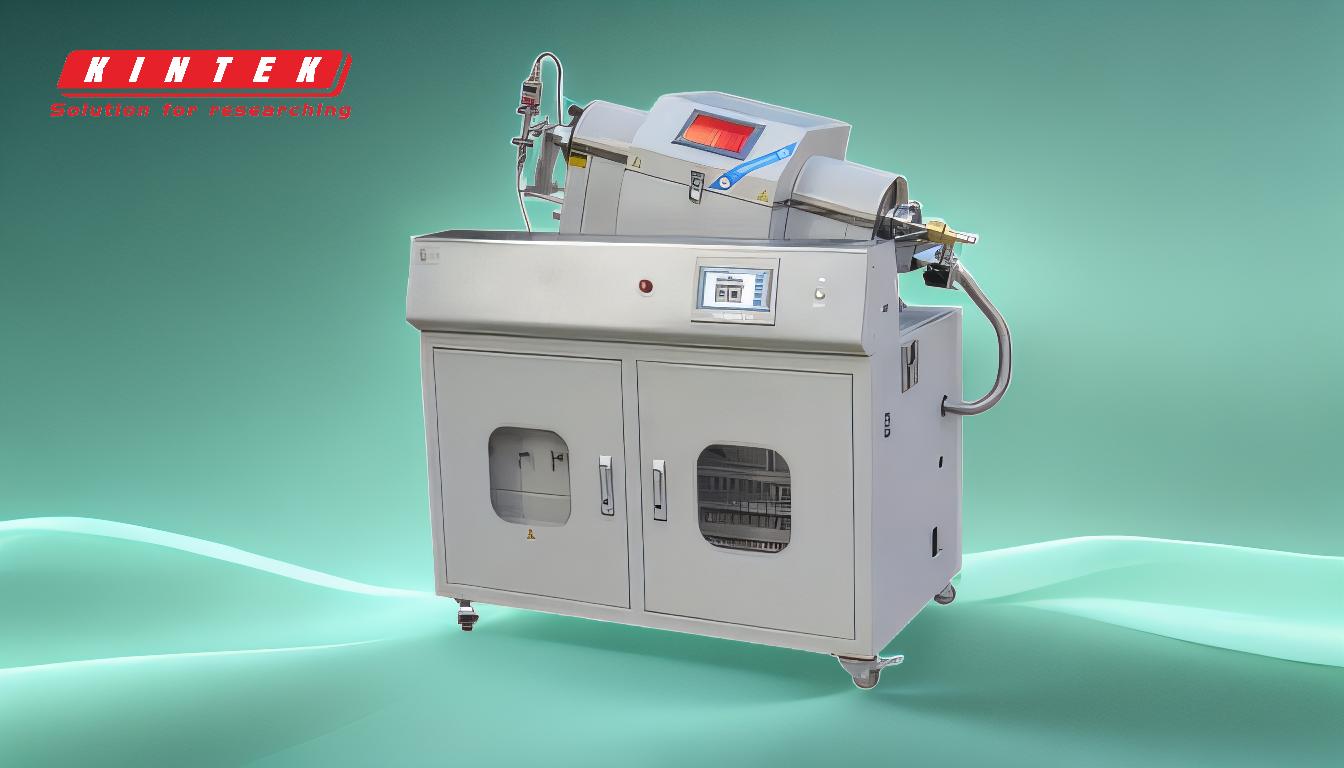
-
Vacuum Creation:
- The first step in sputtering is to create a vacuum inside the reaction chamber, reducing the pressure to around 1 Pa (0.0000145 psi). This removes moisture and impurities, ensuring a clean environment for deposition.
- A vacuum is essential because it minimizes contamination and allows the inert gas to ionize effectively.
-
Introduction of Inert Gas:
- An inert gas, typically argon, is introduced into the chamber to create a low-pressure atmosphere. Argon is preferred because it is chemically inert and does not react with the target material or substrate.
- The gas atoms are ionized in the next steps to create the plasma necessary for sputtering.
-
Heating the Chamber:
- The chamber is heated to temperatures ranging from 150°C to 750°C (302°F to 1382°F), depending on the material being deposited. Heating improves the adhesion of the coating and ensures a uniform film.
- Higher temperatures are often used for more complex materials or to enhance the film's properties.
-
Creation of a Magnetic Field:
- A magnetic field is generated using electromagnets placed around the target material. This field confines the plasma and increases the efficiency of the sputtering process by trapping electrons near the target.
- The magnetic field enhances the ionization of the inert gas, leading to a higher density of ions available for sputtering.
-
Ionization of Gas Atoms:
- A high voltage (3-5 kV) is applied to the target, which is negatively charged. This voltage ionizes the argon gas atoms, creating positively charged argon ions and free electrons.
- The ionization process generates a plasma, which is essential for the sputtering mechanism.
-
Bombardment of the Target:
- The positively charged argon ions are accelerated toward the negatively charged target due to the electric field. When these ions collide with the target, they transfer their energy to the target atoms.
- This energy transfer causes target atoms to be ejected from the surface in a process known as sputtering.
-
Transport of Sputtered Atoms:
- The ejected target atoms travel through the vacuum chamber in a straight line due to the low pressure. This ensures that the atoms reach the substrate without significant scattering.
- The vacuum environment also prevents contamination from residual gases.
-
Deposition on the Substrate:
- The sputtered atoms condense on the substrate, forming a thin film. The film's thickness and uniformity depend on factors such as the sputtering rate, target-substrate distance, and substrate temperature.
- The resulting film adheres securely to the substrate, providing excellent mechanical, optical, or electrical properties.
-
Advantages of Sputtering:
- Sputtering allows for the deposition of a wide range of materials, including metals, alloys, and ceramics.
- It produces high-quality, uniform films with excellent adhesion and minimal defects.
- The process is scalable and can be used for large-area coatings or intricate geometries.
-
Applications of Sputtering:
- Sputtering is widely used in the semiconductor industry to deposit thin films for integrated circuits and microelectronics.
- It is also used in optics for anti-reflective coatings, in decorative coatings for consumer products, and in energy applications such as solar cells.
By following these steps, the sputtering process enables precise and controlled deposition of thin films, making it a cornerstone of modern materials science and manufacturing.
Summary Table:
Step | Description |
---|---|
Vacuum Creation | Reduces pressure to ~1 Pa, removes impurities, and ensures a clean environment. |
Inert Gas Introduction | Argon is introduced to create a low-pressure atmosphere for ionization. |
Chamber Heating | Heated to 150°C–750°C to improve adhesion and film uniformity. |
Magnetic Field Creation | Confines plasma and increases sputtering efficiency. |
Gas Ionization | High voltage ionizes argon gas, generating plasma. |
Target Bombardment | Argon ions collide with the target, ejecting atoms. |
Atom Transport | Sputtered atoms travel through the vacuum to the substrate. |
Deposition | Atoms condense on the substrate, forming a thin, uniform film. |
Advantages | High-quality, uniform films; scalable; works with metals, alloys, and ceramics. |
Applications | Semiconductors, optics, decorative coatings, and solar cells. |
Discover how sputtering can enhance your manufacturing process—contact our experts today!