The target substrate distance in sputtering is a critical parameter that directly influences the quality, uniformity, and thickness of the deposited thin film. This distance must be carefully controlled to ensure optimal deposition conditions, as it affects the kinetic energy of the sputtered particles, their directionality, and the overall deposition rate. The ideal target substrate distance varies depending on factors such as the sputtering method, target material, substrate material, chamber pressure, and sputtering power. Generally, a distance of 5 to 15 cm is commonly used, but specific applications may require adjustments to achieve the desired film properties. Proper spacing ensures uniform coverage, minimizes defects, and enhances the overall quality of the coating.
Key Points Explained:
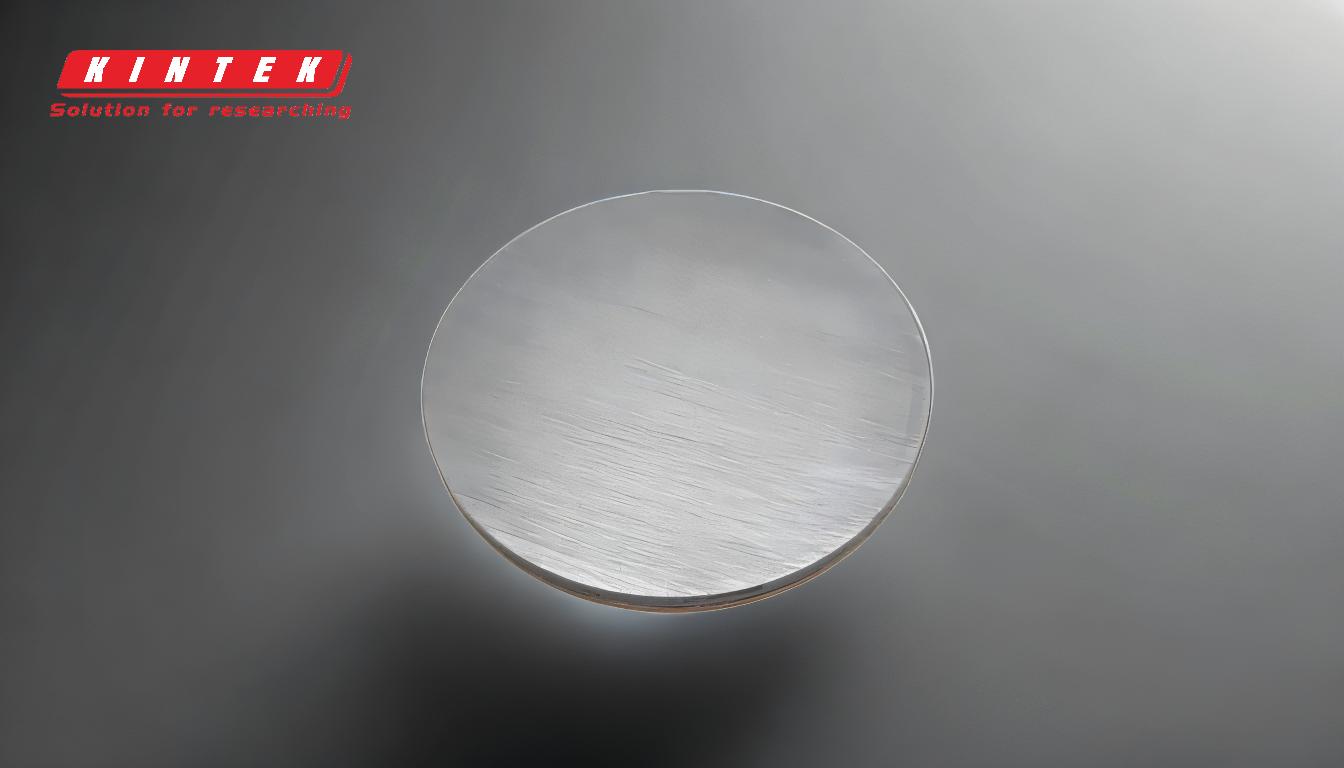
-
Importance of Target Substrate Distance:
- The distance between the target and substrate is crucial for achieving uniform thin film deposition.
- It affects the kinetic energy and directionality of the sputtered particles, which in turn influences the film's thickness, uniformity, and quality.
- Proper spacing ensures consistent deposition rates and minimizes defects such as uneven coating or voids.
-
Typical Range for Target Substrate Distance:
- A common range for target substrate distance in sputtering is 5 to 15 cm.
- This range is suitable for most standard sputtering applications, providing a balance between deposition rate and film quality.
- However, the exact distance may need to be adjusted based on specific experimental or industrial requirements.
-
Factors Influencing the Optimal Distance:
- Sputtering Method: Different sputtering techniques (e.g., DC, RF, magnetron) may require varying distances due to differences in ion energy and deposition mechanisms.
- Target and Substrate Materials: The mass and properties of the target and substrate materials influence the sputtering yield and particle behavior.
- Chamber Pressure: Higher pressures can reduce the mean free path of particles, requiring shorter distances to maintain deposition efficiency.
- Sputtering Power: Higher power levels can increase the energy of sputtered particles, potentially allowing for greater target substrate distances without compromising film quality.
-
Impact on Deposition Rate and Film Quality:
- Deposition Rate: A shorter distance generally increases the deposition rate due to reduced particle scattering and higher particle flux on the substrate.
- Film Quality: A longer distance can improve film uniformity by allowing particles to spread more evenly across the substrate, but it may also reduce deposition efficiency.
-
Practical Considerations for Equipment Setup:
- Uniformity: Ensuring the substrate is positioned parallel to the target surface is essential for achieving uniform film thickness.
- Adjustability: Sputtering systems should allow for precise adjustment of the target substrate distance to accommodate different materials and process conditions.
- Monitoring: Real-time monitoring of film thickness and quality can help optimize the distance during the sputtering process.
-
Application-Specific Adjustments:
- High-Precision Coatings: For applications requiring extremely uniform or defect-free coatings, the target substrate distance may need to be minimized and carefully controlled.
- Large-Scale Deposition: In industrial settings, larger distances may be used to coat larger substrates or multiple substrates simultaneously, though this may require adjustments to other parameters (e.g., power, pressure) to maintain quality.
-
Experimental Optimization:
- The optimal target substrate distance is often determined experimentally for specific applications.
- Factors such as the desired film thickness, substrate size, and material properties should guide the optimization process.
In summary, the target substrate distance in sputtering is a key parameter that must be carefully controlled to achieve high-quality thin film deposition. While a general range of 5 to 15 cm is commonly used, the exact distance should be tailored to the specific sputtering method, materials, and application requirements. Proper spacing ensures uniform deposition, minimizes defects, and enhances the overall performance of the coated substrate.
Summary Table:
Key Factor | Impact on Target Substrate Distance |
---|---|
Typical Range | 5 to 15 cm |
Sputtering Method | DC, RF, or magnetron sputtering may require adjustments in distance for optimal ion energy and yield. |
Target/Substrate Materials | Material mass and properties affect sputtering yield and particle behavior. |
Chamber Pressure | Higher pressure may require shorter distances to maintain deposition efficiency. |
Sputtering Power | Higher power allows for greater distances without compromising film quality. |
Deposition Rate | Shorter distances increase deposition rate; longer distances improve uniformity. |
Application-Specific Needs | High-precision coatings or large-scale deposition may require tailored distances. |
Need help optimizing your sputtering process? Contact our experts today for tailored solutions!