Thermal evaporation is a widely used technique in thin-film deposition, where a material is heated to its evaporation point, causing it to vaporize and condense onto a substrate to form a thin film. The temperature required for thermal evaporation depends on the material being evaporated, as each material has a unique evaporation point. This process typically involves heating the material using resistive heating elements like boats, coils, or baskets, and the temperature can range from a few hundred degrees Celsius to over 2000°C, depending on the material's properties.
Key Points Explained:
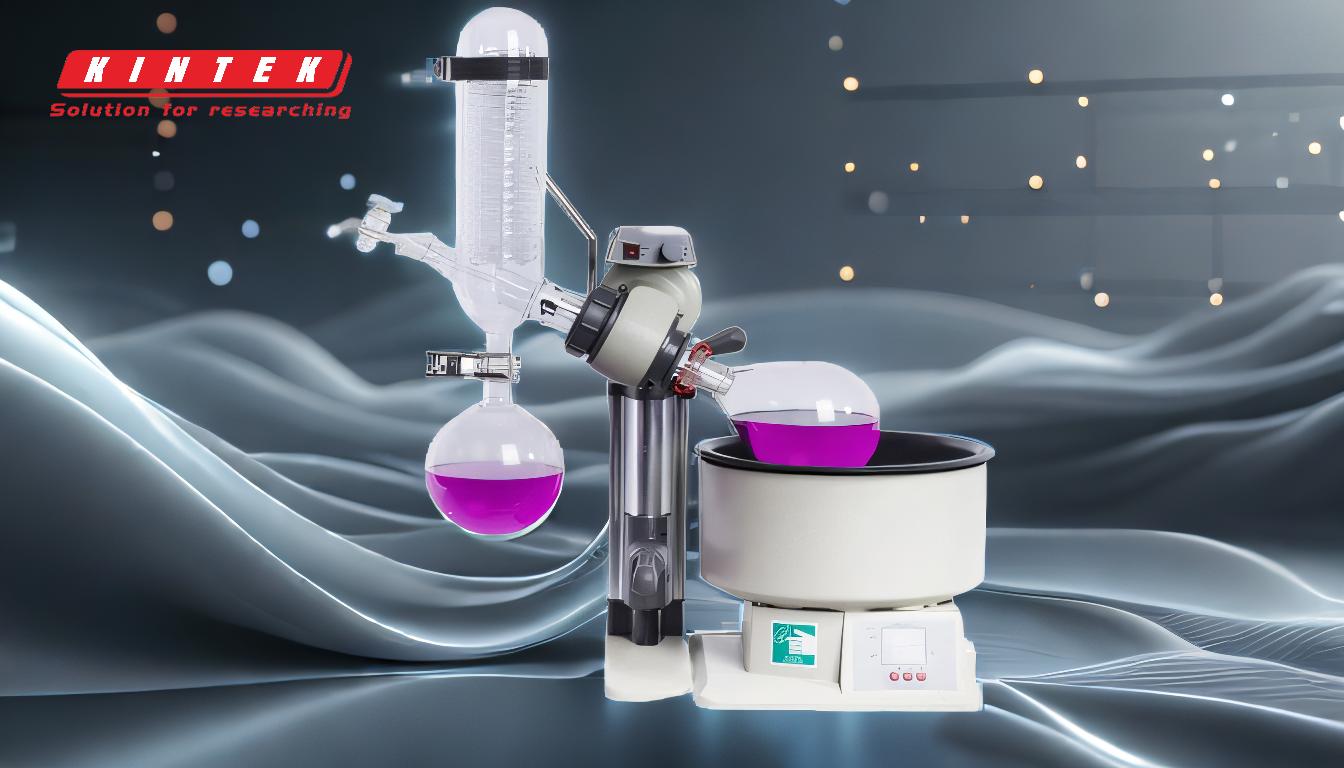
-
Principle of Thermal Evaporation:
- Thermal evaporation relies on heating a target material until it reaches its evaporation point. This is achieved by passing an electric current through a resistive heating element, which generates heat due to electrical resistance.
- The vaporized material then travels through a vacuum chamber and deposits onto a substrate, forming a thin, uniform film.
-
Temperature Range in Thermal Evaporation:
- The temperature required for thermal evaporation varies significantly depending on the material. For example:
- Low-melting-point materials like organic compounds may require temperatures as low as 100–300°C.
- Metals such as aluminum or gold typically need temperatures between 1000°C and 1500°C.
- High-melting-point materials like tungsten or ceramics may require temperatures exceeding 2000°C.
- The exact temperature is determined by the material's vapor pressure and evaporation rate, which must be sufficient to achieve the desired deposition.
- The temperature required for thermal evaporation varies significantly depending on the material. For example:
-
Factors Influencing Evaporation Temperature:
- Material Properties: The melting point, vapor pressure, and thermal conductivity of the material dictate the required temperature.
- Vacuum Conditions: A high vacuum environment (typically 10^-5 to 10^-7 Torr) is essential to minimize contamination and ensure efficient vapor transport.
- Heating Source Design: The type of heating element (e.g., tungsten boat, tantalum basket, or coiled filament) affects the temperature distribution and evaporation efficiency.
-
Applications of Thermal Evaporation:
- Thermal evaporation is commonly used in industries such as electronics, optics, and coatings. It is ideal for depositing metals, semiconductors, and dielectric materials.
- The process is favored for its simplicity, high deposition rates, and ability to produce high-purity films.
-
Advantages and Limitations:
-
Advantages:
- High deposition rates and straightforward operation.
- Suitable for a wide range of materials, including metals and alloys.
- Produces films with excellent adhesion and uniformity.
-
Limitations:
- High temperatures can damage heat-sensitive substrates.
- Limited to materials with relatively low melting points compared to other deposition methods like sputtering or thermal evaporation.
-
Advantages:
-
Comparison with Other Deposition Techniques:
- Unlike sputtering or chemical vapor deposition (CVD), thermal evaporation does not require reactive gases or plasma, making it a cleaner and simpler process.
- However, it is less suitable for depositing complex compounds or materials with extremely high melting points.
In summary, the temperature in thermal evaporation is highly material-dependent, ranging from a few hundred degrees Celsius to over 2000°C. The process is versatile and widely used for thin-film deposition, but it requires careful control of temperature, vacuum conditions, and heating source design to achieve optimal results.
Summary Table:
Material Type | Temperature Range |
---|---|
Organic Compounds | 100–300°C |
Metals (e.g., Al, Au) | 1000–1500°C |
High-Melting Materials | >2000°C |
Need help selecting the right thermal evaporation setup? Contact our experts today!