RF sputtering is a thin-film deposition technique widely used in industries such as semiconductors, optics, and photonics. It employs an alternating current (AC) power source, typically at 13.56 MHz, to create a high-frequency electrical potential in a vacuum environment. This alternating potential prevents charge buildup on insulating materials, making RF sputtering suitable for both conductive and non-conductive target materials. The process involves two cycles: the positive cycle, where electrons are attracted to the target, creating a negative bias, and the negative cycle, where ion bombardment ejects target atoms and gas ions toward the substrate to form a high-quality film. RF sputtering is particularly effective for depositing dielectric materials, fabricating optical waveguides, and creating photonic microcavities, offering precise control over film thickness and refractive index. However, it has a lower deposition rate compared to DC sputtering and is generally more expensive, limiting its use to smaller substrates.
Key Points Explained:
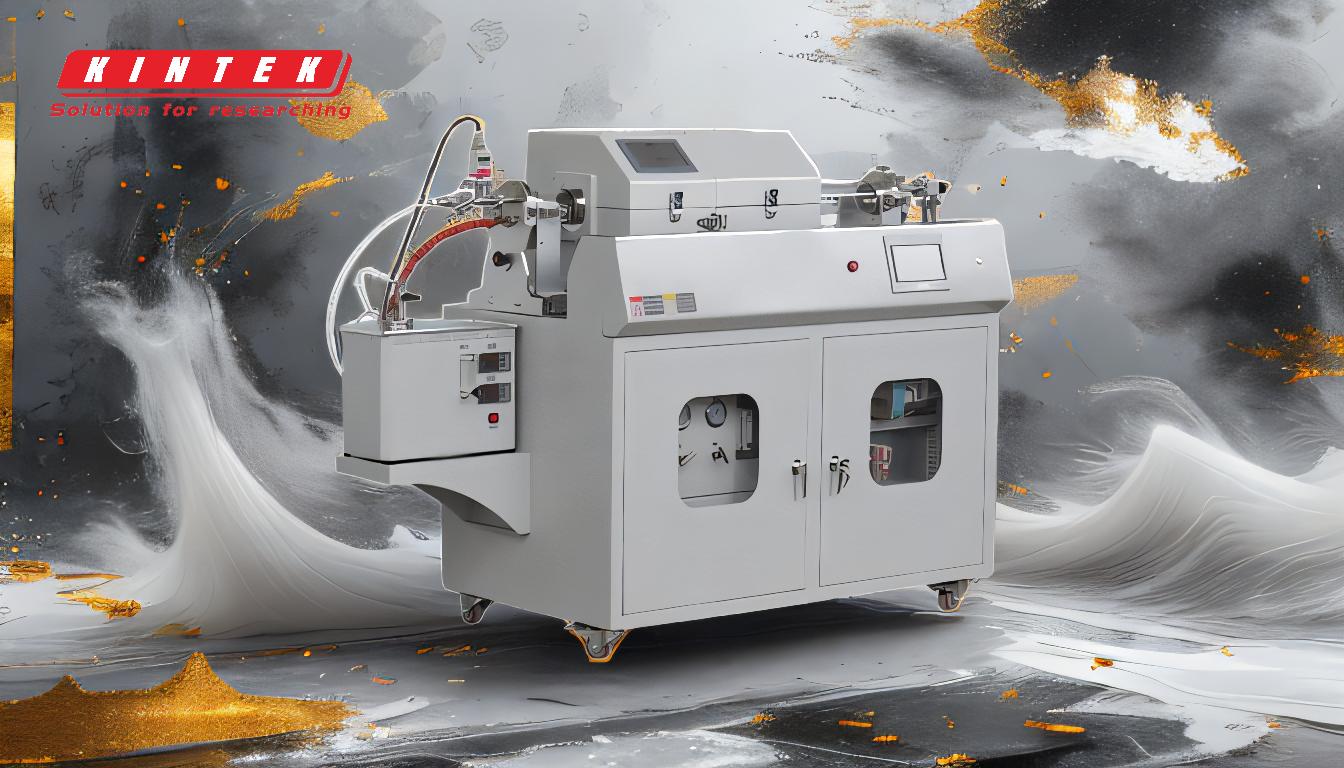
-
Principle of RF Sputtering:
- RF sputtering uses an alternating current (AC) power source, typically at 13.56 MHz, to create a high-frequency electrical potential.
- The alternating potential prevents charge buildup on insulating materials, making it suitable for both conductive and non-conductive targets.
- The process involves two cycles:
- Positive Cycle: Electrons are attracted to the target, creating a negative bias.
- Negative Cycle: Ion bombardment ejects target atoms and gas ions toward the substrate for deposition.
-
Equipment and Setup:
- Power Source: High-voltage RF source fixed at 13.56 MHz with a peak-to-peak voltage of 1000 V.
- Chamber Pressure: Typically maintained between 0.5 to 10 mTorr.
- Electron Density: Ranges from 10^9 to 10^11 Cm^-3.
- Matching Network: Ensures efficient power transfer and minimizes reflected power.
-
Applications of RF Sputtering:
- Optical and Photonic Devices: Used to fabricate optical planar waveguides, photonic microcavities, and 1-D photonic crystals operating in the visible and near-infrared (NIR) regions.
- Semiconductor Industry: Deposits high-quality thin films for computer and semiconductor applications.
- Dielectric Materials: Ideal for depositing alternating layers of different materials with controlled refractive index and thickness.
-
Advantages of RF Sputtering:
- Versatility: Can deposit both conductive and insulating materials.
- High-Quality Films: Produces films with excellent uniformity, density, and adhesion.
- Low Substrate Temperature: Suitable for temperature-sensitive substrates.
- Precision: Offers precise control over film thickness and composition.
-
Limitations of RF Sputtering:
- Lower Deposition Rate: Compared to DC sputtering, RF sputtering has a slower deposition rate.
- Higher Cost: The equipment and operational costs are higher, making it less economical for large-scale production.
- Substrate Size: Typically used for smaller substrates due to cost and technical constraints.
-
Process Optimization:
- Frequency and Power: The 13.56 MHz frequency is standard to avoid interference with communication bands. Power levels are optimized for specific materials and applications.
- Gas Selection: Inert gases like argon are commonly used to create plasma and sputter target materials.
- Target Material: The choice of target material depends on the desired film properties, such as conductivity, refractive index, and thermal stability.
-
Challenges and Solutions:
- Charge Buildup: Alternating the electrical potential prevents charge buildup on insulating targets, avoiding arcing and ensuring consistent film quality.
- Ion Bombardment: Continuous ion bombardment during the negative cycle ensures efficient sputtering of non-conductive materials.
- Matching Network: A properly tuned matching network is critical to minimize power loss and maintain stable plasma conditions.
-
Comparison with DC Sputtering:
- Material Compatibility: RF sputtering can handle insulating materials, whereas DC sputtering is limited to conductive targets.
- Deposition Rate: RF sputtering generally has a lower deposition rate compared to DC sputtering.
- Cost and Complexity: RF sputtering systems are more complex and expensive, making them less suitable for high-volume production.
By understanding these key points, equipment and consumable purchasers can make informed decisions about implementing RF sputtering for specific applications, balancing the benefits of high-quality film deposition with the associated costs and limitations.
Summary Table:
Aspect | Details |
---|---|
Principle | Uses 13.56 MHz AC power to prevent charge buildup on insulating materials. |
Equipment | RF source (13.56 MHz), chamber pressure (0.5–10 mTorr), matching network. |
Applications | Optical waveguides, photonic microcavities, semiconductor thin films. |
Advantages | Versatile, high-quality films, low substrate temperature, precise control. |
Limitations | Lower deposition rate, higher cost, limited to smaller substrates. |
Optimization | Frequency (13.56 MHz), inert gases (e.g., argon), target material choice. |
Comparison with DC | Handles insulators, slower deposition, more complex and costly. |
Discover how RF sputtering can enhance your thin-film applications—contact us today for expert advice!