The thermal efficiency of a rotary kiln is a critical factor in its performance, influencing energy consumption, operational costs, and environmental impact. While electrical heated rotary kilns can achieve energy efficiencies of over 95% due to minimal heat losses, most rotary kilns operate under more complex conditions where efficiency is influenced by factors such as heat transfer, material properties, and kiln design. Thermal efficiency is not a fixed value but varies depending on the kiln's design, operational parameters, and the materials being processed. By optimizing factors like heat recuperation, combustion efficiency, and material retention time, thermal efficiency can be significantly improved. This answer explores the key factors influencing thermal efficiency and how they can be optimized for better performance.
Key Points Explained:
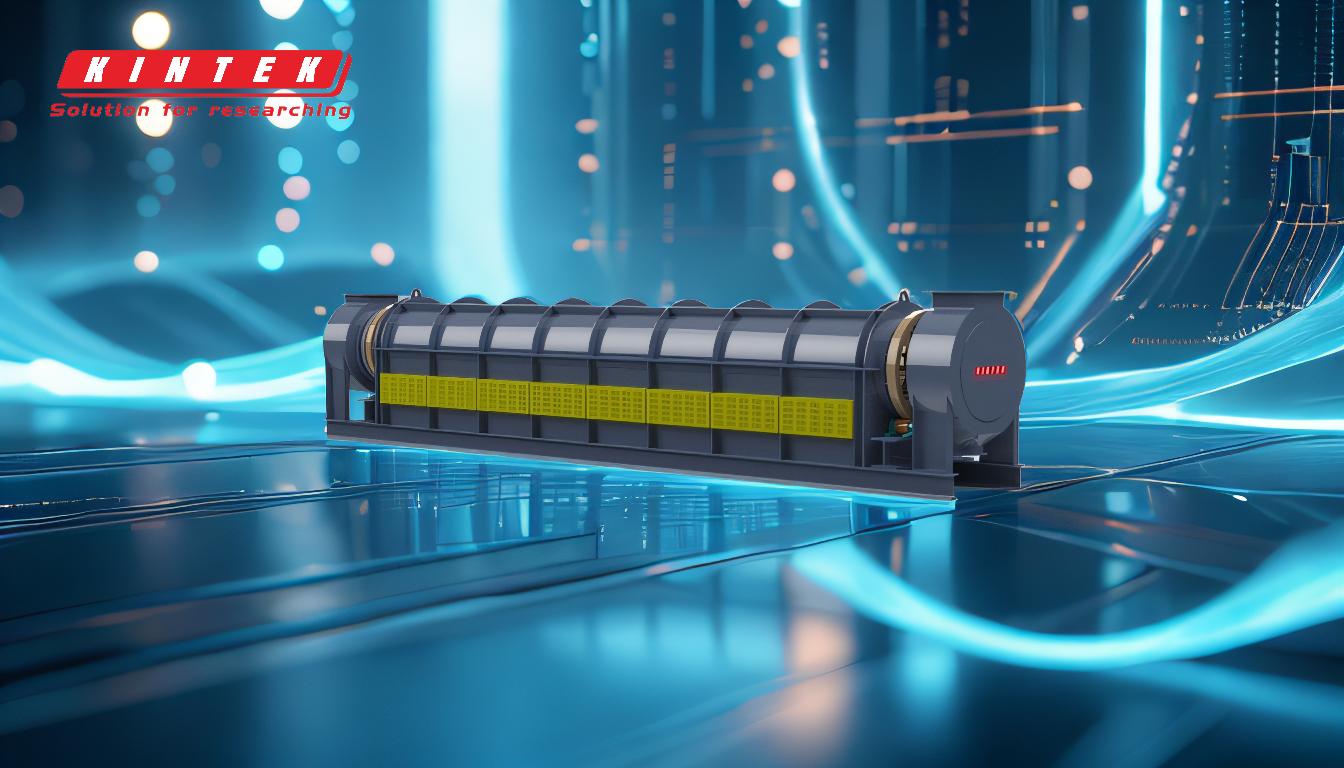
-
Definition of Thermal Efficiency in Rotary Kilns:
- Thermal efficiency refers to the ratio of useful heat energy utilized in the process to the total heat energy supplied to the kiln. It is a measure of how effectively the kiln converts input energy into productive heat for material processing.
- In electrical heated rotary kilns, where there is no gas flow and minimal heat losses, thermal efficiency can exceed 95%. However, in most industrial rotary kilns, efficiency is lower due to heat losses through exhaust gases, radiation, and convection.
-
Factors Influencing Thermal Efficiency:
- Heat Transfer Mechanisms: Efficient heat transfer between the kiln's internal environment and the material being processed is crucial. Factors like material-specific heat, thermal conductivity, and temperature profiles affect heat transfer rates.
- Combustion Efficiency: In fuel-fired kilns, incomplete combustion of fuel can lead to energy waste. Upgrading to multi-channel burners or optimizing burner design can improve combustion efficiency.
- Heat Recuperation: Pre-heaters and coolers are used to recover heat from exhaust gases and hot products, respectively. This recovered heat can preheat combustion air or feed materials, reducing overall energy consumption.
- Retention Time: The time materials spend in the kiln affects how thoroughly they are heated. Optimizing retention time ensures complete heat absorption without unnecessary energy expenditure.
-
Design and Operational Parameters:
- Kiln Size and Geometry: The size of the kiln, including its length and diameter, influences heat distribution and retention time. A properly sized kiln ensures optimal heat utilization.
- Inclination Angle and Rotation Speed: These parameters control the movement of materials through the kiln. Proper adjustment ensures uniform heating and prevents energy waste.
- Refractory Lining: Adding a layer of refractory ceramic fiber to the kiln's lining can reduce heat loss and improve thermal efficiency by providing better insulation.
-
Material Properties:
- Particle Size and Bulk Density: Smaller particles and higher bulk densities improve heat transfer by increasing the surface area exposed to heat.
- Chemical Composition and Heat of Reaction: Materials with exothermic reactions can contribute to the kiln's heat balance, reducing the need for external energy input.
- Abrasiveness and Corrosiveness: These properties affect the durability of the kiln's lining and components, indirectly impacting long-term efficiency.
-
Strategies for Improving Thermal Efficiency:
- Regular Maintenance and Monitoring: Ensuring the kiln operates under optimal conditions through routine checks and adjustments prevents energy losses due to malfunctions or wear.
- Upgrading Supporting Equipment: Modernizing burners, pre-heaters, and coolers can enhance combustion and heat recovery, directly improving thermal efficiency.
- Quantitative Analysis of Transport Phenomena: Understanding momentum and energy transport within the kiln bed allows for precise control of particle motion and heating rates, optimizing energy use.
-
Environmental and Economic Implications:
- High thermal efficiency reduces fuel consumption, lowering operational costs and minimizing greenhouse gas emissions.
- Investments in efficiency improvements, such as advanced refractory materials or heat recuperation systems, often yield significant long-term savings and environmental benefits.
By addressing these factors, rotary kiln operators can achieve higher thermal efficiency, leading to more sustainable and cost-effective operations.
Summary Table:
Factor | Impact on Thermal Efficiency |
---|---|
Heat Transfer Mechanisms | Efficient heat transfer ensures uniform heating and reduces energy waste. |
Combustion Efficiency | Optimizing burner design improves fuel utilization and reduces energy loss. |
Heat Recuperation | Recovering heat from exhaust gases and products lowers overall energy consumption. |
Retention Time | Proper retention time ensures complete heat absorption without unnecessary energy expenditure. |
Kiln Size and Geometry | Proper sizing ensures optimal heat distribution and utilization. |
Refractory Lining | Insulating linings reduce heat loss and improve efficiency. |
Material Properties | Particle size, density, and chemical composition affect heat transfer and energy requirements. |
Ready to improve your rotary kiln's thermal efficiency? Contact our experts today for tailored solutions!