The thickness of CVD (Chemical Vapor Deposition) coatings typically ranges from a few microns to around 10 microns. These coatings are known for their fine-grained structure, high purity, and hardness, making them suitable for various industrial applications. The deposition process is relatively slow, often at rates of a few hundred microns per hour, ensuring a high-quality and uniform coating. While PVD (Physical Vapor Deposition) coatings are generally thinner (1-5 microns), CVD coatings tend to be slightly thicker, often falling in the range of 5-10 microns. This thickness ensures durability and performance without significantly altering the dimensions of the engineered parts.
Key Points Explained:
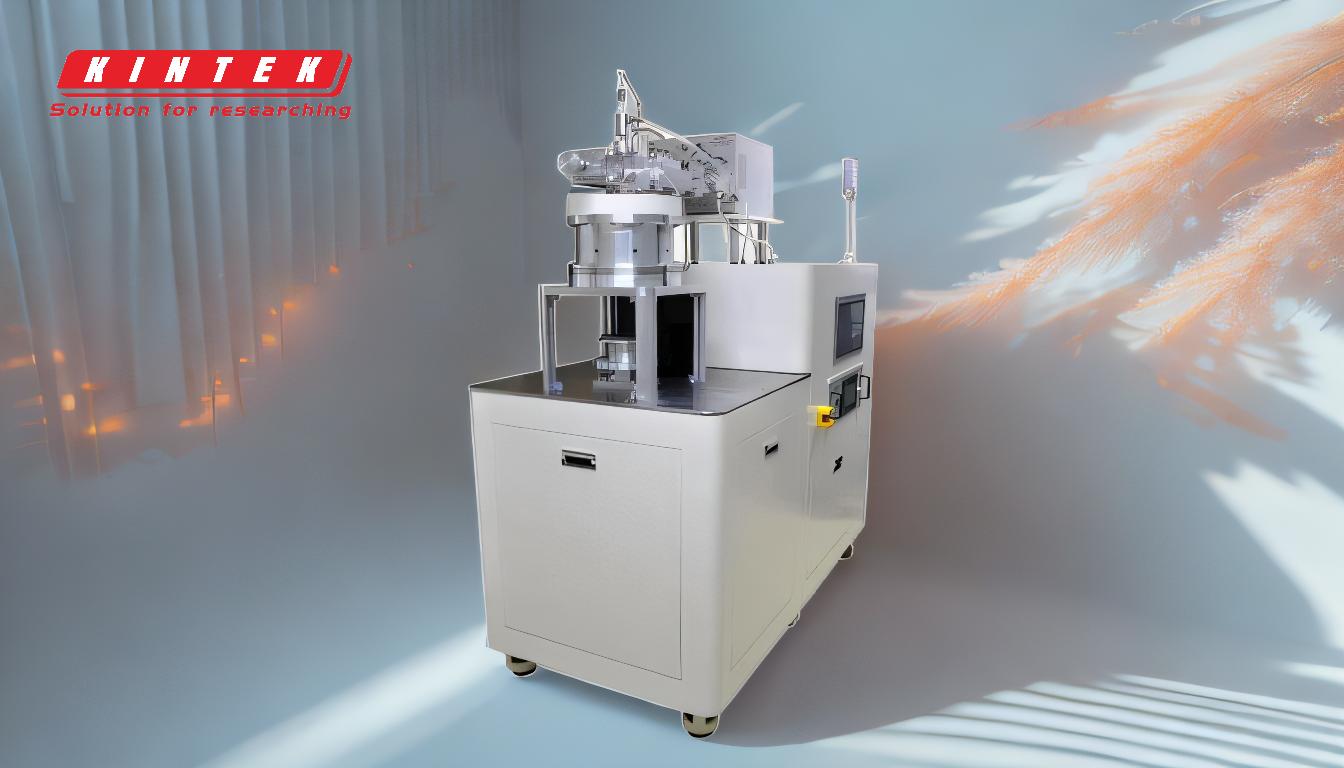
-
Typical Thickness Range of CVD Coatings:
- CVD coatings are usually between 5-10 microns thick. This range ensures that the coating provides sufficient durability and performance without significantly altering the dimensions of the substrate.
- The thickness is carefully controlled to maintain the integrity of the underlying material while providing the desired surface properties.
-
Comparison with PVD Coatings:
- PVD coatings are generally thinner, typically ranging from 1-5 microns. This difference in thickness is due to the distinct deposition processes used in PVD and CVD.
- While PVD coatings are applied in a vacuum environment using physical methods like sputtering or evaporation, CVD involves chemical reactions at the substrate surface, which can result in slightly thicker coatings.
-
Deposition Rate and Process:
- CVD coatings are deposited at relatively slow rates, often a few hundred microns per hour. This slow rate allows for the formation of fine-grained, high-purity coatings with excellent adhesion and uniformity.
- The slow deposition rate also contributes to the hardness and impervious nature of CVD coatings, making them suitable for demanding applications.
-
Properties of CVD Coatings:
- CVD coatings are known for being fine-grained, impervious, and high-purity. These properties make them harder and more durable than similar materials produced using conventional ceramic fabrication processes.
- The hardness of CVD coatings can vary depending on the specific materials and processes used, but they generally offer superior wear resistance and longevity.
-
Applications and Benefits:
- The thickness and properties of CVD coatings make them ideal for applications requiring high wear resistance, thermal stability, and chemical inertness. Common applications include cutting tools, aerospace components, and semiconductor devices.
- The ability to deposit coatings only a few microns thick ensures that the dimensions and tolerances of precision-engineered parts are maintained, which is critical in many industries.
In summary, the thickness of CVD coatings typically ranges from 5-10 microns, offering a balance between durability and precision. The slow deposition rate and chemical nature of the process result in high-quality, fine-grained coatings that are harder and more impervious than those produced by conventional methods. This makes CVD coatings highly suitable for demanding industrial applications where performance and longevity are critical.
Summary Table:
Aspect | Details |
---|---|
Typical Thickness | 5-10 microns |
Deposition Rate | A few hundred microns per hour |
Key Properties | Fine-grained, high purity, hard, impervious |
Comparison with PVD | PVD: 1-5 microns; CVD: Slightly thicker (5-10 microns) |
Applications | Cutting tools, aerospace components, semiconductor devices |
Benefits | High wear resistance, thermal stability, chemical inertness, and precision |
Interested in leveraging CVD coatings for your industrial needs? Contact us today for expert guidance!