Thin film physical vapor deposition (PVD) is a versatile technique used to create thin layers of material on substrates, with thicknesses ranging from fractions of a nanometer (monolayer) to several micrometers. The exact thickness depends on various factors, including deposition parameters, substrate characteristics, and the nature of the material being deposited. PVD processes, such as sputtering, involve transitioning materials from a condensed phase to a gas phase and then back to a condensed film phase. This method is environmentally friendly, produces high-purity coatings, and can significantly improve surface quality. The thickness of PVD thin films can be tailored to specific applications, making it a critical consideration for equipment and consumable purchasers.
Key Points Explained:
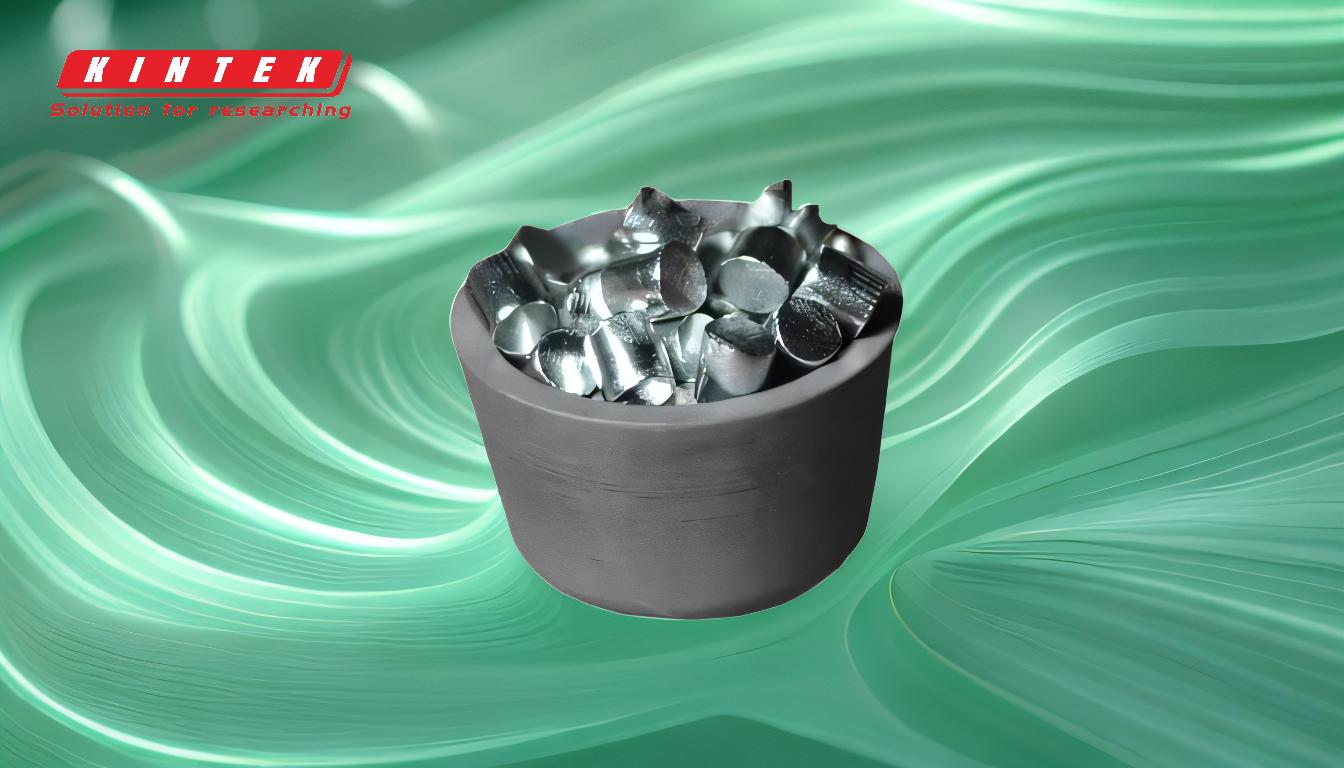
-
Definition of Thin Film Thickness in PVD:
- Thin films produced by PVD typically range in thickness from fractions of a nanometer (monolayer) to several micrometers.
- For example, a monolayer might be just a few atoms thick, while thicker films can reach up to 100 micrometers.
-
Factors Influencing Thin Film Thickness:
-
Deposition Parameters:
- The rate of deposition, duration of the process, and energy of the coating particles (ranging from tens to thousands of electron volts) directly affect the final thickness.
-
Material Properties:
- The mass of the material and its behavior during vaporization, migration, and deposition play a role in determining thickness.
-
Substrate and Environmental Conditions:
- The nature of the substrate, deposition temperature, and residual gas composition in the vacuum chamber can influence the growth and uniformity of the thin film.
-
Deposition Parameters:
-
Range of Thickness in PVD:
- PVD can produce films as thin as a few nanometers (e.g., for optical coatings or semiconductor applications) up to several microns (e.g., for wear-resistant coatings or decorative finishes).
- This wide range allows PVD to be used in diverse industries, from electronics to aerospace.
-
Comparison with Other Deposition Methods:
- PVD is often compared to chemical vapor deposition (CVD), which also produces thin films in a similar thickness range. However, PVD is typically preferred for applications requiring high-purity coatings and precise control over film properties.
-
Applications and Implications for Purchasers:
-
Optical Coatings:
- Thin films in the nanometer range are used for anti-reflective coatings, mirrors, and filters.
-
Semiconductor Devices:
- Ultra-thin films are critical for transistors, sensors, and integrated circuits.
-
Wear-Resistant and Decorative Coatings:
- Thicker films in the micrometer range are used for tools, automotive parts, and consumer goods.
-
Customization:
- Equipment and consumable purchasers must consider the specific thickness requirements for their applications when selecting PVD systems and materials.
-
Optical Coatings:
-
Advantages of PVD for Thin Film Deposition:
-
Environmental Friendliness:
- PVD processes do not involve harmful chemicals, making them eco-friendly.
-
High Purity:
- The coatings produced are free from contaminants, ensuring superior performance.
-
Surface Quality:
- PVD improves surface properties such as hardness, adhesion, and corrosion resistance.
-
Environmental Friendliness:
By understanding the factors influencing thin film thickness and the capabilities of PVD, purchasers can make informed decisions to meet their specific application needs.
Summary Table:
Aspect | Details |
---|---|
Thickness Range | Fractions of a nanometer (monolayer) to several micrometers (up to 100 µm). |
Key Influencing Factors | Deposition parameters, material properties, substrate, and environmental conditions. |
Applications | Optical coatings, semiconductor devices, wear-resistant coatings, decorative finishes. |
Advantages | Eco-friendly, high-purity coatings, improved surface quality. |
Need a PVD solution tailored to your specific requirements? Contact our experts today to learn more!