A single punch tablet press, also known as an eccentric or single station press, is a compact and straightforward machine used primarily in small-scale production or R&D settings. It operates using a single set of tooling, consisting of upper and lower punches and a die. The lower punch remains stationary while the upper punch applies compression force to form tablets. This process is akin to stamping due to its hammer-like motion. The machine is ideal for low-volume production, prototyping, and educational purposes due to its simplicity, ease of operation, and cost-effectiveness.
Key Points Explained:
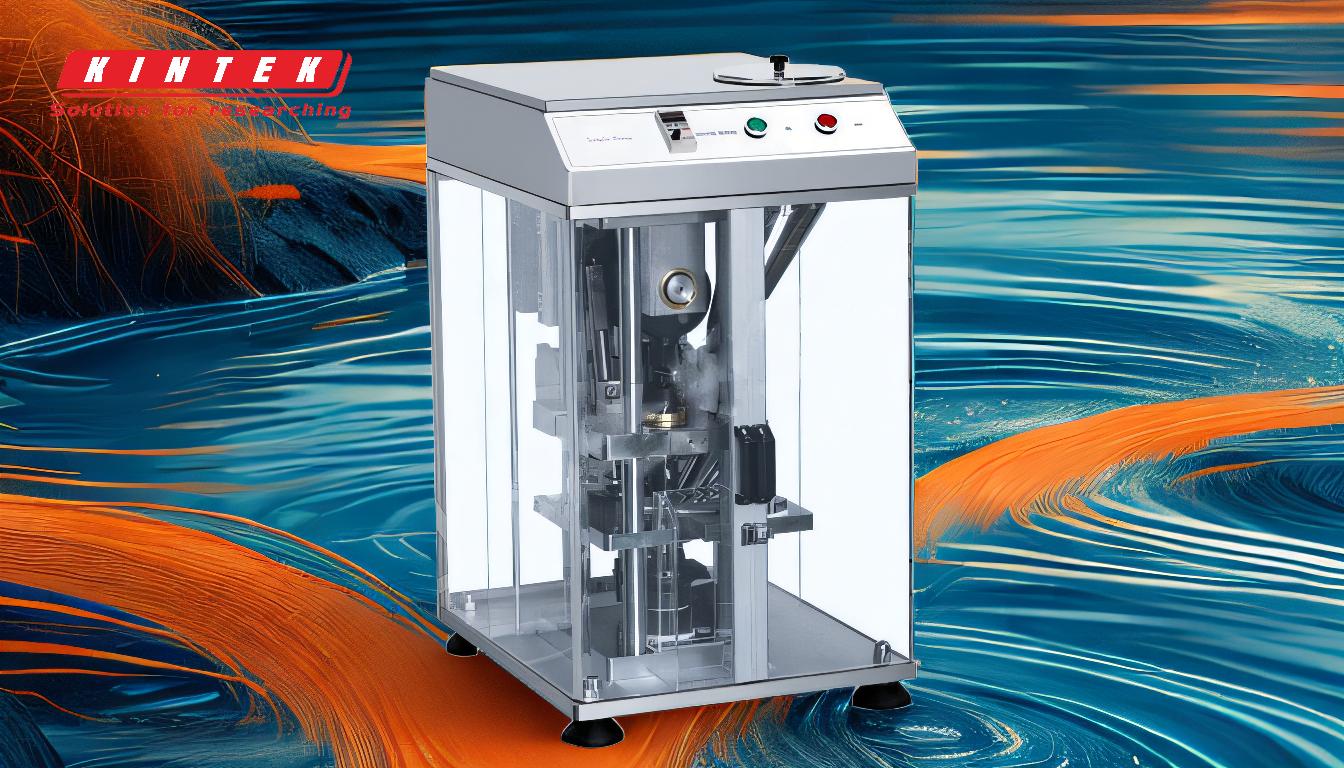
-
Basic Functionality:
- A single punch tablet press uses a single station of tooling, which includes an upper punch, a lower punch, and a die.
- The lower punch remains fixed, while the upper punch moves downward to compress the powder or granule material into a tablet.
- This process is often referred to as a stamping process because of its hammer-like motion.
-
Applications:
- Small-Scale Production: Ideal for producing small batches of tablets, making it suitable for pharmacies, small laboratories, or startups.
- Research and Development (R&D): Widely used in R&D settings for formulating and testing new tablet designs or compositions.
- Educational Purposes: Often used in academic institutions to teach students about tablet manufacturing processes.
- Prototyping: Perfect for creating sample tablets before scaling up to larger production machines.
-
Advantages:
- Simplicity: The machine is easy to operate and maintain, requiring minimal training.
- Cost-Effective: Lower initial investment compared to rotary tablet presses, making it accessible for small businesses or educational institutions.
- Compact Design: Takes up less space, ideal for environments with limited workspace.
- Versatility: Can produce a wide range of tablet shapes and sizes by changing the tooling.
-
Limitations:
- Low Production Capacity: Not suitable for high-volume production due to its single-station design.
- Manual Operation: Often requires manual feeding of materials, which can be time-consuming and less efficient for large-scale needs.
- Limited Automation: Lacks the advanced automation features found in rotary presses, such as continuous feeding and ejection systems.
-
Comparison with Rotary Tablet Presses:
- Single Punch Press: Best for small-scale, low-volume production with simpler designs and lower costs.
- Rotary Press: Designed for high-volume production with multiple stations, automated feeding, and higher efficiency.
-
Key Components:
- Upper Punch: Applies the compression force to form the tablet.
- Lower Punch: Remains stationary and supports the die during the compression process.
- Die: The cavity where the powder or granule material is compressed into the desired tablet shape.
-
Process Steps:
- Filling: The die cavity is filled with the powder or granule material.
- Compression: The upper punch moves downward to compress the material into a tablet.
- Ejection: The lower punch rises to eject the finished tablet from the die.
-
Maintenance and Care:
- Regular cleaning of the punches and die to prevent contamination.
- Lubrication of moving parts to ensure smooth operation.
- Periodic inspection of tooling for wear and tear to maintain tablet quality.
-
Future Trends:
- Integration of basic automation features to improve efficiency.
- Development of more durable and precise tooling materials.
- Increased use in niche markets, such as personalized medicine or specialized compounding pharmacies.
In summary, the single punch tablet press is a versatile and cost-effective solution for low-volume tablet production, R&D, and educational purposes. While it has limitations in terms of production capacity and automation, its simplicity and affordability make it an essential tool in many settings.
Summary Table:
Aspect | Details |
---|---|
Applications | Small-scale production, R&D, prototyping, educational purposes |
Advantages | Simple, cost-effective, compact, versatile |
Limitations | Low production capacity, manual operation, limited automation |
Key Components | Upper punch, lower punch, die |
Process Steps | Filling, compression, ejection |
Maintenance | Regular cleaning, lubrication, periodic inspection |
Future Trends | Basic automation, durable tooling, niche market applications |
Looking for a reliable single punch tablet press? Contact us today to find the perfect solution for your needs!