Sputter coating is a versatile and widely used technique in various industries and scientific applications. It involves the deposition of thin films of material onto a substrate using a process called sputtering. This technique is essential for creating conductive coatings, preparing samples for microscopy, and producing thin films for advanced technologies. Sputter coating is particularly valuable in fields such as solar panel manufacturing, microelectronics, and materials science, where precise and uniform coatings are critical. The process relies on creating a plasma that ejects target material atoms, which then bond to the substrate, forming a thin, even layer. This method ensures strong atomic-level bonding and high-quality results.
Key Points Explained:
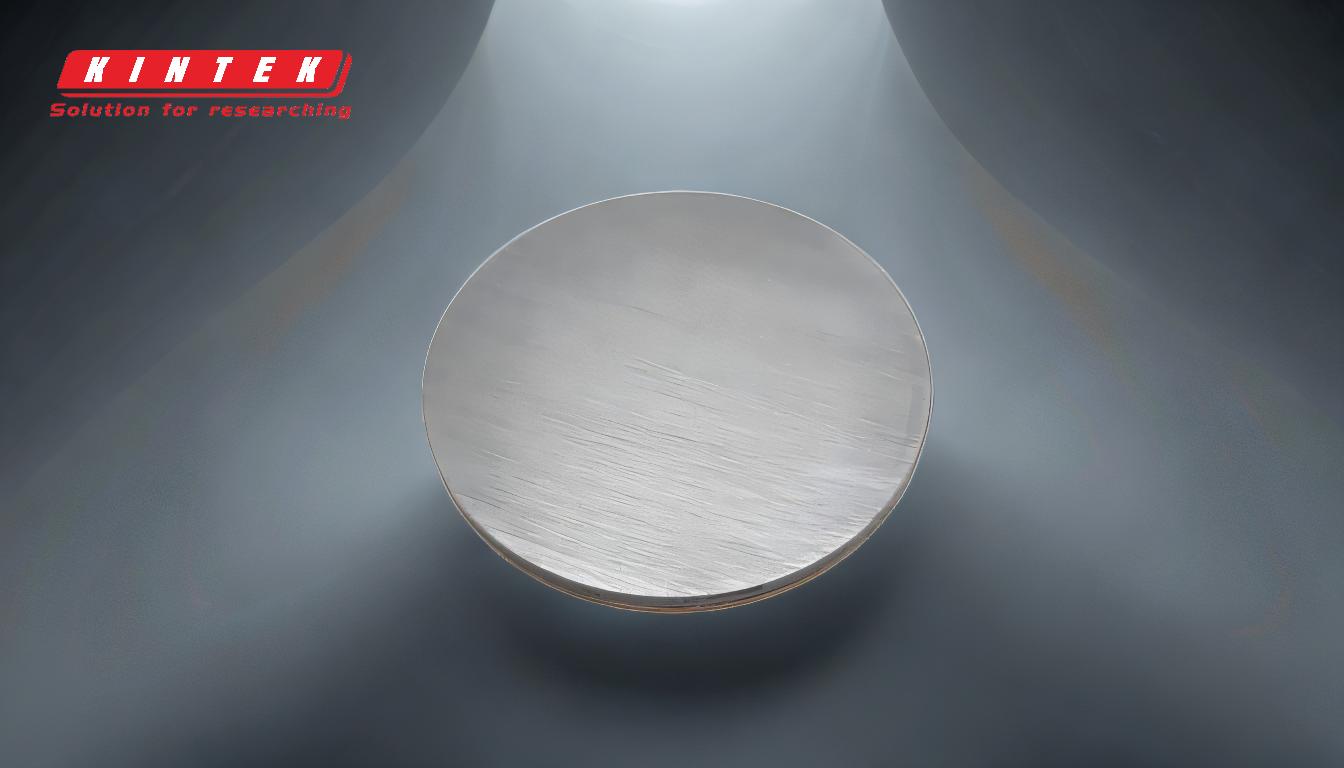
-
What is Sputter Coating?
- Sputter coating is a physical vapor deposition (PVD) process used to deposit thin films of material onto a substrate.
- It involves creating a plasma by electrically charging a sputtering cathode, which ejects atoms from a target material.
- These ejected atoms are directed toward the substrate, where they form a thin, uniform coating through momentum transfer.
-
How Does Sputter Coating Work?
- A high voltage is applied to the target material, creating a plasma consisting of gas atoms, free electrons, and positively charged ions.
- Magnetic fields concentrate the plasma, and energetic ions bombard the target, causing atoms to sputter off.
- The sputtered atoms travel through the vacuum chamber and deposit onto the substrate, forming a thin film.
- Key components include the vacuum chamber, target material, cooling systems, and magnetic fields to ensure stable and uniform erosion.
-
Applications of Sputter Coating:
- Electron Microscopy: Sputter coaters are essential in scanning electron microscopy (SEM) labs for preparing non-conductive samples. A thin conductive coating (e.g., gold or platinum) is applied to the sample to prevent charging and improve image quality.
- Solar Panels: Sputter coating is used to deposit thin films of materials like indium tin oxide (ITO) onto solar panels, enhancing their efficiency and conductivity.
- Microelectronics: It is widely used in the semiconductor industry to create thin films for integrated circuits, sensors, and other electronic components.
- Architectural Glass: Sputter coating is employed to apply reflective or low-emissivity coatings to glass, improving energy efficiency and aesthetics.
- Aerospace and Automotive Industries: Thin films produced by sputter coating are used for protective coatings, sensors, and advanced materials in these industries.
- Flat Panel Displays: Sputter coating is critical for depositing conductive and optical layers in displays, such as LCDs and OLEDs.
-
Advantages of Sputter Coating:
- Uniformity: The process produces highly uniform thin films, even on complex geometries.
- Versatility: It can deposit a wide range of materials, including metals, alloys, and ceramics.
- Strong Adhesion: The momentum transfer process ensures strong atomic-level bonding between the coating and substrate.
- High Purity: Sputter coating is performed in a vacuum, minimizing contamination and producing high-purity films.
- Scalability: It is suitable for both small-scale laboratory applications and large-scale industrial production.
-
Key Components of a Sputter Coater:
- Vacuum Chamber: Provides a controlled environment to minimize contamination and ensure consistent results.
- Target Material: The material to be deposited, which is bonded or clamped to the cathode.
- Cooling Systems: Manage the heat generated during the sputtering process to maintain stability and prevent damage.
- Magnetic Fields: Enhance plasma concentration and ensure uniform erosion of the target material.
-
Challenges and Considerations:
- Heat Management: The sputtering process generates significant heat, requiring effective cooling systems.
- Cost: Sputter coating equipment and materials can be expensive, particularly for high-purity or specialized applications.
- Complexity: The process requires precise control of parameters such as voltage, pressure, and temperature to achieve desired results.
In summary, sputter coating is a critical technology with diverse applications across industries. Its ability to produce high-quality, uniform thin films makes it indispensable for advancements in electronics, energy, and materials science. Understanding its principles, advantages, and challenges is essential for leveraging its full potential in various applications.
Summary Table:
Aspect | Details |
---|---|
Process | Physical vapor deposition (PVD) using plasma to eject target material atoms. |
Applications | Electron microscopy, solar panels, microelectronics, architectural glass. |
Advantages | Uniformity, versatility, strong adhesion, high purity, scalability. |
Key Components | Vacuum chamber, target material, cooling systems, magnetic fields. |
Challenges | Heat management, cost, complexity. |
Discover how sputter coating can enhance your projects—contact our experts today for tailored solutions!