Sputtering deposition is a versatile and widely used technique in various industries for depositing thin films on substrates. It involves the ejection of atoms from a target material due to bombardment by high-energy particles, which then deposit onto a substrate to form a thin film. This process is conducted in a vacuum environment to ensure purity and precision. Sputtering deposition is utilized in numerous applications, including semiconductor manufacturing, optical coatings, magnetic storage media, and decorative finishes. Its ability to produce high-quality, uniform, and durable coatings makes it indispensable in modern technology and industrial processes.
Key Points Explained:
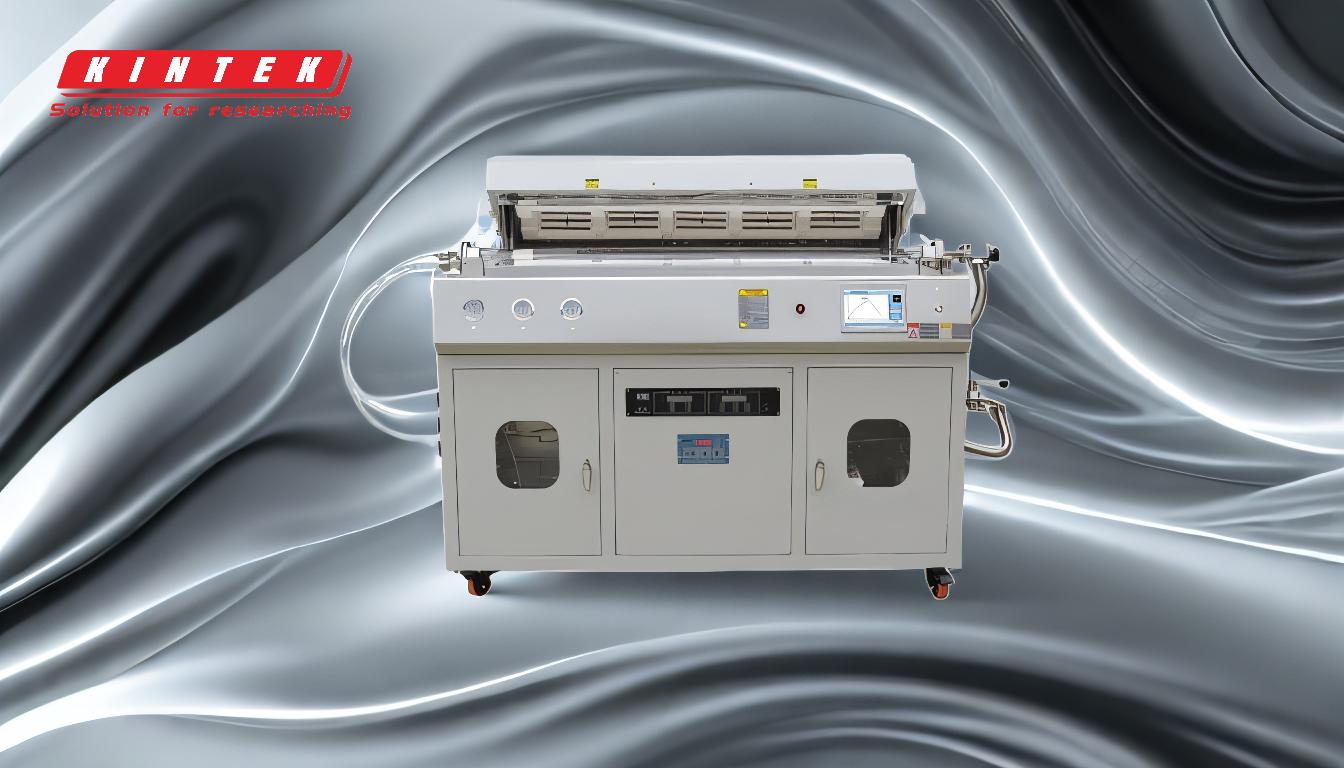
-
Semiconductor Industry:
- Thin Film Metallization: Sputtering deposition is crucial for depositing thin films of metals on semiconductor materials. These films are used for interconnects and contacts in integrated circuits (ICs), which are essential for the functionality of electronic devices.
- Contact Metals in Thin-Film Transistors: The process is also used to deposit contact metals in thin-film transistors (TFTs), which are key components in displays and other electronic devices.
-
Optical Coatings:
- Anti-Reflective Coatings: Sputtering is used to apply anti-reflective coatings on glass, which are essential for reducing glare and improving the efficiency of optical devices, such as lenses and solar panels.
- Low-Emissivity Coatings: These coatings are applied to architectural glass to improve energy efficiency by reflecting infrared light while allowing visible light to pass through.
-
Magnetic Storage Media:
- Hard Disks: Sputtering deposition is used in the production of computer hard disks, where it is employed to deposit magnetic films that store data. The precision and uniformity of the sputtering process are critical for the high-density data storage required in modern hard drives.
-
Wear-Resistant and Decorative Coatings:
- Tool Coatings: Sputtering is used to apply wear-resistant coatings, such as titanium nitride, on cutting tools. These coatings enhance the durability and performance of the tools, making them suitable for high-speed and high-precision machining.
- Decorative Coatings: The process is also used for applying decorative coatings on various materials, including metals and polymers, to enhance their aesthetic appeal.
-
Optical and Data Storage Media:
- CDs and DVDs: Sputtering deposition is used in the fabrication of CDs and DVDs, where it is employed to deposit the reflective and data-storage layers. The precision of the sputtering process ensures the high-quality and durability of these media.
- Optical Waveguides: The technique is also used in the production of optical waveguides, which are essential components in optical communication systems.
-
Photovoltaic Solar Cells:
- Thin Film Solar Cells: Sputtering is used to deposit thin films of materials, such as cadmium telluride (CdTe) or copper indium gallium selenide (CIGS), on substrates to create photovoltaic solar cells. These thin-film solar cells are lightweight, flexible, and cost-effective, making them suitable for a wide range of applications.
-
Surface Physics and Analysis:
- Surface Cleaning: Sputtering is used as a cleaning method in surface physics to prepare high-purity surfaces for analysis or further processing.
- Chemical Composition Analysis: The technique is also employed in surface analysis to determine the chemical composition of materials, which is crucial for quality control and research purposes.
-
Versatility and Precision:
- Alloy Deposition: Sputtering allows for the deposition of alloys in a single run, which is advantageous for creating complex material compositions with precise control over the film properties.
- Uniformity and Durability: The process is known for producing highly uniform and durable coatings, which are essential for applications requiring high performance and reliability.
In summary, sputtering deposition is a critical technology in modern manufacturing and research, offering unparalleled precision, versatility, and quality in the deposition of thin films across a wide range of applications.
Summary Table:
Application | Key Use Cases |
---|---|
Semiconductor Industry | Thin film metallization, contact metals in thin-film transistors (TFTs) |
Optical Coatings | Anti-reflective coatings, low-emissivity coatings for energy-efficient glass |
Magnetic Storage Media | Data storage layers in hard disks |
Wear-Resistant Coatings | Titanium nitride coatings for cutting tools |
Decorative Coatings | Aesthetic finishes on metals and polymers |
Optical & Data Storage | Reflective layers in CDs/DVDs, optical waveguides |
Photovoltaic Solar Cells | Thin-film solar cells (CdTe, CIGS) |
Surface Physics & Analysis | Surface cleaning, chemical composition analysis |
Versatility & Precision | Alloy deposition, uniform and durable coatings |
Interested in leveraging sputtering deposition for your projects? Contact us today to learn more!