The vacuum level in an e-beam evaporator is a critical factor that directly impacts the quality and purity of the thin film deposition process. A high vacuum environment, typically ranging from 10⁻⁷ to 10⁻⁵ mbar, is required to ensure minimal contamination, a high mean free path for evaporated particles, and precise control over the deposition process. This vacuum level allows the evaporated material to travel unimpeded to the substrate, resulting in high-purity coatings with excellent reflectivity and uniformity. The vacuum also prevents unwanted reactions with residual gases, ensuring the integrity of the deposited film. Below, the key points related to the vacuum level in e-beam evaporators are explained in detail.
Key Points Explained:
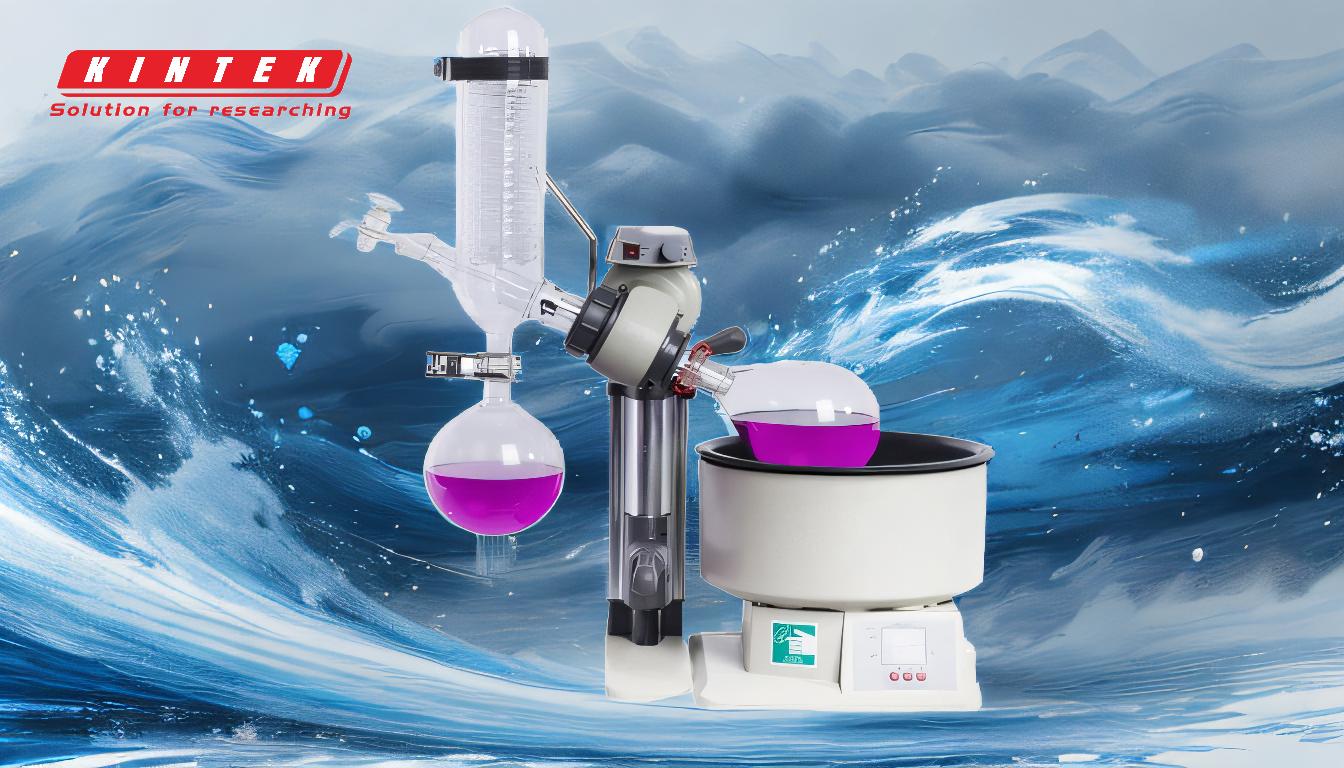
-
Vacuum Level Range (10⁻⁷ to 10⁻⁵ mbar)
- The vacuum level in e-beam evaporators typically operates within the range of 10⁻⁷ to 10⁻⁵ mbar. This high vacuum is essential to create an environment where the mean free path of the evaporated particles is maximized.
- A higher vacuum (closer to 10⁻⁷ mbar) is often required for applications demanding ultra-high purity, such as in semiconductor or optical coatings. A slightly lower vacuum (closer to 10⁻⁵ mbar) may be sufficient for less critical applications.
- The specific vacuum level depends on the size of the vacuum chamber, the material being evaporated, and the desired quality of the deposited layer.
-
Importance of High Vacuum for Mean Free Path
- The mean free path is the average distance a particle travels before colliding with another particle. In a high vacuum, the mean free path is significantly longer, ensuring that most evaporated particles reach the substrate without scattering or reacting with residual gases.
- This minimizes losses and ensures that the deposited film is uniform and free from contaminants, which is critical for achieving high-quality coatings.
-
Minimizing Contamination
- A high vacuum environment reduces the presence of residual gases, such as oxygen, nitrogen, and water vapor, which could otherwise react with the evaporated material or the substrate.
- Contamination can lead to defects, impurities, or altered properties in the deposited film, which is particularly detrimental in applications like semiconductor manufacturing or optical coatings.
- The vacuum ensures a cleaner and more controlled deposition process, preserving the purity and integrity of the thin film.
-
Role in Thermal Evaporation
- In e-beam evaporation, the electron beam generates intense heat, melting and evaporating the source material. The evaporated particles then travel through the vacuum chamber to the substrate.
- The high vacuum ensures that the evaporated material remains in a vapor state and does not condense prematurely or interact with other particles before reaching the substrate.
- This process results in thin films with thicknesses typically ranging from 5 to 250 nanometers, depending on the application.
-
Impact on Deposition Rate and Film Quality
- The vacuum level directly influences the deposition rate and the quality of the deposited film. A stable and high vacuum ensures consistent evaporation rates, which are crucial for achieving the desired film thickness and uniformity.
- Quartz crystal microbalances are often used to monitor and regulate the deposition rate, ensuring precise control over the process.
- Any fluctuation in the vacuum level can lead to variations in film thickness, defects, or reduced reflectivity, which are undesirable in high-precision applications.
-
Applications Requiring High Vacuum
- High vacuum levels are particularly important in industries such as:
- Semiconductors: For depositing high-purity conductive or insulating layers.
- Optics: For creating reflective or anti-reflective coatings with precise optical properties.
- Research and Development: For experimental thin films requiring ultra-high purity and precise control.
- In these applications, even minor contamination or deviations in vacuum levels can compromise the performance of the final product.
- High vacuum levels are particularly important in industries such as:
-
Chamber Size and Vacuum Requirements
- The size of the vacuum chamber affects the achievable vacuum level. Larger chambers may require more powerful vacuum pumps to maintain the desired vacuum range.
- The vacuum system typically includes components such as turbomolecular pumps, cryopumps, or diffusion pumps to achieve and maintain the required vacuum level.
- Regular maintenance and calibration of the vacuum system are essential to ensure consistent performance and avoid contamination.
In summary, the vacuum level in an e-beam evaporator is a critical parameter that ensures the success of the thin film deposition process. By maintaining a high vacuum (10⁻⁷ to 10⁻⁵ mbar), the system minimizes contamination, maximizes the mean free path of evaporated particles, and enables precise control over the deposition rate and film quality. This is essential for producing high-purity, uniform coatings in applications ranging from semiconductors to optics.
Summary Table:
Key Factor | Details |
---|---|
Vacuum Level Range | 10⁻⁷ to 10⁻⁵ mbar, depending on application requirements. |
Mean Free Path | Maximized in high vacuum, ensuring particles reach the substrate unimpeded. |
Contamination Prevention | Reduces residual gases, preserving film purity and integrity. |
Deposition Rate & Quality | Stable vacuum ensures consistent film thickness and uniformity. |
Applications | Semiconductors, optics, and R&D require ultra-high vacuum for precision. |
Achieve flawless thin film deposition with the right vacuum setup—contact our experts today!