Plasma Enhanced Chemical Vapor Deposition (PECVD) is a thin-film deposition technique that utilizes plasma to enhance chemical reactions at relatively low temperatures. This process involves introducing reactant gases between parallel electrodes, where plasma is generated to induce chemical reactions. The reaction products are then deposited onto a substrate, typically at temperatures around 350°C. PECVD is known for its high deposition rates, uniformity, and ability to produce high-quality films, making it a cost-effective and reliable method for applications such as hard masking, protective layers, and MEMS-specific processes.
Key Points Explained:
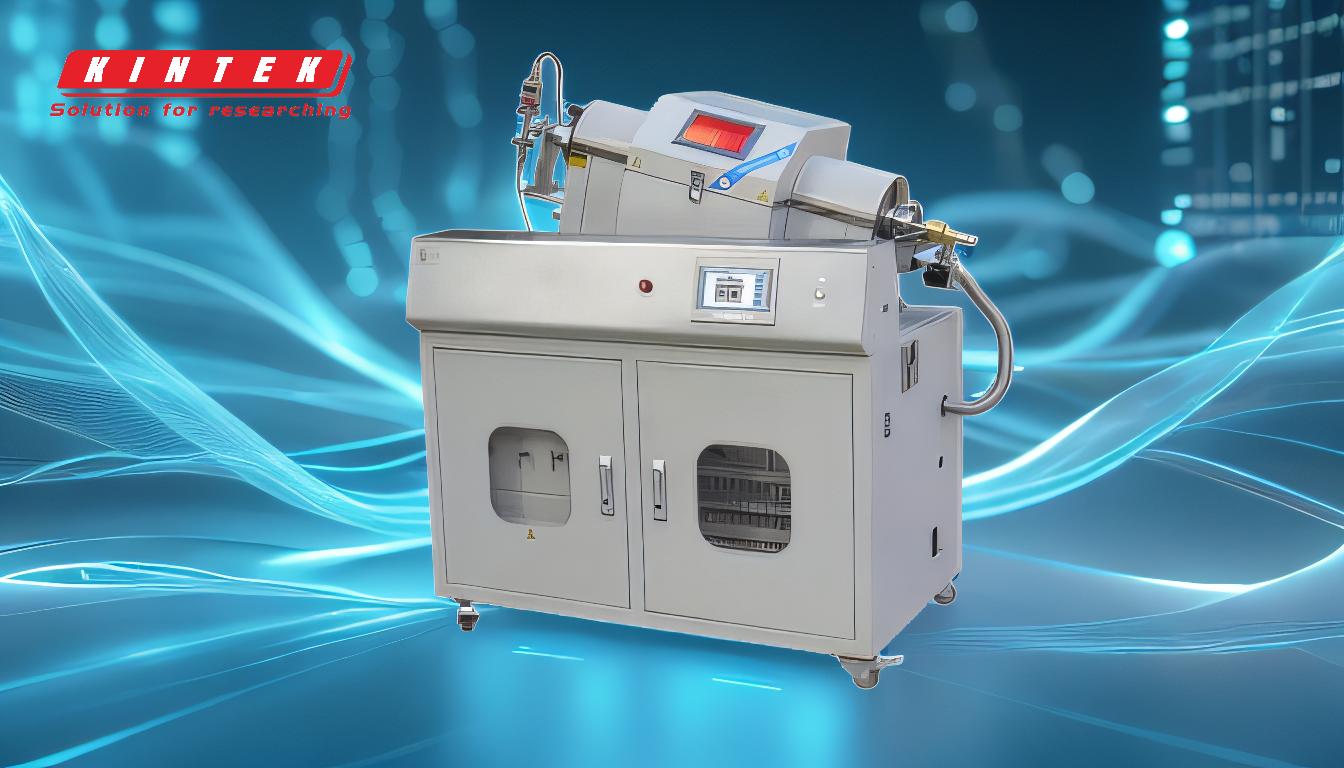
-
Introduction of Reactant Gases:
PECVD begins by introducing reactant gases into a chamber containing parallel electrodes. These gases are typically precursors for the desired thin-film material. The gases flow between the electrodes, creating an environment where chemical reactions can occur. -
Plasma Generation:
A plasma is generated by applying a high-frequency electric field between the electrodes. This plasma consists of ionized gas molecules, free electrons, and other reactive species. The plasma enhances the chemical reactions by providing energy to break down the reactant gases into reactive fragments. -
Chemical Reactions and Deposition:
The reactive fragments created by the plasma undergo chemical reactions, forming the desired thin-film material. These reaction products are then deposited onto the substrate, which is placed on one of the electrodes. The deposition occurs at relatively low temperatures (around 350°C), making PECVD suitable for temperature-sensitive substrates. -
Advantages of PECVD:
- High Deposition Rates: PECVD offers significantly higher deposition rates compared to traditional vacuum-based techniques, reducing fabrication time and costs.
- Uniformity: The process ensures uniform deposition of thin films, which is critical for applications requiring consistent layer thickness.
- Low-Temperature Processing: The ability to deposit films at low temperatures makes PECVD compatible with a wide range of substrates, including those that cannot withstand high temperatures.
- Ease of Cleaning: The chamber used in PECVD is easier to clean compared to other deposition methods, reducing downtime and maintenance costs.
-
Applications of PECVD:
PECVD is widely used in various industries for applications such as:- Hard Masking: Creating durable masks for etching processes.
- Sacrificial Layers: Forming temporary layers that are later removed.
- Protective and Passivation Layers: Providing protection against environmental factors and enhancing device reliability.
- MEMS-Specific Processes: Enabling the fabrication of microelectromechanical systems with precise control over film properties.
-
Comparison with Other Techniques:
- PECVD vs. CVD: PECVD operates at lower temperatures and produces higher-quality films with reduced likelihood of cracking compared to traditional Chemical Vapor Deposition (CVD).
- PECVD vs. LPCVD: While PECVD films are less flexible than those produced by Low-Pressure Chemical Vapor Deposition (LPCVD), PECVD offers higher deposition rates and is more suitable for temperature-sensitive substrates.
By leveraging plasma to enhance chemical reactions, PECVD provides a versatile and efficient method for depositing high-quality thin films, making it a cornerstone technology in modern fabrication processes.
Summary Table:
Key Aspect | Details |
---|---|
Reactant Gases | Introduced into a chamber with parallel electrodes for chemical reactions. |
Plasma Generation | High-frequency electric field creates plasma, breaking gases into fragments. |
Deposition Process | Reactive fragments form thin films on substrates at ~350°C. |
Advantages | High deposition rates, uniformity, low-temperature processing, easy cleaning. |
Applications | Hard masking, sacrificial layers, protective coatings, MEMS fabrication. |
Comparison | Lower temp than CVD, higher rates than LPCVD, ideal for sensitive substrates. |
Discover how PECVD can revolutionize your fabrication process—contact our experts today for more details!